Programmable Fiber Connector Epoxy Curing Ovens
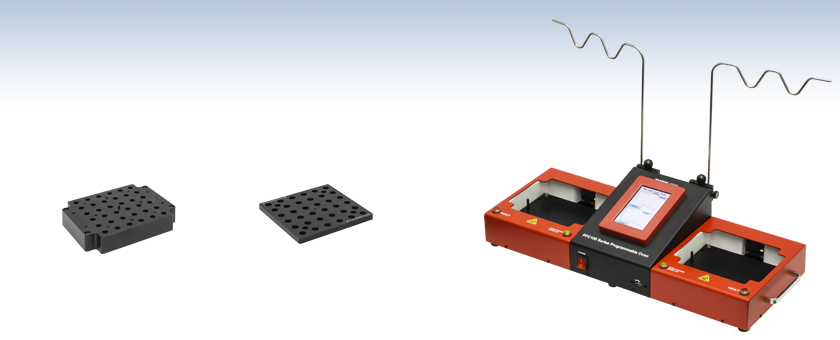
- Cure Epoxy on Up to 72 Fiber Connectors
- User-Programmable Curing Cycles with Ramp and Soak
- Max Curing Temperature of 150 °C
- Single or Double Bay Versions
PFC9AL
Aluminum Curing Block for
Ø9-10 mm Connectors
(Sold Separately)
PFC10TF
Optional PTFE Guide Plate for
Ø10 mm Connectors
(Optional; Sold Separately)
PFC121
Double Bay Curing Oven

Please Wait
Key Specsa | |
---|---|
Compatible Connectors | FC/PC, FC/APC, SMA, ST/PC, & SC/PC |
Connector Capacity | 36 or 72 |
Max Temperature | 150 °C (302 °F) |
Temperature Accuracy | ±1.5 °C |
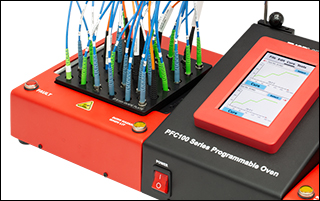
Click to Enlarge
Thorlabs' PFC121 Fiber Connector Epoxy Curing Oven Shown with Curing Blocks, Guide Plates, and Patch Cables (Each Sold Separately)
Demo Unit Available
Interested in trying the Fiber Connector Epoxy Curing Oven for your application? Contact us at techsales@thorlabs.com to request a demo unit.Features
- Fully Programmable Using the Integrated Controller
- Low Stress PM Fiber Curing for Increased PER
- High Temperature Uniformity and Repeatability
Thorlabs' PFC100 Series Curing Ovens are specifically designed for curing high performance connector epoxy during the fiber-to-ferrule termination process. Models are available with simultaneous curing capacities of 36 connectors (PFC111 & PFC112) or 72 connectors (PFC121 & PFC122). The PTFE-coated, aluminum curing blocks (sold separately) accommodate various sizes of FC/PC, FC/APC, SMA, ST®*/PC, and SC/PC connectors. We also offer optional PTFE guide plates for increased connector stability.
The curing oven has an integrated PID temperature controller and touch screen interface that allows the oven to be set at a constant temperature (soak) or run through a programmed ramp and soak cycle. The controller has a capability of 50 ramp/soak steps and 99 preset curing schedules. The heaters are capable of bringing the curing area up to 150 °C (302 °F). A temperature vs. time log is recorded by the controller and can then be exported through the USB for tracking and quality control purposes.
Warning: This device is solely designed for curing fiber connectors. Using the oven for any other purposes will void the warranty and may cause damage to the machine and/or result in personal injury.
*ST® is a registered trademark of Lucent Technologies, Inc.
Item # | PFC111 | PFC112 | PFC121 | PFC122 |
---|---|---|---|---|
Compatible Connectors |
FC/PC, FC/APC, SMA, ST®a/PC, SC/PC | |||
Oven Bays | One | Two | ||
Connector Capacity | 36 | 72 | ||
Max Temperature | 150 °C (302 °F) | |||
Temperature Accuracy | ±1.5 °C | |||
Power Consumption | 250 W (Single Bay) | 500 W (Double Bay) | ||
Max # of Curing Profiles |
99 | |||
Max # of Steps | 50 | |||
Temperature Logging | 1 min. Increment CSV Format Accessible Through USB | |||
Operating Conditions | 15 to 30 °C, 0 - 85% RH (Non-Condensing) | |||
Storage Conditions | -40 to 80 °C, 0 - 95% RH (Non-Condensing) | |||
Power Source | 90-130 VAC @ 47-63 Hz |
210-240 VAC @ 47-63 Hz |
90-130 VAC @ 47-63 Hz |
210-240 VAC @ 47-63 Hz |
Dimensions (W × H × D) |
16.96" x 15.10" x 9.72" (430.7 mm x 383.6 mm x 247.0 mm) |
24.88" x 15.10" x 9.72" (631.8 mm x 383.6 mm x 247.0 mm) |
||
Mass (Weight) | 7 kg (15 lbs) | 10 kg (22 lbs) |
Selected Compatible Connectorsa | |||
---|---|---|---|
Connector Item # |
Connector Description | Curing Blockb |
Guide Platec |
30127A3 | FC/APC, MM, Ø127 µm Bore, Ø3 mm Boot | PFC10AL (Ø9 - 10 mm Connector, <Ø3.4 mm Ferrule) |
PFC10TF (Ø10 mm Connector) |
30080D1 | FC/PC, SM, Ø80 µm Bore, Ø900 µm Boot | ||
30125D2 | FC/PC, PM, Ø125.5 µm Bore, Ø3 mm & Ø900 µm Boots |
||
30126C3 | FC/PC, SM, Ø126 µm Bore, Ø3 mm Boot | ||
30126C9 | FC/PC, SM, Ø126 µm Bore, Ø900 µm Boot | ||
30126B1 | ST®/PC, SM, Ø125 µm Bore, Ø3 mm Boot | ||
10125A | SMA905, MM, Ø128 µm Bore, Ø3 mm Boot | PFC9AL (Ø8 - 9 mm Connector, <Ø3.4 mm Ferrule) |
PFC9TF (Ø9 mm Connector) |
10140A | SMA905, MM, Ø144 µm Bore, Ø3 mm Boot | ||
10230A | SMA905, MM, Ø231 µm Bore, Ø3 mm Boot | ||
10245A | SMA905, MM, Ø245 µm Bore, Ø3 mm Boot | ||
10250A | SMA905, MM, Ø250 µm Bore, Ø3 mm Boot | ||
10260A | SMA905, MM, Ø260 µm Bore, Ø3 mm Boot | ||
10270A | SMA905, MM, Ø270 µm Bore, Ø3 mm Boot | ||
10340A | SMA905, MM, Ø340 µm Bore, Ø3 mm Boot | ||
10380A | SMA905, MM, Ø380 µm Bore, Ø3 mm Boot | ||
10410A | SMA905, MM, Ø410 µm Bore, Ø3 mm Boot | ||
10440A | SMA905, MM, Ø440 µm Bore, Ø3 mm Boot | ||
10450A | SMA905, MM, Ø450 µm Bore, Ø3 mm Boot | ||
10490A | SMA905, MM, Ø490 µm Bore, Ø3 mm Boot | ||
10510A | SMA905, MM, Ø510 µm Bore, Ø3 mm Boot | ||
10610A | SMA905, MM, Ø612 µm Bore, Ø3 mm Boot | ||
10640A | SMA905, MM, Ø641 µm Bore, Ø3 mm Boot | ||
10670A | SMA905, MM, Ø670 µm Bore, Ø3 mm Boot | ||
10720A | SMA905, MM, Ø720 µm Bore, Ø3 mm Boot | ||
10770A | SMA905, MM, Ø770 µm Bore, Ø3 mm Boot | ||
10850A | SMA905, MM, Ø850 µm Bore, Ø3 mm Boot | ||
11040A | SMA905, MM, Ø1040 µm Bore, Ø3 mm Boot | ||
11050A | SMA905, MM, Ø1050 µm Bore, Ø3 mm Boot | ||
11275A | SMA905, MM, Ø1275 µm Bore, Ø3 mm Boot | ||
11580A | SMA905, MM, Ø1580 µm Bore, Ø3 mm Boot |
The oven controller can be used to configure ramp/soak profiles for curing. Full instructions for using oven can be found in the manual. The screenshots below highlight key features of the graphical user interface.

Click to Enlarge
While curing, the controller displays the current profile(s) and the progress of the cure. The Stop button can be used to end the active cure. Other menus can be accessed by swiping the touchscreen left or right, or by tapping the options at the top of the screen.
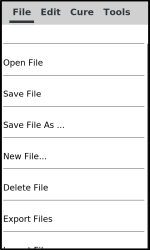
Click to Enlarge
The handset controller can open, save, create new, delete, export, and import files containing cure profiles. Exporting or importing a file will require a memory device to be connected to the USB port of the oven.
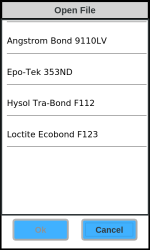
Click to Enlarge
The curing oven is preloaded with curing profiles for common fiber connector epoxies. Up to 99 profiles can be stored on the oven's controller.
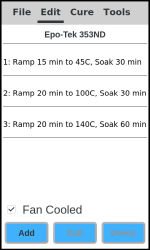
Click to Enlarge
The ramp and soak steps of the selected curing profile may be reviewed or edited. Each profile can have up to 50 steps.
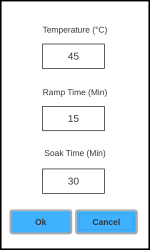
Click to Enlarge
Editing a step allows the user to alter set temperature, ramp time, and soak time.
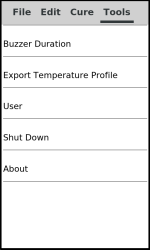
Click to Enlarge
Temperature logs may be exported on the Tools screen. See the manual for more information.
Posted Comments: | |
No Comments Posted |

Included
- Curing Oven
- Location-Specific Power Cord
- Cable Hanger(s)
- Block Insertion Tools
- Epoxy Removal Tools
Must be Purchased Separately
- Curing Blocks (One Required per Bay)
Recommended Accessories
- Guide Plates
- Compatible with Most FC/PC, FC/APC, SMA, ST®*/PC, & SC/PC Connectors
- Create and Store up to 99 Custom Ramp/Soak Curing Profiles
- 150 °C Max Temperature, ±1.5 °C Accuracy
- Ideal for Low-Volume Manufacturing and R&D
The PFC100 series of fiber connector epoxy curing ovens heats aluminum curing blocks (sold separately below) mounted inside the oven bays to cure the epoxy of up to 72 connectors simultaneously. The integrated PID temperature controller stores up to 99 custom curing profiles of 50 ramp/soak steps each (see the Programming tab for details) and temperature logging is offered via a USB port. The controller is preconfigured with curing profiles for the F112, F123, and 353NDPK fiber connector epoxies.
The removable blocks and optional guide plates can be easily swapped out and the curing parameters can be easily changed, providing flexibility and adaptability, but residual epoxy and broken fiber should be cleaned from the heater plate and curing blocks between each curing process. 13" (330 mm) tall hangers (included) attach to the back of the oven console to support patch cables during curing.
Curing Blocks
PTFE-coated, aluminum curing blocks are required and sold separately below. One block is required per bay, and two versions are available for stable retention and heating of connectors with different sizes. The blocks can be inserted and removed using hand tools included with and stored on the back of the curing oven.
Guide Plates
Solid PTFE guide plates, available below, increase the depth of the connector holes for added stability. We recommend using these when curing armored patch cables or where vertical alignment is critical.
*ST® is a registered trademark of Lucent Technologies, Inc.

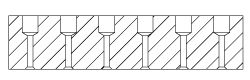
Click for Details
Curing Block Cross Section
- Support Connectors and Distribute Heat Evenly
- Up to 36 Connectors per Block
- Compatible with Ø8 - 9 mm or Ø9 - 10 mm Connectors
- Compatible Ferrule Diameter: <3.4 mm
- Black PTFE Coating to Aid Epoxy Cleanup
One curing block is required per oven bay. There are a variety of connector diameters on the market; to ensure that all fiber connectors cure evenly, the gap between the connector and the bore must be minimized. Even curing optimizes fiber performance and minimizes variation in results. Two sizes are available for stable retention and heating of various connectors with a ferrule smaller than Ø3.4 mm. Please check your connectors and choose the appropriate blocks. Using a block with smaller connectors than it's intended for will require adjustment of the set temperature to compensate for additional heat loss.
The blocks are solid aluminum with a PTFE coating for ease of epoxy cleanup. Each block features captive screws for attachment and includes a 5/32" hex key. The blocks can be inserted and removed using the hand tools included with and stored on the back of the oven console. For dimensions of the connector support holes, please click on the diagram above.
Optional PTFE guide plates are available below. These attach to the top of the curing blocks and increase the depth of the connector holes for added stability.

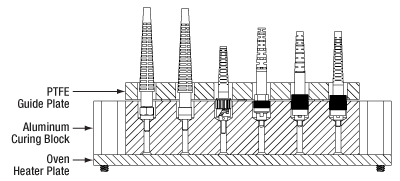
Click for Details
Assembled Cross Section with Fiber Connectors
- PTFE Extension Plate Increases Connector Stability
- Versions for Three Connector Sizes Available
These PTFE guide plates attach directly to the top of curing blocks and increase the depth of the connector holes by 10 mm for added stability. We recommend using these when curing armored patch cables or where vertical alignment is critical. Four 10-24 mounting screws and a 5/32" hex key are included with each plate.
The diagram to the right illustrates the use of a PFC10TF guide plate with a PFC10AL curing block and a variety of connectors.