Laser Safety Curtain System Kits
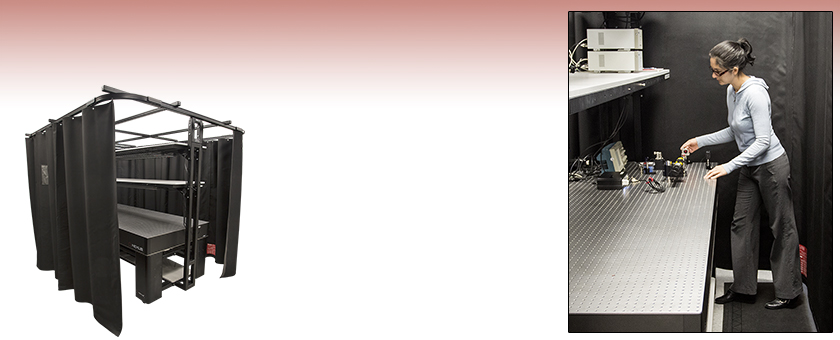
- Laser Curtains and Mounting Hardware Included
- Floor-Length Curtains Form Enclosed Workspace
- Continuous, Uninterrupted Curtain Track for Effort-Free Gliding
TFL1225N
Laser Curtain Kit
(Shown Mounted to the TFS251 Overhead Shelf on a TF1225A7 Nexus® Optical Table Frame)
Floor-length laser curtains are provided to enclose the table. Select kits are designed to provide a walkway between the table and curtains, allowing for work to continue while the curtain is closed.

Please Wait
Laser Curtain Kits Compatibility | |||
---|---|---|---|
No Walkway | TFL1020 | TFL1220 | TFL1225 |
Partial Walkway | TFL1020N | TFL1220N | TFL1225N |
Complete Walkway | TFL1020W | TFL1220W | TFL1225W |
Nexus Table Framesa,b | TF1020A7 or TF1020R7 with TFS201 |
TF1220A7, TF1220R7, or TF1220A6 with TFS201 |
TF1225A7, TF1225R7, or TF1225A6 with TFS251 |
Free-Standing Overhead Shelving Unit |
PTA280 | PTA280 | PTA281 |
Features
- Laser Curtain Kits Designed for Thorlabs' Optical Table Workstations and Free-Standing Shelving Units
- Workstation Requires an Overhead Shelving Unit to Attach the Curtain Kit
- Versions with and without Work Space Between the Optical Table and Curtains
- Flame Retardant, Floor-Length Laser Curtains with Magnetic Connectors for Light-Tight Seals are Included
- Includes All Components Needed to Mount the Kit
- Curtain End Stops Available to Provide a Hard Stop Along Tracks
- Replacement Wheel Runners and T-Nuts Sold Below
- Adapter Kit for Mounting to Legacy Workstations and Free-Standing Shelves Available
- Laser Safety Valance Panel and Mounting Kit Available Separately Below
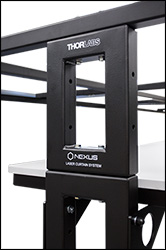
Click to Enlarge
Kits Attach Directly to Our Free-Standing Shelves or Our Nexus Workstation's Overhead Shelves
(Upgrade Kit Available for Workstations and Shelving Purchased Prior to March 2017)
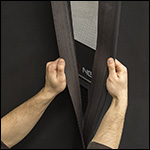
Click to Enlarge
Magnetic Strips are Used to Connect Curtains for a Light-Tight Seal
Laser Safety Accessories |
---|
Modular Laser Curtain System |
Laser Curtain Kits |
Laser Glasses |
Laser Signs |
Beam Blocks/Traps |
Beam Shutters |
Aluminum Protective Screens |
Blackout Materials |
Thorlabs' Laser Curtain Kits include all components needed to mount laser curtains to a
Nexus® Optical Table Workstation Frame that has an overhead shelving unit installed or directly to our Free-Standing Shelves. Kits that fully enclose a 1 m x 2 m, 1.2 m x 2 m, or 1.2 m x 2.5 m optical table are available. See the table to the right for complete compatibility information.
Each kit provides approximately 2.2 m (7.2') of overhead clearance when mounted, has continuous tracking for uninterrupted movement of the curtains, and includes enough laser safety curtains to fully enclose the optical table. All laser safety curtains are floor length, flame retardant, 2.1 m (7.0') long, and include magnetic connectors for light-tight seals. Kits with item numbers ending in 'N' or 'W' are designed with a walkway between the optical table and curtain; see the drawings below for details. This additional space allows for work to continue while the laser curtains remain closed.
All laser safety curtains are certified to EN 12254:2010(E)*; certification levels can be found in the Certifications tab. Each curtain is made using a rubber compound fabric and includes a 380 mm x 280 mm document pocket on the front of the curtain. The back of the curtain includes the item #, safety compliance information, manufacturing date, and protection level information.
Curtain end stops as well as replacement wheel runners and T-nuts are also available below. End stops provide a hard stop for a laser safety curtain mounted on the track. A laser safety valance panel and associated hardware mountings kit are available separately below. The valance panel is designed to cover any gaps near the ceiling or the curtain tracks of a laser curtain kit.
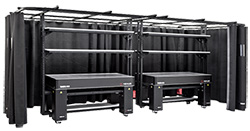
Click to Enlarge
Two Curtain Kits Connected to Enclose Two Tables
A Modular Laser Safety Curtain System that attaches to walls and ceilings is also available. This system features laser curtain panels, curtain tracks, track connectors, and mounting adapters that are each sold individually. The modular assembly imparts the ability to fully customize a system to fit most lab spaces using a standard system of components. Our laser curtain kits use many components from our modular system, including the laser curtains, curtain tracks, LPC01 track connectors, wheel runners, and T-nuts. All components from this modular system are fully compatible with our Laser Curtain Kits.
*DISCLAIMER
The curtain materials have been tested individually by a third party using EN specifications; see the Certifications tab for details. Due to manufacturing variances, mechanical wear, and laser damage, Thorlabs assumes no responsibility for laser curtain failure. Please consult your local laser safety specialist before purchasing to ensure that the curtain is suitable for your application. To minimize risk, inspect the curtain before each use and ensure that it is in excellent condition.
Laser Curtain Kit Options
The simplified drawings below display the amount of work space provided within each kit option. Each depicts a top view of a laser safety curtain kit overlaid on an optical table. The width of each walkway is indicated by X and Y. See the tables below for the exact amount of workspace provided along the long edge and short edge of the optical table by each kit. Once a laser curtain kit is installed, it can be altered to remove or add a walkway; contact Tech Support for more details.
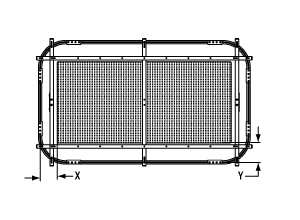
Click to Enlarge
No Walkway Around Table
TFL1x2x Curtain Frame Shown Above an Optical Table
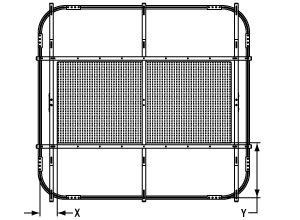
Click to Enlarge
Partial Walkway Around Table
TFL1x2xN Curtain Frame Shown Above an Optical Table
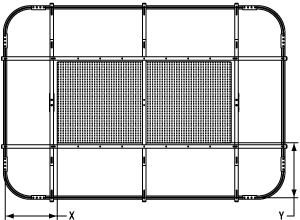
Click to Enlarge
Complete Walkway Around Table
TFL1x2xW Curtain Frame Shown Above an Optical Table
DISCLAIMER
The Laser Curtain materials have been tested by third parties using a variety of state regulations and EN specifications. Due to manufacturing variances, mechanical wear, and laser damage, Thorlabs assumes no responsibility for laser material failure. Please consult your local laser safety specialist before purchasing to ensure that the fabric is suitable for your application. To minimize risk, inspect the material before each use and ensure that it is in excellent condition.
EN Certificationa | ||||
---|---|---|---|---|
Certification Requirements | Test Parameters | Damage Threshold | Maximum Spectral Transmittance Ratio |
Certification Levela |
EN 12254: 2010 (E), 180 - 315 nm Range | 266 nm, 3 ns Pulses (FWHM), 50 kHz | 1 x 107 W/m2 | 1 x 10-10 | D AB10 |
EN 12254: 2010 (E), 180 - 315 nm Range | 266 nm, 240 ms Pulses (FWHM), 10 Hz | 3 x 106 J/m2 | 1 x 10-5 | I AB5 |
EN 12254: 2010 (E), 180 - 315 nm Range | 266 nm, 5 ns Pulses (FWHM), 10 Hz | 3 x 105 J/m2 | 1 x 10-4 | R AB4 |
EN 12254: 2010 (E), 180 - 315 nm Range | 266 nm, 800 ps Pulses (FWHM), 20 Hz | 3 x 1014 J/m2 | 1 x 10-4 | M AB4 |
EN 12254: 2010 (E), 315 - 1050 nm Range | 532 nm (CW) | 1 x 107 W/m2 | 1 x 10-7 | D AB7 |
EN 12254: 2010 (E), 315 - 1400 nm Range | 1064 nm / 532 nm, 10 ns Pulses (Square), 5 Hz | 5 x 103 J/m2 | 1 x 10-6 | R AB6 |
EN 12254: 2010 (E), 315 - 1400 nm Range | 1064 nm, 300 µs Pulses (Square), 20 Hz | 5 x 105 J/m2 | 1 x 10-8 | I AB8 |
EN 12254: 2010 (E), 315 - 1400 nm Range | 1064 nm / 532 nm, 500 ps / 400 ps Pulses (Square), 20 Hz | 1.5 x 104 J/m2 | 1 x 10-8 | M AB8 |
EN 12254: 2010 (E), 1050 - 1400 nm Range | 1070 nm (CW) | 2.5 x 106 W/m2 | 1 x 10-5 | D AB5 |
EN 12254: 2010 (E), 1400 - 10 600 nm Range | 10.6 µm (CW) | 1 x 107 W/m2 | 1 x 10-4 | D AB4 |
EN 12254: 2010 (E), 1400 - 10 600 nm Range | 10.6 µm, 100 ms Pulses (Square), 10 Hz | 1 x 107 J/m2 | 1 x 10-5 | I AB5 |
EN 12254: 2010 (E), 1400 - 10 600 nm Range | 10.6 µm, 100 ns Pulses (Square), 1 Hz | 1 x 104 J/m2 | 1 x 10-2 | R AB2 |
Other EN Certificationsa | |||
---|---|---|---|
Certification Type | Test Wavelength | Pulsewidth (FWHM) | Comments |
Mechanical Strength | N/A | N/A | UV-Exposed Protected Fabric. All samples meet requirement. |
Resistance to Ignition | N/A | N/A | Flame does not reach the test mark with the burner in position, and self-extinguishes after removal of the burner. Material does not continue to glow for more than one second after removal of the burner. |
Spectral Transmittance | 200 nm - 50 000 nm | N/A | Samples do not exhibit transmission windows from 200 nm to 50 000 nm. |
Stability to Temperature | Various | Various | No degradation was observed in any AB level for any sample. |
Stability to UV Radiation | All | 10 ns - 20 ns | Samples do not exhibit any cracking, peeling, or degradation. For laser wavelengths, samples do not exceed maximum spectral transmission for scale number. Samples maintained optical density using both laser and spectrophotometer. |
Additional Certifications | |
---|---|
Certification Requirements | Comments |
Boston Fire Department Classification Fire Test: BFD IX-1 |
After flame does exceed two seconds; flame propogation and after flame does not extend beyond six inches from the bottom edge. Propagating afterglow does not exceed forty seconds; non-propogating afterglow in the charred area does not exceed eighty seconds. |
California Administrative Code Title 19: Public Safety, Section 1237 |
The char length did not exceed 6.0 inches, and the average afterflame time did not exceed 4.0 seconds in length or width directions. |
NFPA No. 701 Standard Methods of Fire Test for Flame Propogation of Textiles and Films, 2019 Edition, (Test 1)a | The average percent weight loss does not exceed 40% and the average residual flame does not exceed 2.0 seconds. |
NYC Cal. No. 294-40-SR | No flashing occured at any time, and the average continuation of flaming did not exceed three seconds. The average continuation of glow at the edge of the charred area did not exceed twenty seconds after the cessation of flaming. |
Laser Safety Valance Certifications
DISCLAIMER
These Laser Valance materials have been tested by third parties using a variety of state regulations and EN specifications. Due to manufacturing variances, mechanical wear, and laser damage, Thorlabs assumes no responsibility for laser material failure. Please consult your local laser safety specialist before purchasing to ensure that the fabric is suitable for your application. To minimize risk, inspect the material before each use and ensure that it is in excellent condition.
EN Certificationa | ||||
---|---|---|---|---|
Certification Requirements | Test Parameters | Damage Threshold | Maximum Spectral Transmittance Ratio |
Certification Levela |
EN 12254: 2010 (E), 180 - 315 nm Range | 266 nm (CW) | 1 x 107 W/m2 | 1 x 10-10 | D AB10 |
EN 12254: 2010 (E), 180 - 315 nm Range | 266 nm, 45 ms Pulses (FWHM), 10 Hz | 3 x 106 J/m2 | 1 x 10-5 | I AB5 |
EN 12254: 2010 (E), 180 - 315 nm Range | 266 nm, 5 ns Pulses (FWHM), 10 Hz | 3 x 105 J/m2 | 1 x 10-4 | R AB4 |
EN 12254: 2010 (E), 180 - 315 nm Range | 266 nm, 500 ps Pulses (FWHM), 20 Hz | 3 x 1012 J/m2 | 1 x 10-2 | M AB2 |
EN 12254: 2010 (E), 315 - 1050 nm Range | 532 nm (CW) | 1 x 107 W/m2 | 1 x 10-7 | D AB7 |
EN 12254: 2010 (E), 315 - 1400 nm Range | 1064 nm, 2 ms Pulses (Square), 20 Hz | 5 x 104 J/m2 | 1 x 10-7 | R AB7 |
EN 12254: 2010 (E), 315 - 1400 nm Range | 1064 nm, 3 ms Pulses (Square), 10 Hz | 5 x 105 J/m2 | 1 x 10-8 | I AB8 |
EN 12254: 2010 (E), 315 - 1400 nm Range | 1064 nm, 500 ps Pulses (Square), 20 Hz | 1.5 x 104 J/m2 | 1 x 10-5 | M AB8 |
EN 12254: 2010 (E), 1050 - 1400 nm Range | 1070 nm (CW) | 2.5 x 106 W/m2 | 1 x 10-5 | D AB5 |
EN 12254: 2010 (E), 1400 - 10 600 nm Range | 10.6 µm (CW) | 1 x 106 W/m2 | 1 x 10-3 | D AB3 |
EN 12254: 2010 (E), 1400 - 10 600 nm Range | 10.6 µm, 3 ms Pulses (Square), 10 Hz | 1 x 106 J/m2 | 1 x 10-4 | I AB4 |
EN 12254: 2010 (E), 1400 - 10 600 nm Range | 10.6 µm, 100 ns Pulses (Square), 1 Hz | 1 x 104 J/m2 | 1 x 10-2 | R AB2 |
Other EN Certificationsa | |||
---|---|---|---|
Certification Type | Test Wavelength |
Pulsewidth (FWHM) |
Comments |
Mechanical Strength | N/A | N/A | UV-Exposed Protected Fabric. All samples meet requirement. |
Resistance to Ignition | N/A | N/A | Flame does not reach the test mark with the burner in position, and self-extinguishes after removal of the burner. Material does not continue to glow for more than one second after removal of the burner. |
Spectral Transmittance | 200 nm - 50 000 nm | N/A | Samples do not exhibit transmission windows from 200 nm to 50 000 nm. |
Stability to Temperature | Various | Various | No degradation was observed in any AB level for any sample. |
Stability to UV Radiation | All | 10 ns - 20 ns | Samples do not exhibit any cracking, peeling, or degradation. For laser wavelengths, samples do not exceed maximum spectral transmission for scale number. Samples maintained optical density using both laser and spectrophotometer. |
Each kit requires an Overhead Shelving Unit or Free-Standing Overhead Shelf for assembly. | ||
![]() |
- Or - | ![]() |
Laser Safety Curtain Kit Assembly
The animation below provides a simplified illustration of how the TFL1020 Curtain Kit is installed onto a TFS201 Overhead Shelf that was mounted onto a TF1020A7 Nexus® Table Frame. The steps in the assembly process are the same when mounting a kit onto a free-standing shelving unit. Enough laser curtains are included with each kit to fully enclose the optical table.
The animation shows the curtain kits being attached to the table frame using our TFLA01 adapter kit, which is needed to attach the kit to legacy shelving units. Our current shelving units (sold approximately after March 2017) have two Ø10 mm through holes in the top bar of each shelf support that allow the curtain kit to be directly connected using the included M8 bolts, without the use of the TFLA01. See the bottom of the page for details. Note that installing the curtain kit using the TFLA01 requires temporarily removing some of the screws that support the overhead shelf, so be sure that the shelf and optical table are empty before beginning the curtain installation.
Complete assembly instructions are provided in the manual for each curtain kit, which can be accessed by clicking on the red Docs icon () next to the item number below.
Laser Safety and Classification
Safe practices and proper usage of safety equipment should be taken into consideration when operating lasers. The eye is susceptible to injury, even from very low levels of laser light. Thorlabs offers a range of laser safety accessories that can be used to reduce the risk of accidents or injuries. Laser emission in the visible and near infrared spectral ranges has the greatest potential for retinal injury, as the cornea and lens are transparent to those wavelengths, and the lens can focus the laser energy onto the retina.
Safe Practices and Light Safety Accessories
- Laser safety eyewear must be worn whenever working with Class 3 or 4 lasers.
- Regardless of laser class, Thorlabs recommends the use of laser safety eyewear whenever working with laser beams with non-negligible powers, since metallic tools such as screwdrivers can accidentally redirect a beam.
- Laser goggles designed for specific wavelengths should be clearly available near laser setups to protect the wearer from unintentional laser reflections.
- Goggles are marked with the wavelength range over which protection is afforded and the minimum optical density within that range.
- Laser Safety Curtains and Laser Safety Fabric shield other parts of the lab from high energy lasers.
- Blackout Materials can prevent direct or reflected light from leaving the experimental setup area.
- Thorlabs' Enclosure Systems can be used to contain optical setups to isolate or minimize laser hazards.
- A fiber-pigtailed laser should always be turned off before connecting it to or disconnecting it from another fiber, especially when the laser is at power levels above 10 mW.
- All beams should be terminated at the edge of the table, and laboratory doors should be closed whenever a laser is in use.
- Do not place laser beams at eye level.
- Carry out experiments on an optical table such that all laser beams travel horizontally.
- Remove unnecessary reflective items such as reflective jewelry (e.g., rings, watches, etc.) while working near the beam path.
- Be aware that lenses and other optical devices may reflect a portion of the incident beam from the front or rear surface.
- Operate a laser at the minimum power necessary for any operation.
- If possible, reduce the output power of a laser during alignment procedures.
- Use beam shutters and filters to reduce the beam power.
- Post appropriate warning signs or labels near laser setups or rooms.
- Use a laser sign with a lightbox if operating Class 3R or 4 lasers (i.e., lasers requiring the use of a safety interlock).
- Do not use Laser Viewing Cards in place of a proper Beam Trap.
Laser Classification
Lasers are categorized into different classes according to their ability to cause eye and other damage. The International Electrotechnical Commission (IEC) is a global organization that prepares and publishes international standards for all electrical, electronic, and related technologies. The IEC document 60825-1 outlines the safety of laser products. A description of each class of laser is given below:
Class | Description | Warning Label |
---|---|---|
1 | This class of laser is safe under all conditions of normal use, including use with optical instruments for intrabeam viewing. Lasers in this class do not emit radiation at levels that may cause injury during normal operation, and therefore the maximum permissible exposure (MPE) cannot be exceeded. Class 1 lasers can also include enclosed, high-power lasers where exposure to the radiation is not possible without opening or shutting down the laser. | ![]() |
1M | Class 1M lasers are safe except when used in conjunction with optical components such as telescopes and microscopes. Lasers belonging to this class emit large-diameter or divergent beams, and the MPE cannot normally be exceeded unless focusing or imaging optics are used to narrow the beam. However, if the beam is refocused, the hazard may be increased and the class may be changed accordingly. | ![]() |
2 | Class 2 lasers, which are limited to 1 mW of visible continuous-wave radiation, are safe because the blink reflex will limit the exposure in the eye to 0.25 seconds. This category only applies to visible radiation (400 - 700 nm). | ![]() |
2M | Because of the blink reflex, this class of laser is classified as safe as long as the beam is not viewed through optical instruments. This laser class also applies to larger-diameter or diverging laser beams. | ![]() |
3R | Class 3R lasers produce visible and invisible light that is hazardous under direct and specular-reflection viewing conditions. Eye injuries may occur if you directly view the beam, especially when using optical instruments. Lasers in this class are considered safe as long as they are handled with restricted beam viewing. The MPE can be exceeded with this class of laser; however, this presents a low risk level to injury. Visible, continuous-wave lasers in this class are limited to 5 mW of output power. | ![]() |
3B | Class 3B lasers are hazardous to the eye if exposed directly. Diffuse reflections are usually not harmful, but may be when using higher-power Class 3B lasers. Safe handling of devices in this class includes wearing protective eyewear where direct viewing of the laser beam may occur. Lasers of this class must be equipped with a key switch and a safety interlock; moreover, laser safety signs should be used, such that the laser cannot be used without the safety light turning on. Laser products with power output near the upper range of Class 3B may also cause skin burns. | ![]() |
4 | This class of laser may cause damage to the skin, and also to the eye, even from the viewing of diffuse reflections. These hazards may also apply to indirect or non-specular reflections of the beam, even from apparently matte surfaces. Great care must be taken when handling these lasers. They also represent a fire risk, because they may ignite combustible material. Class 4 lasers must be equipped with a key switch and a safety interlock. | ![]() |
All class 2 lasers (and higher) must display, in addition to the corresponding sign above, this triangular warning sign. | ![]() |
Posted Comments: | |
dkleckner
 (posted 2018-12-11 11:34:04.783) Are your laser curtains for fire retardancy by the California State Fire Marshall? If not, do you have any plans to get them certified? AManickavasagam
 (posted 2018-12-13 11:03:25.0) Response from Arunthathi @ Thorlabs: The resistance to Ignition certification for our laser curtains have been tested and certified in accordance to EN:1598: 1997. If this does not meet your requirements please contact us directly with further details and we will look into this further. |

![]() |
- Or - | ![]() |
Laser Curtain Kit (Click for Drawing) |
TFL1020 (No Walkway) |
TFL1020N (Partial Walkway) |
TFL1020W (Complete Walkway) |
|||
---|---|---|---|---|---|---|
Space Between Curtain and Tablea |
X | Y | X | Y | X | Y |
1 m x 2 m Table | 181.0 mm (7.12") |
181.0 mm (7.12") |
181.0 mm (7.12") |
581.0 mm (22.87") |
581.0 mm (22.87") |
581.0 mm (22.87") |
3' x 6' Table | 266.6 mm (10.49") |
223.8 mm (8.81") |
266.6 mm (10.49") |
623.8 mm (24.56") |
666.6 mm (26.24") |
623.8 mm (24.56") |
- Designed to Enclose 1.0 m x 2.0 m (3' x 6') Optical Tables
- Attach Directly to an Optical Table Workstation with a TFS201 Overhead Shelving Unit
- Attach Directly to a PTA280 Free-Standing Overhead Shelving Unit
Kit Components
- Laser Safety Curtains:
- Laser Curtain Tracks, LPC01 Track Connectors, Wheel Runners, and T-Nuts
- Support Frame with Adapters to Attach to Nexus Frame or Free-Standing Shelf
- All Hardware Needed to Construct the Curtain System
- Required Hex Keys and Wrenches
For step-by-step instructions detailing how to assemble our Laser Safety Curtain Kits, please view the manual, which can be found by clicking the red docs icon () below. For additional support, please contact Tech Support. It is recommended that two people work together to assemble these kits. Legacy table frames purchased prior to approximately March 2017 require the TFLA01 Adapter Kit. See the bottom of the page for compatibility details.
Note that each system will ship in a 2.2 m x 1.5 m x 0.6 m (7.2' x 4.9' x 2.0') crate.

![]() |
- Or - | ![]() |
Laser Curtain Kit (Click for Drawing) |
TFL1220 (No Walkway) |
TFL1220N (Partial Walkway) |
TFL1220W (Complete Walkway) |
|||
---|---|---|---|---|---|---|
Space Between Curtain and Tablea |
X | Y | X | Y | X | Y |
1.2 m x 2 m Table | 181.0 mm (7.12") |
181.0 mm (7.12") |
181.0 mm (7.12") |
581.0 mm (22.87") |
581.0 mm (22.87") |
581.0 mm (22.87") |
4' x 6' Table | 266.6 mm (10.49") |
171.4 mm (6.75") |
266.6 mm (10.49") |
571.4 mm (22.49") |
666.6 mm (26.24") |
571.4 mm (22.49") |
- Designed to Enclose 1.2 m x 2.0 m (4' x 6') Optical Tables
- Attach Directly to an Optical Table Workstation with a TFS201 Overhead Shelving Unit
- Attach Directly to a PTA280 Free-Standing Overhead Shelving Unit
Kit Components
- Laser Safety Curtains:
- Laser Curtain Tracks, LPC01 Track Connectors, Wheel Runners, and T-Nuts
- Support Frame with Adapters to Attach to Nexus Frame or Free-Standing Shelf
- All Hardware Needed to Construct the Curtain System
- Required Hex Keys and Wrenches
For step-by-step instructions detailing how to assemble our Laser Safety Curtain Kits, please view the manual, which can be found by clicking the red docs icon () below. For additional support, please contact Tech Support. It is recommended that two people work together to assemble these kits. Legacy table frames purchased prior to approximately March 2017 require the TFLA01 Adapter Kit. See the bottom of the page for compatibility details.
Note that each system will ship in a 2.2 m x 1.5 m x 0.6 m (7.2' x 4.9' x 2.0') crate.

![]() |
- Or - | ![]() |
Laser Curtain Kit (Click for Drawing) |
TFL1225 (No Walkway) |
TFL1225N (Partial Walkway) |
TFL1225W (Complete Walkway) |
|||
---|---|---|---|---|---|---|
Space Between Curtain and Tablea |
X | Y | X | Y | X | Y |
1.2 m x 2.5 m Table | 231.0 mm (9.09") |
181.0 mm (7.12") |
231.0 mm (9.09") |
581.0 mm (22.87") |
631.0 mm (24.84") |
581.0 mm (22.87") |
4' x 8' Table | 261.8 mm (10.31") |
171.4 mm (6.75") |
261.8 mm (10.31") |
571.4 mm (22.49") |
661.8 mm (26.05") |
571.4 mm (22.49") |
- Designed to Enclose 1.2 m x 2.5 m (4' x 8') Optical Tables
- Attach Directly to an Optical Table Workstation with a TFS251 Overhead Shelving Unit
- Attach Directly to a PTA281 Free-Standing Overhead Shelving Unit
Kit Components
- Laser Safety Curtains:
- Laser Curtain Tracks, LPC01 Track Connectors, Wheel Runners, and T-Nuts
- Support Frame with Adapters to Attach to Nexus Frame or Free-Standing Shelf
- All Hardware Needed to Construct the Curtain System
- Required Hex Keys and Wrenches
For step-by-step instructions detailing how to assemble our Laser Safety Curtain Kits, please view the manual, which can be found by clicking the red docs icon () below. For additional support, please contact Tech Support. It is recommended that two people work together to assemble these kits. Legacy table frames purchased prior to approximately March 2017 require the TFLA01 Adapter Kit. See the bottom of the page for compatibility details.
Note that each system will ship in a crate that is approximately 2.82 m x 1.5 m x 0.85 m (9.2' x 4.9' x 2.8').

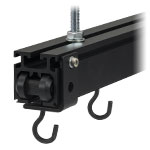
Click to Enlarge
End Stop Shown Attached to the Side of a Curtain Track to Stop the Movement of the Wheel Runners
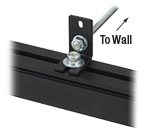
Click to Enlarge
The LPC05 shown attached to the top of a track with an LPC02 to create a horizontal restraint that prevents swaying of the system.
Included Hardware |
---|
M4 Cap Screw (x2) |
M4 Drop-In T-Nut (x2) |
M4 Washer (x2) |
- Provides a Hard Stop for Curtain Panels
- Attaches to the Side Channels of the Curtain Track Using the Provided M4 Cap Screw and T-Nut
- Can be Placed at Any Location Along the Curtain Track
The LPC05 is used to provide a hard stop for a curtain mounted to a track. As shown in the image to the right, it is designed to attach to the side channel of the curtain track using the provided drop-in nut and M4 cap screw. The drop-in nut can be placed into the channel from anywhere on the track; it does not need to be slid in on the end of the track.
When the curtain's wheel runner is in place, the end stop can be positioned with the bottom slot around the hook of the wheel runner. The end stop and held wheel runner can then be adjusted along the length of the curtain track by loosening the M4 cap screw that secures the end stop in place.
The LPC05 can also be attached to the top channel of the curtain track to provide additional wall support for the curtain system. See the image to the right for details and the manual for specific, step-by-step mounting instructions.

Right: Our curtain kits can be attached directly to our current overhead shelves using four M8 bolts and nuts. No brackets are required.
Included Hardware |
---|
Extension Bracket (x4) |
Spacer Bracket (x4) |
M8 Bolt (x16) |
M8 Nut (x16) |
M8 Washer (x32) |
Nut Caps (x16) |
- Needed to Attach a Curtain Kit to a Legacy* Optical Table Workstation or Free-Standing Shelf
- Can be Used to Attach a Laser Curtain Kit Directly to:
- An Optical Table Workstation with a Overhead Shelving Unit
- A PTA280 or PTA281 Free-Standing Overhead Shelving Unit
- All Necessary Hardware Included
Each laser curtain adapter kit includes four extension plates, four spacer plates, and all necessary hardware required to securely mount a laser curtain kit onto a legacy workstation or a free-standing shelf. For complete assembly instructions, please see the manual.
*All of Thorlabs' current Optical Table Worktations and Free-Standing Shelves are directly compatible with the laser curtain kits sold above and do not require this upgrade kit. Legacy workstations and free-standing shelves purchased before approximately March 2017 will require this kit to attach the above curtain kits. To check for compatibility, look for two Ø10 mm through holes in the top bar of the overhead shelf supports. Current shelving units have these through holes, allowing them to connect directly to the curtain kits as shown in the image to the far right. Our legacy overhead shelves do not have these Ø10 mm through holes, and the brackets included in the adapter kit are needed to secure the system in place, as shown in the photo to the near right.

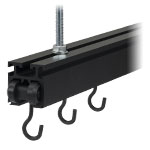
Click to Enlarge
Wheel runners shown being added to a curtain track. Each laser curtain includes one wheel runner for each eyelet.
The LPC07 contains a pack of 10 replacement wheel runners that are used to attach the laser safety curtains to a curtain track. First, insert the wheels of the LPC07 into the bottom channel of the curtain track. Then slide the hook of the wheel runner into the eyelet of the laser curtain.
Please note that Thorlabs' laser safety curtains come with one wheel runner for each eyelet in the panel.

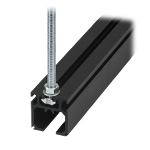
Click to Enlarge
M8-Threaded T-Nuts are Used in the top Channel of the Curtain Tracks to Attach Mounting Adapters and Track Connectors
The LPC06 contains a pack of 10 T-Nuts that can be used in the top channel of the laser curtain tracks. These T-Nuts effectively add M8 tapped holes to the laser curtain track, which allows the track connectors, mounting rods, and wall/ceiling mounting brackets in our modular curtain system to be mounted. They can also be used to replace the T-Nuts included in our Laser Curtain Kits to connect the tracks to the main support frame.
Please note that T-Nuts are provided with each laser curtain accessory.

Valance Material Certifications | |
---|---|
Wavelength | Certificationa |
D AB10 I AB5 R AB4 M AB2 |
|
D AB7 | |
R AB7 I AB8 M AB8 |
|
D AB5 | |
D AB3 I AB4 R AB2 |
LPCVH1 Included Hardware |
---|
Mounting Clip (x10) |
Connector Clip (x10) |
M4 Cap Screw (x20) |
M4 Drop-In T-Nut (x20) |
2.5 mm Hex Key (x1) |
- Designed to Cover Gaps Near Curtain Track or Ceiling
- Certified to EN 12254: 2010(E)*
- Flame Retardant
- Track Mounting Kit for Mounting up to 5 Valance Panels Available Separately
Thorlabs' Laser Safety Valance Panel is certified to EN 12254: 2010(E); certification levels can be found in the table to the right. The valance panel is made using a rubber compound and is designed to cover any gaps between laser safety curtains and the curtain tracks or the ceiling. The back of the valance displays the Item # and manufacturing date on a product information label. The valance panel is available from stock in dimensions of 1.2 m wide by 0.4 m high and can be overlapped to cover the required area.
A separate hardware kit allows for the valance panels to be mounted on the curtain tracks of a laser curtain kit. The LPCVH1 Track Mounting Kit comes with 10 mounting clips to support the valance panels, as well as 10 connector clips which allow the valance panels to be securely overlapped to prevent gaps in coverage. It is recommended that at least two mounting clips are used to support each valance panel, with an additional clip used when installing the panels on a curved track, allowing for the installation of up to five valance panels. To attach the mounting clips to the curtain tracks the kit includes 20 M4 drop-in T-nuts, which can be inserted into the side channel of the curtain tracks. These T-nuts accept the included M4 cap screws; two screws can be used to secure one mounting clip, which can then be used to help support the valance panels. Please see the manual for detailed mounting instructions.
When ordering valance panels, we recommend allowing for an overlap of at least 10 cm between panels to prevent light leakage; if using the connector clips, an overlap of 15 cm is needed to allow the rigid support bars in each valance panel to overlap. An additional hardware kit designed for use with our LPC02 mounting rods is available with our laser curtain systems.
*DISCLAIMER
The valance materials have been tested by a third party using EN specifications; see the Certifications tab for details. Due to manufacturing variances, mechanical wear, and laser damage, Thorlabs assumes no responsibility for laser safety valance failure. Please consult your local laser safety specialist before purchasing to ensure that the valance is suitable for your application. To minimize risk, inspect the valance before each use and ensure that it is in excellent condition.