NIR Volume Phase Holographic Transmission Gratings
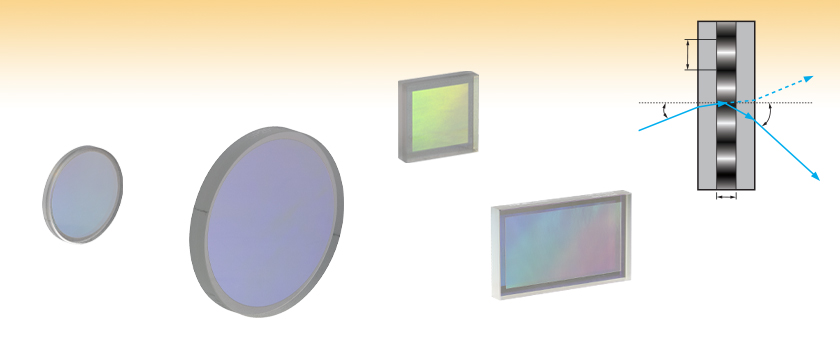
- Six Design Wavelengths from 840 nm to 1550 nm
- High First-Order Diffraction Efficiency
- Resistant to Fingerprint and Aerosol Damage
a
d
θi
θm
GP3508U
1300 nm, 800 Lines/mm, 50 mm x 30 mm
GP2012L
840 nm, 1200 Lines/mm,
Ø2"
GP1012L
840 nm, 1200 Lines/mm,
Ø1"
Volume Phase Holographic Grating Schematic
GP1118P
1030 nm, 1800 Lines/mm,
1" x 1"

Please Wait
Selection Guide | |
---|---|
Transmission Gratings | |
Ruled | UV |
Visible | |
Near IR | |
Volume Phase Holographic |
Visible |
Near IR | |
Reflective Gratings | |
Ruled | UV |
Visible | |
Near IR | |
Mid IR | |
Holographic | |
Echelle |
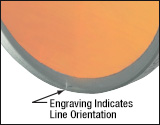
Click to Enlarge
The circular and square gratings have engravings that indicate the line orientation.
Common Specifications | |
---|---|
Grating Film | Dichromated Gelatin |
Cover-Plate Substrate | GP3508P and GP1118P: C7980 Fused Silicaa or Equivalent All Others: N-BK7a or Equivalent |
Thickness Tolerance | ±0.2 mm |
Spatial Frequency Tolerance |
±2 lines/mm |
AOI Tolerance | ±1° |
Transmitted Wavefront Error (RMS) |
<λ/4 at 632.8 nm |
Surface Quality | 40-20 Scratch-Dig |
Webpage Features | |
---|---|
![]() |
Clicking this info icon below will open a window that contains specifications and performance plots. |
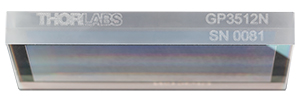
Click to Enlarge
The item number and serial number are engraved on the edge of each rectanglar and square grating.
NIR VPH Transmission Gratings Selection Guide | |||||
---|---|---|---|---|---|
Design Wavelength (nm) |
Spatial Frequency (Lines/mm) |
Ø1" | Ø2" | 50 x 30 mm | 1" x 1" |
840 | 600 | GP1006L | GP2006L | GP3506L | - |
960 | GP10096L | GP20096L | GP35096L | - | |
1200 | GP1012L | GP2012L | GP3512L | - | |
900 | 600 | GP1006M | GP2006M | GP3506M | - |
1000 | - | - | GP3510M | - | |
930 | 900 | GP1009N | GP2009N | GP3509N | - |
1200 | - | - | GP3512N | - | |
1500 | - | - | GP3515N | - | |
1030 | 800 | - | - | GP3508P | - |
1800 | - | - | - | GP1118P | |
1300 | 800 | GP3508U | - | ||
1550 | 600 | GP1006Z | GP2006Z | GP3506Z | - |
Features
- Design Wavelength (DWL) and Spatial Frequency Options:
- 840 nm: 600, 960, or 1200 Lines/mm
- 900 nm: 600 or 1000 Lines/mm
- 930 nm: 900, 1200, or 1500 Lines/mm
- 1030 nm: 800 or 1800 Lines/mm
- 1300 nm: 800 Lines/mm
- 1550 nm: 600 Lines/mm
- High First-Order Diffraction Peak Efficiency (See Tables Below)
- Uniform Performance Over Broad Bandwidths (See Diffraction Efficiency Graphs Below)
- Extremely Low Scatter Between Orders (No Ghosting)
- Dichromated Gelatin (DCG) Film Between Two Glass Substrates
- Ideal for Spectroscopy, Optical Coherence Tomography (OCT), and Laser Pulse Compression
Thorlabs' Near Infrared Volume Phase Holographic (VPH) Transmission Gratings are ideal for applications that require high diffraction efficiency. We offer a variety of gratings in Ø1" or Ø2" circular, 50 mm x 30 mm rectangular, and 1" square formats. See the table to the lower right for a full summary of the grating sizes available for each design wavelength and spatial frequency. These unique transmission gratings exhibit high first-order diffraction efficiency across broad bandwidths, extremely low scatter of stray light between diffraction order peaks, and minimal ghosting, making them well-suited for use in spectroscopy, OCT, and laser pulse compression applications. All gratings have low polarization-dependent loss except for Item # GP1118P, which is designed for use with incident light polarized parallel to the grating lines.
VPH gratings are different from traditional gratings since they have no surface grooves. In this case, diffraction occurs as incoming light crosses through a DCG film with periodic index modulations sealed between two glass substrates. To minimize transmission losses due to reflection, the air-to-glass interfaces are also antireflection (AR) coated. Unlike other gratings, these VPH gratings are resistant to damage from fingerprints and aerosols, as well as easy to maintain since they can be cleaned using standard optics cleaning methods. For more information, see the Gratings Tutorial tab. Environmental testing has been performed to ensure that our VPH gratings continue to meet all specifications after 20 thermal cycles from 40 °C to -18 °C with a two hour holding period at each endpoint temperature. Each grating is engraved with its Item # on the edge as seen in the image to the right. The circular and square gratings feature an engraving that indicates the line orientation. The line pair orientation of the rectangular gratings is perpendicular to the long (50 mm) edge.
The Gratings Guide tab provides a summary of the other grating types that Thorlabs offers, while information on the differences between grating types can be found on the Gratings Tutorial tab.
Note: On some gratings, a holographic mirroring effect may be seen. This is not a defect in the grating, but a non-intrusive artifact written into the film during the exposure process. These interference patterns do not affect the performance of the grating.
Custom Volume Phase Holographic Gratings
Thorlabs is capable of fabricating custom VPH gratings to support the needs of other applications, such as astronomy. High dispersion can be achieved to meet specialized customer needs with line densities ranging from 400 to 1800 lines/mm, center wavelengths from 300 to 2000 nm, and bandwidths of 20 to 500 nm. Customized round or square optics can be achieved with dimensions as small as 10 mm and as large as 60 mm. Please contact Tech Support with inquiries.
Mounts and Adapters
For round gratings, we recommend using a rotation mount, such as our nested or kinematic rotation mounts, so that the user can align the line orientation to a fixed degree value and use the mount to rotate the optic while tracking the displacement of the first-order diffracted beam. The rectangular and square gratings can be mounted directly into the KM100C Right-Handed or KM100CL Left-Handed Kinematic Rectangular Optic Mount for precise and stable mounting and alignment.
Thorlabs uses a clean room facility for assembly of gratings into mechanical setups. If your application requires integrating the grating into a sub-assembly or a setup, please contact Tech Support to learn more about our assembly capabilities.
Diffraction Gratings Tutorial
- Introduction
- Blazed (Ruled) Gratings
- Volume Phase Holographic Transmission Gratings
- Holographic Reflective Gratings
Introduction
Diffraction gratings, either transmissive or reflective, can separate different wavelengths of light using a repetitive structure embedded within the grating. The structure affects the amplitude and/or phase of the incident wave, causing interference in the output wave. In the transmissive case, the repetitive structure can be thought of as many tightly spaced, thin slits. Solving for the irradiance as a function wavelength and position of this multi-slit situation, we get a general expression that can be applied to all diffractive gratings when = 0°,
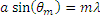
(1)
known as the grating equation. The equation states that a diffraction grating with spacing will deflect light at discrete angles (
), dependent upon the value
λ, where
is the order of principal maxima. The diffracted angle,
, is the output angle as measured from the surface normal of the diffraction grating. It is easily observed from Eq. 1 that for a given order
, different wavelengths of light will exit the grating at different angles. For white light sources, this corresponds to a continuous, angle-dependent spectrum.
Figure 1. Transmission Grating
Transmission Gratings
One popular style of grating is the transmission grating. The sample diffraction grating with surfaces grooves shown in Figure 1 is created by scratching or etching a transparent substrate with a repetitive series of narrow-width grooves separated by distance . This creates areas where light can scatter.
The incident light impinges on the grating at an angle , as measured from the surface normal. The light of order
exiting the grating leaves at an angle of
, relative to the surface normal. Utilizing some geometric conversions and the general grating expression (Eq. 1) an expression for the transmissive diffraction grating can be found:

(2)
where both and
are positive if the incident and diffracted beams are on opposite sides of the grating surface normal, as illustrated in the example in Figure 1. If they are on the same side of the grating normal,
must then be considered negative.
Figure 2. Reflective Grating
Reflective Gratings
Another very common diffractive optic is the reflective grating. A reflective grating is traditionally made by depositing a metallic coating on an optic and ruling parallel grooves in the surface. Reflective gratings can also be made of epoxy and/or plastic imprints from a master copy. In all cases, light is reflected off of the ruled surface at different angles corresponding to different orders and wavelengths. An example of a reflective grating is shown in Figure 2. Using a similar geometric setup as above, the grating equation for reflective gratings can be found:

(3)
where is positive and
is negative if the incident and diffracted beams are on opposite sides of the grating surface normal, as illustrated in the example in Figure 2. If the beams are on the same side of the grating normal, then both angles are considered positive.
Both the reflective and transmission gratings suffer from the fact that the zeroth order mode contains no diffraction pattern and appears as a surface reflection or transmission, respectively. Solving Eq. 2 for this condition, =
, we find the only solution to be
=0, independent of wavelength or diffraction grating spacing. At this condition, no wavelength-dependent information can be obtained, and all the light is lost to surface reflection or transmission.
This issue can be resolved by creating a repeating surface pattern, which produces a different surface reflection geometry. Diffraction gratings of this type are commonly referred to as blazed (or ruled) gratings. More information about this can be found in the section below.
Blazed (Ruled) Gratings
Figure 4. Blazed Grating, 0th Order Reflection
Figure 3. Blazed Grating Geometry
The blazed grating, also known as the echelette grating, is a specific form of reflective or transmission diffraction grating designed to produce the maximum grating efficiency in a specific diffraction order. This means that the majority of the optical power will be in the designed diffraction order while minimizing power lost to other orders (particularly the zeroth). Due to this design, a blazed grating operates at a specific wavelength, known as the blaze wavelength.
The blaze wavelength is one of the three main characteristics of the blazed grating. The other two, shown in Figure 3, are , the groove or facet spacing, and
, the blaze angle. The blaze angle
is the angle between the surface structure and the surface parallel. It is also the angle between the surface normal and the facet normal. Note that Figure 3 also defines the direction of the "blaze arrow"; this arrow is visibly marked on one edge of all Thorlabs' blazed transmission gratings.
The blazed grating features geometries similar to the transmission and reflection gratings discussed thus far; the incident angle () and
th order reflection angles (
) are determined from the surface normal of the grating. However, the significant difference is the specular reflection geometry is dependent on the blaze angle,
, and NOT the grating surface normal. This results in the ability to change the diffraction efficiency by only changing the blaze angle of the diffraction grating.
The 0th order reflection from a blazed grating is shown in Figure 4. The incident light at angle is reflected at
for
= 0. From Eq. 3, the only solution is
= –
. This is analogous to specular reflection from a flat surface.
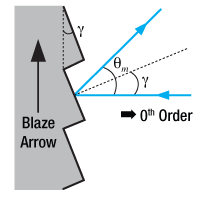
Figure 6. Blazed Grating, Incident Light Normal to Grating Surface
Figure 5. Blazed Grating, Specular Reflection from Facet
The specular reflection from the blazed grating is different from the flat surface due to the surface structure, as shown in Figure 5. The specular reflection, , from a blazed grating occurs at the blaze angle geometry. This angle is defined as being negative if it is on the same side of the grating surface normal as
. Performing some simple geometric conversions, one finds that

(4)
Figure 6 illustrates the specific case where = 0°, hence the incident light beam is perpendicular to the grating surface. In this case, the 0th order reflection also lies at 0°. Utilizing Eqs. 3 and 4, we can find the grating equation at twice the blaze angle:
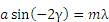
(5)
Littrow Configuration for Reflective Gratings
The Littrow configuration refers to a specific geometry for blazed gratings and plays an important role in monochromators and spectrometers. It is the angle at which the grating efficiency is the highest. In this configuration, the angle of incidence of the incoming and diffracted light are the same,
=
, and
> 0 so

(6)
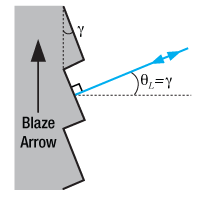
Figure 7. Littrow Configuration
The Littrow configuration angle, , is dependent on the most intense order (
= 1), the design wavelength,
, and the grating spacing
. It is easily shown that the Littrow configuration angle,
, is equal to the blaze angle,
, at the design wavelength. The Littrow / blaze angles for all Thorlabs' Blazed Gratings can be found in the grating specs tables.

(7)
It is easily observed that the wavelength dependent angular separation increases as the diffracted order increases for light of normal incidence (for = 0°,
increases as
increases). There are two main drawbacks for using a higher order diffraction pattern over a low order one: (1) a decrease in efficiency at higher orders and (2) a decrease in the free spectral range,
, defined as:

(8)
where is the central wavelength, and
is the order.
The first issue with using higher order diffraction patterns is solved by using an Echelle grating, which is a special type of ruled diffraction grating with an extremely high blaze angle and relatively low groove density. The high blaze angle is well suited for concentrating the energy in the higher order diffraction modes. The second issue is solved by using another optical element: grating, dispersive prism, or other dispersive optic, to sort the wavelengths/orders after the Echelle grating.
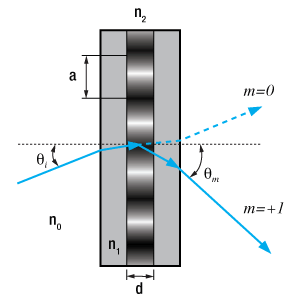
Figure 8. Volume Phase Holographic Grating
Volume Phase Holographic Transmission Gratings
Unlike traditional gratings, volume phase holographic (VPH) gratings do not have surface grooves. Instead, VPH gratings consist of a dichromated gelatin (DCG) film between two glass substrates. These VPH gratings are designed to reduce the periodic errors that can occur in blazed gratings. Surface gratings with high groove density also have an issue with polarization dependent loss. These unique transmission gratings deliver high first-order diffraction peak efficiency, low polarization dependence, and uniform performance over broad bandwidths.
The desired grating pattern is comprised of a repetitive series of lines separated by distance . The fringe planes for transmission gratings are perpendicular to the plane of the plate as seen in Figure 8, allowing any frequency of light to pass through the plate. Diffraction occurs as incoming light crosses through the DCG film. Therefore, the three major factors that determine performance are film thickness, bulk index (the average index of refraction between Bragg planes), and index modulation (the difference of index of refraction between the Bragg planes). The incident light enters the grating at an angle of
, as measured from the surface normal. The light of order
exiting the grating leaves at an angle of
, relative to the surface normal. The grating expression mentioned above can be used to calculate diffraction angles for volume phase holographic gratings since dispersion is based on the line density. The quality of the grating is determined by the fringe contrast, with a poor fringe contrast resulting in low efficiency or no grating at all.
The DCG film is taken through multiple quality control steps to ensure it performs up to standard and then cut into the desired size. The film is sealed between two glass covers to prevent degradation of the material. Since the DCG film is contained between two glass substrates, VPH gratings have high durability and long lifetimes, as well as easy maintenance compared to other gratings that can be easily damaged.
Figure 9. Holographic Grating
Holographic Surface Reflective Gratings
While blazed gratings offer extremely high efficiencies at the design wavelength, they suffer from periodic errors, such as ghosting, and relatively high amounts of scattered light, which could negatively affect sensitive measurements. Holographic gratings are designed specially to reduce or eliminate these errors. The drawback of holographic gratings compared to blazed gratings is reduced efficiency.
Holographic gratings are made from master gratings by similar processes to the ruled grating. The master holographic gratings are typically made by exposing photosensitive material to two interfering laser beams. The interference pattern is exposed in a periodic pattern on the surface, which can then be physically or chemically treated to expose a sinusoidal surface pattern. An example of a holographic grating is shown in Figure 9.
Please note that dispersion is based solely on the number of grooves per mm and not the shape of the grooves. Hence, the same grating equation can be used to calculate angles for holographic as well as ruled blazed gratings.
Posted Comments: | |
Jerome Faist
 (posted 2024-05-01 06:36:46.58) Could these gratings be cut to smaller pieces (5.5mm) to fit in a tight cavity?
Yours,
Jerome cdolbashian
 (posted 2024-05-06 01:17:52.0) Thank you for reaching out to us with this inquiry. We can potentially do this as a custom, though there would be some considerations to discuss. I have contacted you directly to have such a conversation. user
 (posted 2024-03-25 12:40:44.15) I would like to conduct optical simulations using your two products, GP3508P and GP1118P. Optical simulation is necessary to determine the position of the diffraction grating on the beamline. Can you provide Zemax files for these products? cdolbashian
 (posted 2024-03-29 02:26:13.0) Thank you for reaching out to us with this inquiry. Unfortunately, we do not have zemax files to share for these gratings. I have contacted you directly to discuss this further in order to see how we can assist you. Conner Phillips
 (posted 2023-11-01 11:33:26.527) Greetings,
I would like to know if you could comment on the anti-reflection properties of GP3508P if operating over a wavelength range of 750-920nm (830nm center) with an angle of incidence 19.3 degrees. Obviously the GP1012L has the correct design wavelength for our application, but we have a fixed detector size and would like to use a longer focal length lens before the detector to achieve a higher system magnification, necessitating a smaller grating constant. jpolaris
 (posted 2023-11-14 06:26:47.0) Thank you for contacting Thorlabs. The performance of a broadband AR coating when used outside its design wavelength range is oftentimes difficult to predict, particularly at wavelengths shorter than the design wavelength. Further, if you use a grating at an AOI other than the design AOI, you can expect to see a drop in diffraction efficiency. Theoretical Bragg sensitivity data shows an ~30% drop in efficiency when GP3508P is used ± 5° away from the 24.3° design AOI. It should be noted that the design AOI is wavelength-dependent as well. I have reached out to you directly to discuss this. |
Transmission Gratings
Thorlabs offers two types of transmission gratings: ruled and volume phase holographic. The ruled transmission gratings are created by scratching or etching a transparent substrate with a repetitive, parallel structure, creating areas where light can scatter. These gratings have a sawtooth diffraction profile and are made of epoxy and/or plastic imprints from a master copy, in a process called replication. Our volume phase holographic diffraction gratings consist of a dichromated gelatin (DCG) film between two glass substrates. These gratings have a sinusoidal wave diffraction pattern written on the DCG film using a laser setup. For more information, please refer to the Gratings Tutorial tab.
Ruled Diffraction Gratings | ||
---|---|---|
![]() |
UV | Thorlabs' ruled transmission gratings disperse incident light on the opposite side of the grating at a fixed angle. They are ruled and blazed for optimum efficiency in their respective wavelength range, are relatively polarization insensitive, and have an efficiency comparable to that of a reflection grating optimized for the same wavelength. They are ideal for applications that require fixed gratings such as spectrographs. |
Visible | ||
Near IR |
UV Ruled Transmission Blazed Diffraction Gratings |
---|
Visible Ruled Transmission Blazed Diffraction Gratings |
---|
NIR Ruled Transmission Blazed Diffraction Gratings |
---|
Volume Phase Holographic Diffraction Gratings | |||
---|---|---|---|
![]() |
Volume Phase Holographic | Thorlabs' volume phase holographic (VPH) gratings consist of a DCG film between two glass substrates. These unique transmission gratings are easy to maintain and deliver high first-order diffraction peak efficiency and uniform performance over broad bandwidths. |
Visible VPH Transmission Gratings |
---|
NIR VPH Transmission Gratings |
---|
Reflective Gratings
Reflective grating master copies are made by depositing a metallic coating on an optic and ruling parallel grooves in the surface. Thorlabs' reflective gratings are made of epoxy and/or plastic imprints from a master copy, in a process called replication. In all cases, light is reflected off of the ruled surface at different angles corresponding to different orders and wavelengths. All of Thorlabs' ruled reflective diffraction gratings exhibit a sawtooth profile, also known as blazed, while our reflective holographic diffraction gratings exhibit a sinusoidal profile. For more information, please refer to the Gratings Tutorial tab.
Ruled Diffraction Gratings | ||
---|---|---|
![]() |
UV | Ruled gratings can achieve higher efficiencies than holographic gratings due to their blaze angles. They are ideal for applications centered near the blaze wavelength. Thorlabs offers replicated ruled diffraction gratings in a variety of sizes and blaze angles. |
Visible | ||
Near IR | ||
Mid IR |
UV Ruled Reflective Blazed Diffraction Gratings |
---|
Visible Ruled Reflective Blazed Diffraction Gratings |
---|
Near-IR Ruled Reflective Blazed Diffraction Gratings |
---|
Mid-IR Ruled Reflective Blazed Diffraction Gratings |
---|
Holographic Diffraction Gratings | |||
---|---|---|---|
![]() |
Holographic | Holographic gratings have a low occurrence of periodic errors, which results in limited ghosting, unlike ruled gratings. The low stray light of these gratings makes them ideal for applications where the signal-to-noise ratio is critical, such as Raman Spectroscopy. |
Reflective Holographic Sinusoidal Diffraction Gratings |
---|
Echelle Diffraction Gratings | |||
---|---|---|---|
![]() |
Echelle | Echelle gratings are low period gratings designed for use in high diffraction orders. They are generally used with a second grating or prism to separate overlapping diffracted orders. They are ideal for applications such as high-resolution spectroscopy. |
Echelle Ruled Blazed Diffraction Gratings |
---|
Selecting a grating requires consideration of a number of factors, some of which are listed below:
Efficiency:
Ruled gratings generally have a higher efficiency than holographic gratings. Holographic grating tend to have a lower efficiency but a broader effective wavelength range. The efficiency of ruled gratings may be desirable in applications such as fluorescence excitation and other radiation-induced reactions.
Blaze Wavelength:
Ruled gratings have a sawtooth groove profile created by sequentially etching the surface of the grating substrate. As a result, they have a sharp peak efficiency around their blaze wavelength. Holographic gratings are harder to blaze, and tend to have a sinusoidal groove profile resulting in a less intense peak around the design wavelength. Applications centered around a narrow wavelength range could benefit from a ruled grating blazed at that wavelength.
Stray Light:
Due to a difference in how the grooves are made, holographic gratings have less stray light than ruled gratings. The grooves on a ruled grating are machined one at a time which results in a higher frequency of errors. Holographic gratings are made through a lithographic process, which generally creates smoother grating masters free of tool marks. Replicants made from these masters exhibit less stray light. Applications such as Raman spectroscopy, where signal-to-noise is critical, can benefit from the limited stray light of the holographic grating.
Resolving Power:
The resolving power of a grating is a measure of its ability to spatially separate two wavelengths. It is determined by applying the Rayleigh criteria to the diffraction maxima; two wavelengths are resolvable when the maxima of one wavelength coincides with the minima of the second wavelength. The chromatic resolving power (R) is defined by R = λ/Δλ = n*N, where Δλ is the resolvable wavelength difference, n is the diffraction order, and N is the number of grooves illuminated. Due to their low groove density, Echelle gratings provide high resolving power.
Polarization Dependence:
Surface gratings that have high groove densities also have an issue with polarization dependent loss, often with significantly lower efficiency when exposed to parallel- versus perpendicularly-polarized light. Volume phase holographic gratings are designed for applications that require low polarization dependent loss at higher spatial frequencies.
For further information about gratings and selecting the grating right for your application, please visit our Gratings Tutorial.
Caution for Gratings with Surface Grooves:
The surface of a diffraction grating with surface grooves can be easily damaged by fingerprints, aerosols, moisture or the slightest contact with any abrasive material. Gratings should only be handled when necessary and always held by the sides. Latex gloves or a similar protective covering should be worn to prevent oil from fingers from reaching the grating surface. Solvents will likely damage the grating's surface. No attempt should be made to clean a grating other than blowing off dust with clean, dry air or nitrogen. Scratches or other minor cosmetic imperfections on the surface of a grating do not usually affect performance and are not considered defects. Conversely, volume phase holographic gratings can be cleaned using standard optics cleaning procedures and have high durability.

Item # | Info | DWLa | Spatial Frequency |
AOIb | Diffraction Efficiencyc | BBAR Coatingd |
Cover Plate Substrate |
Dimensions |
---|---|---|---|---|---|---|---|---|
GP1006L | ![]() |
840 nm | 600 lines/mm | 14.6° | ![]() 650 nm: S-Pol > 70%; P-Pol > 70% 840 nm: S-Pol > 85%; P-Pol > 85% 1030 nm: S-Pol > 70%; P-Pol > 70% |
600 - 1050 nm Ravg < 1.0% |
N-BK7e or Equivalent |
Ø25.4 mm x 3.0 mm |
GP2006L | ![]() |
Ø50.8 mm x 6.0 mm | ||||||
GP3506L | ![]() |
50.0 mm x 30.0 mm x 6.0 mm | ||||||
GP10096L | ![]() |
960 lines/mm | 23.8° | ![]() 730 nm: S-Pol > 70%; P-Pol > 70% 840 nm: S-Pol > 85%; P-Pol > 85% 950 nm: S-Pol > 70%; P-Pol > 70% |
700 - 1000 nm Ravg < 0.75% |
Ø25.4 mm x 3.0 mm | ||
GP20096L | ![]() |
Ø50.8 mm x 6.0 mm | ||||||
GP35096L | ![]() |
50.0 mm x 30.0 mm x 6.0 mm | ||||||
GP1012L | ![]() |
1200 lines/mm | 30.3° | ![]() 730 nm: S-Pol > 50%; P-Pol > 60% 840 nm: S-Pol > 80%; P-Pol > 80% 950 nm: S-Pol > 60%; P-Pol > 50% |
650 - 1010 nm Ravg < 1.0% |
Ø25.4 mm x 3.0 mm | ||
GP2012L | ![]() |
Ø50.8 mm x 6.0 mm | ||||||
GP3512L | ![]() |
50.0 mm x 30.0 mm x 6.0 mm |

Item # | Info | DWLa | Spatial Frequency |
AOIb | Diffraction Efficiencyc | BBAR Coatingd |
Cover Plate Substrate |
Dimensions |
---|---|---|---|---|---|---|---|---|
GP1006M | ![]() |
900 nm | 600 lines/mm | 15.7° | ![]() 750 nm: S-Pol > 70%; P-Pol > 70% 900 nm: S-Pol > 85%; P-Pol > 85% 1050 nm: S-Pol > 70%; P-Pol > 70% |
700 - 1100 nm Ravg < 0.75% |
N-BK7e or Equivalent |
Ø25.4 mm x 3.0 mm |
GP2006M | ![]() |
Ø50.8 mm x 6.0 mm | ||||||
GP3506M | ![]() |
50.0 mm x 30.0 mm x 6.0 mm | ||||||
GP3510M | ![]() |
1000 lines/mm | 27° | ![]() 800 nm: S-Pol > 65%; P-Pol > 78% 900 nm: S-Pol > 85%; P-Pol > 85% 1000 nm: S-Pol > 75%; P-Pol > 70% |
750 - 1050 nm Ravg < 0.75% |
50.0 mm x 30.0 mm x 6.0 mm |

Item # | Info | DWLa | Spatial Frequency |
AOIb | Diffraction Efficiencyc | BBAR Coatingd |
Cover Plate Substrate |
Dimensions |
---|---|---|---|---|---|---|---|---|
GP1009N | ![]() |
930 nm | 900 lines/mm | 25° | ![]() 830 nm: S-Pol > 60%; P-Pol > 60% 930 nm: S-Pol > 80%; P-Pol > 80% 1030 nm: S-Pol > 60%; P-Pol > 60% |
700 - 1100 nm Ravg < 1.0% |
N-BK7e or Equivalent |
Ø25.4 mm x 3.0 mm |
GP2009N | ![]() |
Ø50.8 mm x 6.0 mm | ||||||
GP3509N | ![]() |
![]() 892 nm: S-Pol > 85%; P-Pol > 88% 930 nm: S-Pol > 88%; P-Pol > 88% 968 nm: S-Pol > 88%; P-Pol > 85% |
750 - 1050 nm Ravg < 0.75% |
50.0 mm x 30.0 mm x 6.0 mm | ||||
GP3512N | ![]() |
1200 lines/mm | 34° | ![]() 885 nm: S-Pol > 75%; P-Pol > 80% 930 nm: S-Pol > 80%; P-Pol > 80% 975 nm: S-Pol > 80%; P-Pol > 70% |
50.0 mm x 30.0 mm x 6.0 mm | |||
GP3515N | ![]() |
1500 lines/mm | 44° | ![]() 899 nm: S-Pol > 85%; P-Pol > 74% 930 nm: S-Pol > 80%; P-Pol > 90% 961 nm: S-Pol > 70%; P-Pol > 75% |
750 - 1050 nm Ravg < 1.5% |
50.0 mm x 30.0 mm x 6.0 mm |

Item # | Info | DWLa | Spatial Frequency |
AOIb | Diffraction Efficiencyc | BBAR Coatingd |
Cover Plate Substrate |
Dimensions |
---|---|---|---|---|---|---|---|---|
GP3508P | ![]() |
1030 nm | 800 lines/mm | 24.3° | ![]() 980 nm: S-Pol > 80%; P-Pol > 85% 1030 nm: S-Pol > 90%; P-Pol > 90% 1080 nm: S-Pol > 85%; P-Pol > 80% |
930 - 1130 nm Ravg < 0.5% |
C7980 Fused Silicae or Equivalent |
50.0 mm x 30.0 mm x 6.0 mm |
GP1118P | ![]() |
1800 lines/mm | 68.0° | ![]() 1020 nm: S-Pol > 90%f 1030 nm: S-Pol > 90%f 1040 nm: S-Pol > 90%f |
1000 - 1060 nm RSavg < 1.5% |
25.4 mm x 25.4 mm x 6.0 mm |

Item # | Info | DWLa | Spatial Frequency |
AOIb | Diffraction Efficiencyc | BBAR Coatingd |
Cover Plate Substrate |
Dimensions |
---|---|---|---|---|---|---|---|---|
GP3508U | ![]() |
1300 nm | 800 lines/mm | 31° | ![]() 1230 nm: S-Pol > 75%; P-Pol > 80% 1300 nm: S-Pol > 80%; P-Pol > 80% 1370 nm: S-Pol > 80%; P-Pol > 75% |
1180 - 1420 nm Ravg < 0.75% |
N-BK7e or Equivalent |
50.0 mm x 30.0 mm x 6.0 mm |

Item # | Info | DWLa | Spatial Frequency |
AOIb | Diffraction Efficiencyc | BBAR Coatingd |
Cover Plate Substrate |
Dimensions |
---|---|---|---|---|---|---|---|---|
GP1006Z | ![]() |
1550 nm | 600 lines/mm | 27.7° | ![]() 1400 nm: S-Pol > 70%; P-Pol > 70% 1550 nm: S-Pol > 85%; P-Pol > 85% 1700 nm: S-Pol > 70%; P-Pol > 70% |
1350 - 1750 nm Ravg < 1.25% |
N-BK7e or Equivalent |
Ø25.4 mm x 3.0 mm |
GP2006Z | ![]() |
Ø50.8 mm x 6.0 mm | ||||||
GP3506Z | ![]() |
50.0 mm x 30.0 mm x 6.0 mm |