Polaris® 5-Axis Kinematic Mounts
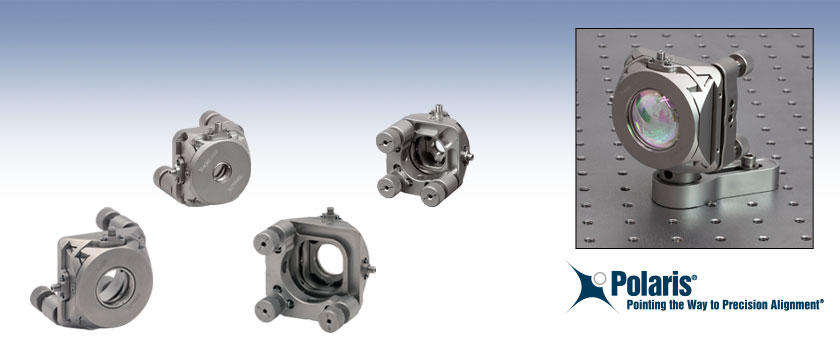
- 3 Kinematic Adjusters for Tip/Tilt and Z Travel
- SM-Threaded Mounting Bore with ±2.0 mm of X/Y Travel
- Integrated Locking Mechanisms on X & Y Axes
- Heat Treated to Minimize Temperature-Dependent Hysteresis
POLARIS-K1XY
SM1-Threaded
5-Axis Kinematic Mount
Front
Back
POLARIS-K15XY
SM1.5-Threaded Mount
Shown with Lens
POLARIS-K05XY
SM05-Threaded
5-Axis Kinematic Mount
Front
Back

Please Wait
Quick Links | |
---|---|
Ø1/2" 5-Axis Mount | |
Ø1" 5-Axis Mount | |
Ø1.5" 5-Axis Mount | |
Adjuster Knobs | |
5/64" Hex Key Adjusters | |
Lock Nuts |
Features
- Five Axes of Adjustment
- Pitch/Yaw:
- Ø1/2" Mount: ±4° at 7.7 mrad/rev
- Ø1" Mount: ±3.4° at 5.5 mrad/rev
- Ø1.5" Mount: ±3.4° at 4.8 mrad/rev
- X/Y Translation with Integrated Locking Mechanism: ±2.0 mm at 195 µm/rev
- Z Translationa:
- Ø1/2" Mount: 3 mm at 254 µm/rev
- Ø1" & Ø1.5" Mounts: 6 mm at 254 µm/rev
- Pitch/Yaw:
- SM-Threaded Bore for Mounting Optics up to 0.20" (5.0 mm) Thick
- Matched Actuators and Body Provide Stability and Smooth Kinematic Adjustment
- Extensive Testing Guarantees Less than 5 μrad Reflected Beam Shift after Temperature Cycling (See Test Data Tab for Details)
- Machined from Heat-Treated Stainless Steel with Low Coefficient of Thermal Expansion (CTE)
- Passivated Stainless Steel Surface Ideal for Vacuum and High-Power Laser Cavity Applications
Polaris® 5-Axis Kinematic Mounts are the ultimate solution for applications requiring stringent long-term alignment stability. These mounts feature a front plate with an SM05-threaded (0.535"-40), SM1-threaded (1.035"-40), or SM1.5-threaded (1.535"-40) bore for mounting optics or SM-threaded components. The tip/tilt/Z adjusters may be locked using POLARIS-LN1 lock nuts (sold separately below), and Z-axis translation is achieved using all three of the adjusters on the back plate. The X- and Y-axis translation plates are secured using a patent-pending flexure preloading mechanism that is lockable using a setscrew with a ball tip that introduces minimal angular shifts during locking and unlocking. This design provides high holding force and pointing stability while allowing quick and easy installation of the optic. The X and Y adjusters can additionally be locked using POLARIS-LN05 lock nuts. Two mounting positions are possible for right- or left-handed orientations.
Optic Retention
These mounts feature SM-threaded bores that allow a variety of optical components to be secured. A stainless steel retaining ring is included with each mount; additional retaining rings can also be purchased separately. Polaris optic bores are precision machined to achieve a fit that will provide optimum positional stability over changing environmental conditions such as temperature changes, transportation shock, and vibration. The performance will be diminished if this mount is used with optics that have an outer diameter tolerance greater than zero or smaller metric optic sizes (Ø12.5 mm, Ø25 mm, or Ø37.5 mm). To order a mount designed for metric optics, please contact Tech Support.
Design
Machined from heat-treated stainless steel, Polaris mounts utilize precision-matched adjusters with ball contacts and sapphire seats to provide smooth kinematic adjustment. As shown on the Test Data tab, these mounts have undergone extensive testing to ensure high-quality performance. The Polaris design addresses all of the common causes of beam misalignment; please refer to the Design Features tab for detailed information.
Post Mounting
These mounts are equipped with #8 (M4) counterbores for post mounting, as well as Ø2 mm alignment pin holes around the central mounting holes, allowing for precision alignments when paired with our posts for Polaris mirror mounts. See the Usage Tips tab for more recommendations about mounting configurations.
Cleanroom and Vacuum Compatibility
These mounts are designed to be compatible with cleanroom and vacuum applications. See the Specs tab and the Design Features tab for details.
Item # | POLARIS-K05XY | POLARIS-K1XY | POLARIS-K15XY |
---|---|---|---|
Optic Sizea | Ø1/2" | Ø1" | Ø1.5" |
Optic Thickness (Max) | 0.20" (5.0 mm) | ||
Tip/Tilt/Z Adjusters | 1/4"-100 Matched Actuator/Body Pairs, 5/64" (2.0 mm) Hex Drive with Removable Knobs | ||
X/Y Adjusters | 3/16"-130 Matched Actuator/Body Pairs, 5/64" (2.0 mm) Hex Drive | ||
Tip/Tilt Angular Range | ±4°, 7.7 mrad/revb | ±3.4°, 5.5 mrad/revb | ±3.4°, 4.8 mrad/revb |
X/Y Travel Range | ±2 mm / ±2 mm, 195 µm/rev | ||
Max Front Plate Travelc (Z Axis, 3 Adjuster Pitch) |
3 mm, 254 µm/rev | 6 mm, 254 µm/rev | |
Measured Point-to-Point Mechanical Resolution per Adjuster (Tip/Tilt) |
5 µrad (Typical) 2 µrad (Achievable) |
||
Measured Point-to-Point Mechanical Resolution per Adjuster (X/Y) |
5 µm (Typical) | ||
Measured Adjuster Lock (Tip/Tilt)d | 10 µrad (Typical) | ||
Measured Beam Shift from Locking Screw (per Axis)e |
15 µrad (Typical) 5 µrad (Achievable) |
||
Crosstalk (X/Y) | <3.4 µm/rev | ||
Orthogonality (X/Y) | 90.0° ± 0.5° | ||
Beam Deviation | <5 μradf | <5 μradg | <5 μradh |
Recommended Optic Mounting Torque | 5 - 18 oz-in for 5 mm Thick Optics | ||
Maximum SM-Threaded Component Mounting Torque |
15 lb-in for SM05-Threaded Parts | 30 lb-in for SM1-Threaded Parts | 40 lb-in for SM1.5-Threaded Parts |
Maximum Front Plate Payload | 0.5 lb-in (0.05 N·m) / 0.5 lb (2.3 N) | ||
Mountingi | Two #8 (M4) Counterbores at 90° | Two Sets of #8 (M4) Counterbores at 90° | |
Alignment Pin Holesj | Two at Each Counterbore | Two at Each Central Counterbore | |
Vacuum Compatibilityk | 10-9 Torr at 25 °C with Proper Bake Out; 10-5 Torr at 25 °C without Bake Out; DuPont Krytox® LVP High-Vacuum Grease Vapor Pressure: 10-13 Torr at 20 °C, 10-5 Torr at 200 °C; DuPont Krytox® XHT-BDX High-Vacuum Grease Vapor Pressure: 10-14 Torr at 20 °C, 10-6 Torr at 200 °C; EPO-TEK® 353ND Epoxy (353NDPK) Meets Low Outgassing Standards NASA ASTM E595, Telcordia GR-1221 |
||
Cleaningk | Passivated per ASTM-967 using Carpenter AAA Method | ||
Operating Temperature Range | -30 to 200 °C |
Polaris® 5-Axis Kinematic Mounts Test Data
Polaris 5-Axis Mounts have undergone extensive testing to ensure high-quality performance. Each Polaris mount had a mirror installed and torqued down to 5 oz-in with the included SM-threaded retaining ring. The mount was then installed in a temperature-controlled environment on a Ø1" stainless steel post that was secured to a stainless steel optical table. The mount had its translation axes unlocked and a beam from an independently temperature-stabilized laser diode was reflected by the mirror onto a position sensing detector.
Positional Repeatability After Thermal Shock
Purpose: This testing was done to determine how reliably the mount returns the optic, without hysteresis, to its initial position. These measurements show that the alignment of the optical system is unaffected by the temperature shock.
Procedure: The temperature of the tested mount was raised to above 32 °C, then the temperature of the mount was returned to the starting temperature. The results of this test are shown below.
Results: As can be seen in the plots below, when the Polaris mount was returned to its initial temperature, the angular position (both pitch and yaw) of the optic returned to within 5 µrad of its initial position. The performance of the mounts was tested further by subjecting them to repeated temperature change cycles. After each cycle, the mirror position reliably returned to within 5 µrad of its initial position.
Conclusions: Polaris mounts are high-quality, ultra-stable mounts that will reliably return an optic to its original position after cycling through a temperature change. As a result, these mount is ideal for use in applications that require long-term alignment stability.
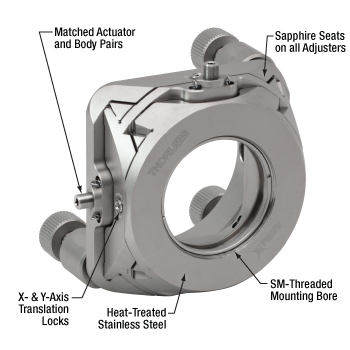
Click to Enlarge
Design Features of Polaris 5-Axis Kinematic Mounts
Several common factors typically lead to beam misalignment in an optical setup. These include temperature-induced hysteresis of the optic's position, crosstalk, drift, and backlash. Polaris optic mounts are designed specifically to minimize these misalignment factors and thus provide extremely stable performance. Hours of extensive research, multiple design efforts using sophisticated design tools such as finite element analysis software, and months of rigorous testing went into choosing the best components to provide an ideal solution for experiments requiring ultra-stable performance from a lens mount.
Thermal Hysteresis
The temperature in most labs is not constant due to factors such as air conditioning, the number of people in the room, and the operating states of equipment. Thus, it is necessary that all mounts used in an alignment-sensitive optical setup be designed to minimize any thermally induced alignment effects. Thermal effects can be minimized by choosing materials with a low coefficient of thermal expansion (CTE), like stainless steel. However, even mounts made from a material with a low CTE do not typically return the optic to its initial position when the initial temperature is restored. All the critical components of the mount are heat treated prior to assembly since this process removes internal stresses that can cause a temperature-dependent hysteresis. As a result, the alignment of the optical system will be restored when the temperature of the mount is returned to the initial temperature.
The method by which the lens is secured in the mount is another important design factor; these Polaris mounts offer excellent performance without the use of adhesives. Instead, each mount has an SM-threaded bore and a stainless steel retaining ring that holds the optic in place. The holding force provided by the stainless steel retaining ring is sufficient to keep the lens locked into place regardless of the ambient temperature. This bore also allows other SM-threaded components to be secured in the mount.
Crosstalk
Crosstalk is minimized by carefully controlling the dimensional tolerances of the plates of the mount so that the X and Y actuators are orthogonal. In addition, sapphire seats are used at both contact points. Standard metal-to-metal actuator contact points will wear down over time. The polished sapphire seats of these Polaris mounts, in conjunction with the hardened stainless steel actuator tips, maintain the integrity of the contact surfaces over time.
Drift and Backlash
In order to minimize the positional drift of the lens mount and backlash, it is necessary to limit the amount of play in the adjuster as well as the amount of lubricant used. When an adjustment is made to the actuator, the lubricant will be squeezed out of some spaces and built up in others. This non-equilibrium distribution of lubricant will slowly relax back into an equilibrium state. However, in doing so, this may cause the position of one of the mount's plates to move. The Polaris mounts use adjusters matched to the body that exceed all industry standards so very little adjuster lubricant is needed. These adjusters have a smooth feel that allows the user to make small, repeatable adjustments.
Cleanroom and Vacuum Compatibility
Polaris 5-axis kinematic mounts are designed to be compatible with cleanroom and vacuum applications. They are chemically cleaned using the Carpenter AAA passivation method to remove sulfur, iron, and contaminants from the surface. After passivation, they are assembled in a clean environment and then double vacuum bagged to eliminate contamination when transported into a cleanroom.
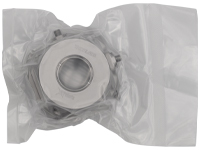
Click to Enlarge
Polaris mounts are shipped inside two vacuum bag layers.
The sapphire contacts are bonded into place using a NASA-approved low outgassing procedure. In addition, DuPont Krytox® LVP High-Vacuum Grease, an ultra-high-vacuum-compatible, low outgassing-PTFE grease, is applied to the adjusters. The grease applied to the dovetail mechanism is DuPont Krytox® XHT-BDX High-Vacuum Grease, which is also an ultra-high-vacuum-compatible, low-outgassing PTFE grease. When operating at pressures below 10-5 Torr, we highly recommend using an appropriate bake out procedure prior to installing the mount in order to minimize contamination caused by outgassing.
Cleanroom-Compatible Packaging
Each vacuum-compatible Polaris mount is packaged within two vacuum bag layers after assembly in a clean environment, as seen in the image to the right. The vacuum-tight fit of the bags stabilizes the mount, limiting translation of the front plate due to shocks during transportation. The tight fit also minimizes rubbing against the bag, preventing the introduction of bag material shavings that would contaminate the clean mount.
In the vacuum-sealing process, moisture-containing air is drawn out of the packaging. This eliminates unwanted reactions on the surface of the mount without the need for desiccant materials. The vacuum bags protect the mount from contamination by air or dust during transport and storage, and the double-vacuum bag configuration allows for a straightforward and effective cleanroom entry procedure. The outer bag can be removed outside of the cleanroom, allowing the contaminant-free inner bag to be placed into a clean container and transferred into the cleanroom while retaining the benefits of vacuum-bag packaging. Inside the cleanroom, the mount can be removed from the inner bag when ready for use.
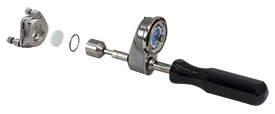
Click to Enlarge
Spanner bits and the TD24 torque driver can be used to mount optics in SM-threaded Polaris mounts.
Through thermal changes and vibrations, the Polaris 5-axis kinematic mounts are designed to provide years of use. Below are some usage tips to ensure that the mount provides optimal performance.
Mounting Considerations
Due to its relatively low coefficient of thermal expansion, stainless steel was chosen as the material from which to fabricate the front and back plates of these Polaris mounts. When mounting, we recommend using components fabricated from the same material, such as our Ø1" Posts for Polaris Mirror Mounts and Non-Bridging Clamping Arms. These posts are made of stainless steel and provide two lines of contact with the mount, which help confine the bottom of the mount during variations in the surrounding temperature, thereby minimizing potential alignment issues.
To minimize the impact of vibrations and temperature changes, it is recommended that your setup has as low of a profile as possible. Using short posts will reduce the Y-axis translation caused by temperature variations and will minimize any movements caused by vibrations. Mount the Polaris mount directly onto a flat surface such as a breadboard using a 8-32 to 1/4"-20 thread adapter (Item # AE8E25E) or M4 x 0.7 to M6 x 1.0 adapter (Item # AE4M6M). Using this mounting method, the instability introduced by a post will be eliminated.
Optic Mounting
Since an optic is prone to movement within its mounting bore, all optics should be mounted with the Polaris out of the setup to ensure accurate mounting that will minimize misalignment effects. As shown to the right, we recommend using a TD24 torque wrench with an SPB05, SPB1, or SPB1.5 Spanner Bit for SM05-, SM1-, or SM1.5-threaded Polaris mounts, respectively. See the Specs tab for recommended torques. Over torquing the optic retaining rings can result in dramatic surface distortions.
Mounting SM-Threaded Components
Since the front optic plate of the Polaris mount can move independently from the other plates, it is important to hold all the plates together while mounting SM-threaded components. This ensures that the front plate will not rotate with respect to the other plates and damage the flexure between them.
Mount Alignment
During alignment, minimized deflection will be achieved if the mount's front plate is kept parallel to the back plate. This ensures even thermal expansion of all the adjustment screws, causing the mounted optic to translate in the Z direction as opposed to rotating during temperature changes.
Front Plate Position
Although these mounts are designed to allow large tip/tilt adjustments, to achieve the best performance, it is recommended that the front plate be kept as parallel as possible to the back plate. This ensures the highest stability of the adjustments.
Lock nut installation demonstrated with the POLARIS-LN1 lock nut on one of our low-distortion Polaris mounts. To install a lock nut without cross threading, gently place the lock nut against the end of the adjuster. "Unscrew" the nut until the threads of the nut and the adjuster align; then thread the nut onto the adjuster.
Translation Limits
The X and Y axes of these mounts translate ±2.0 mm from the optic's nominal center. To prevent accidental damage to the mount, translation limit stops are placed at the ends these translation ranges. Care should be taken when actuating the adjuster screws near the limits to prevent overdriving the mount and causing damage.
The forward Z-axis travel of the front plate is measured from the shipped position (where the front and back plates are parallel and approximately 3 mm apart). The travel is limited to 3 mm for the POLARIS-K05XY mount and 6 mm for the POLARIS-K1XY and POLARIS-K15XY mounts. The installed knobs will prevent overdriving this limit, so care should be taken if the knobs are removed. There will be no limit stops to prevent damage if knobs are removed and Z translation is adjusted beyond the max travel. Note that translating the front plate backwards from the shipped position will limit the range of tip/tilt adjustment.
Polish and Clean the Points of Contact
We highly recommend that the points of contact between the mount and the post, as well as the post and the table, are clean and free of scratches or defects. For best results, we recommend using a polishing stone to clean the table’s surface and a polishing pad (Item # LF1P) for the top and bottom of the post as well as the bottom of the mount.
Not Recommended
We do not recommend taking the adjusters out of the body, as this can contaminate the threading and reduce the fine adjustment performance significantly. Also, do not pull the front plate away as it might stretch the springs beyond their operating range or crack the sapphire seats.
Adjuster Lock Nuts
These mounts feature integrated locking for X and Y axis travel. They are also compatible with the POLARIS-LN05 and POLARIS-LN1 adjuster lock nuts on the X/Y and tip/tilt/Z adjusters, respectively. For long term X/Y travel stability, we recommend using both the adjuster lock nuts and the translation locks. For applications that require frequent tuning of the adjusters, the lock nuts only need to be lightly tightened by hand to a torque of approximately 4 to 8 oz-in (0.03 to 0.06 N·m). Torque wrenches are available with preset torque values for long term stability. The TW6 wrench is set to 24 oz-in and compatible with POLARIS-LN05 lock nuts while the TW13 wrench torques POLARIS-LN1 lock nuts to 32 oz-in.
To avoid cross threading a lock nut during installation, place it against the adjuster and "unscrew" the lock nut until you feel a slight drop, then thread the lock nut onto the adjuster (see the animation to the left). Each lock nut is pre-greased with the same ultra-high-vacuum-compatible, low-outgassing PTFE grease as the Polaris mounts and has been tested for adjuster fit.
SM05 Threading: Ø1/2" Lens Tubes, 16 mm Cage Systems | |||
---|---|---|---|
External Thread, 0.535"-40.0 UNS-2A | Internal Thread, 0.535"-40.0 UNS-2B | ||
Max Major Diameter | 0.5340" | Min Major Diameter | 0.5350" |
Min Major Diameter | 0.5289" | Min Pitch Diameter | 0.5188" |
Max Pitch Diameter | 0.5178" | Max Pitch Diameter | 0.5230" |
Min Pitch Diameter | 0.5146" | Min Minor Diameter (and 83.3% of Thread) | 0.508" |
Max Minor Diameter | 0.5069" | Max Minor Diameter (and 64.9% of Thread) | 0.514" |
RMS Threading: Objective, Scan, and Tube Lenses | |||
---|---|---|---|
External Thread, 0.800"-36.0 UNS-2A | Internal Thread, 0.800"-36.0 UNS-2B | ||
Max Major Diameter | 0.7989" | Min Major Diameter | 0.8000" |
Min Major Diameter | 0.7934" | Min Pitch Diameter | 0.7820" |
Max Pitch Diameter | 0.7809" | Max Pitch Diameter | 0.7866" |
Min Pitch Diameter | 0.7774" | Min Minor Diameter (and 83.3% of Thread) | 0.770" |
Max Minor Diameter | 0.7688" | Max Minor Diameter (and 64.9% of Thread) | 0.777" |
C-Mount Threading: Machine Vision Lenses, CCD/CMOS Cameras | |||
---|---|---|---|
External Thread, 1.000"-32.0 UN-2A | Internal Thread, 1.000"-32.0 UN-2B | ||
Max Major Diameter | 0.9989" | Min Major Diameter | 1.0000" |
Min Major Diameter | 0.9929" | Min Pitch Diameter | 0.9797" |
Max Pitch Diameter | 0.9786" | Max Pitch Diameter | 0.9846" |
Min Pitch Diameter | 0.9748" | Min Minor Diameter (and 83.3% of Thread) | 0.966" |
Max Minor Diameter | 0.9651" | Max Minor Diameter (and 64.9% of Thread) | 0.974" |
SM1 Threading: Ø1" Lens Tubes, 30 mm Cage Systems | |||
---|---|---|---|
External Thread, 1.035"-40.0 UNS-2A | Internal Thread, 1.035"-40.0 UNS-2B | ||
Max Major Diameter | 1.0339" | Min Major Diameter | 1.0350" |
Min Major Diameter | 1.0288" | Min Pitch Diameter | 1.0188" |
Max Pitch Diameter | 1.0177" | Max Pitch Diameter | 1.0234" |
Min Pitch Diameter | 1.0142" | Min Minor Diameter (and 83.3% of Thread) | 1.008" |
Max Minor Diameter | 1.0068" | Max Minor Diameter (and 64.9% of Thread) | 1.014" |
SM30 Threading: Ø30 mm Lens Tubes | |||
---|---|---|---|
External Thread, M30.5 x 0.5 – 6H/6g | Internal Thread, M30.5 x 0.5 – 6H/6g | ||
Max Major Diameter | 30.480 mm | Min Major Diameter | 30.500 mm |
Min Major Diameter | 30.371 mm | Min Pitch Diameter | 30.175 mm |
Max Pitch Diameter | 30.155 mm | Max Pitch Diameter | 30.302 mm |
Min Pitch Diameter | 30.059 mm | Min Minor Diameter (and 83.3% of Thread) | 29.959 mm |
Max Minor Diameter | 29.938 mm | Max Minor Diameter (and 64.9% of Thread) | 30.094 mm |
SM1.5 Threading: Ø1.5" Lens Tubes | |||
---|---|---|---|
External Thread, 1.535"-40 UNS-2A | Internal Thread, 1.535"-40 UNS-2B | ||
Max Major Diameter | 1.5339" | Min Major Diameter | 1.535" |
Min Major Diameter | 1.5288" | Min Pitch Diameter | 1.5188" |
Max Pitch Diameter | 1.5177" | Max Pitch Diameter | 1.5236" |
Min Pitch Diameter | 1.5140" | Min Minor Diameter (and 83.3% of Thread) | 1.508" |
Max Minor Diameter | 1.5068" | Max Minor Diameter (and 64.9% of Thread) | 1.514" |
SM2 Threading: Ø2" Lens Tubes, 60 mm Cage Systems | |||
---|---|---|---|
External Thread, 2.035"-40.0 UNS-2A | Internal Thread, 2.035"-40.0 UNS-2B | ||
Max Major Diameter | 2.0338" | Min Major Diameter | 2.0350" |
Min Major Diameter | 2.0287" | Min Pitch Diameter | 2.0188" |
Max Pitch Diameter | 2.0176" | Max Pitch Diameter | 2.0239" |
Min Pitch Diameter | 2.0137" | Min Minor Diameter (and 83.3% of Thread) | 2.008" |
Max Minor Diameter | 2.0067" | Max Minor Diameter (and 64.9% of Thread) | 2.014" |
SM3 Threading: Ø3" Lens Tubes | |||
---|---|---|---|
External Thread, 3.035"-40.0 UNS-2A | Internal Thread, 3.035"-40.0 UNS-2B | ||
Max Major Diameter | 3.0337" | Min Major Diameter | 3.0350" |
Min Major Diameter | 3.0286" | Min Pitch Diameter | 3.0188" |
Max Pitch Diameter | 3.0175" | Max Pitch Diameter | 3.0242" |
Min Pitch Diameter | 3.0133" | Min Minor Diameter (and 83.3% of Thread) | 3.008" |
Max Minor Diameter | 3.0066" | Max Minor Diameter (and 64.9% of Thread) | 3.014" |
SM4 Threading: Ø4" Lens Tubes | |||
---|---|---|---|
External Thread, 4.035"-40 UNS-2A | Internal Thread, 4.035"-40.0 UNS-2B | ||
Max Major Diameter | 4.0337" | Min Major Diameter | 4.0350" |
Min Major Diameter | 4.0286" | Min Pitch Diameter | 4.0188" |
Max Pitch Diameter | 4.0175" | Max Pitch Diameter | 4.0245" |
Min Pitch Diameter | 4.0131" | Min Minor Diameter (and 83.3% of Thread) | 4.008" |
Max Minor Diameter | 4.0066" | Max Minor Diameter (and 64.9% of Thread) | 4.014" |
Posted Comments: | |
No Comments Posted |
Thorlabs offers several different general varieties of Polaris mounts, including kinematic side optic retention, SM-threaded, low optic distortion, piezo-actuated, vertical drive, and glue-in optic mounts, a fixed monolithic mirror mount and fixed optic mounts, XY translation mounts, 5-axis kinematic mount, and a kinematic platform mount. Refer to the tables below for our complete line of Polaris mounts, grouped by mount type, optic bore size, and then arranged by optic retention method and adjuster type (or intended application in the case of fixed mounts). We also offer a line of accessories that have been specifically designed for use with our Polaris mounts; these are listed in the table to the lower right. Note that the tables below list Item # suffixes that omit the "POLARIS" prefix for brevity. Click the photos below for details.
Polaris Mount Adjuster Types | |||||
---|---|---|---|---|---|
Side Hole | Hex | Adjuster Knobs | Adjuster Lock Nuts |
Piezo Adjusters | Vertical-Drive Adjusters |
![]() |
![]() |
![]() |
![]() |
![]() |
![]() |
Polaris Kinematic Mounts for Round Optics | ||||
---|---|---|---|---|
Optic Retention Method | Side Lock | SM Threaded | Low Distortion | Glue-In |
Ø1/2" Optics | ||||
2 Side Hole Adjusters | - | - | - | -K05C4 -K05G4 |
2 Hex Adjusters | -K05S1 | -K05T1 | -K05F1 | - |
2 Adjusters with Lock Nuts | -K05S2 | -K05T2 | -K05F2 | - |
2 Piezoelectric Adjusters | -K05P2 | - | - | - |
2 Vertical Adjusters | -K05VS2 -K05VS2L |
- | - | - |
3 Hex Adjusters | -K05 | - | - | - |
3 Adjusters with Lock Nuts | - | -K05T6 | -K05F6 | - |
3 Adjuster Knobs (Tip/Tilt/Z) & 2 Hex Adjusters (X/Y) |
- | -K05XY | - | - |
Ø19 mm (3/4") Optics | ||||
2 Side Hole Adjusters | -K19S4 | - | -K19F4/M | -K19G4 |
Ø25 mm Optics | ||||
2 Side Hole Adjusters | -K25S4/M | - | -K25F4/M | - |
Ø1" Optics | ||||
2 Side Hole Adjusters | -K1S4 | - | - | -K1C4 -K1G4 |
2 Hex Adjusters | -K1E2 -K1-2AH |
-K1T2 | -K1F2 | - |
2 Adjuster Knobs | - | -K1T1 | -K1F1 | - |
2 Piezoelectric Adjusters | -K1S2P | - | - | - |
2 Vertical Adjusters | -K1VS2 -K1VS2L |
- | - | - |
3 Side Hole Adjuster | -K1S5 | - | - | - |
3 Hex Adjusters | -K1E3 -K1-H |
-K1T3 | - | - |
3 Adjuster Knobs | -K1E -K1 |
-K1T | -K1F | - |
3 Piezoelectric Adjusters | -K1S3P | - | - | - |
3 Adjuster Knobs (Tip/Tilt/Z) & 2 Hex Adjusters (X/Y) |
- | -K1XY | - | - |
Optic Retention Method | Side Lock | SM Threaded | Low Distortion | Glue-In |
Ø1.5" Optics | ||||
2 Side Hole Adjusters | -K15S4 | - | -K15F4 | - |
2 Vertical Adjusters | -K15VS2 -K15VS2L |
- | - | - |
3 Adjuster Knobs (Tip/Tilt/Z) & 2 Hex Adjusters (X/Y) |
- | -K15XY | - | - |
Ø50 mm Optics | ||||
2 Side Hole Adjusters | -K50S4/M | - | -K50F4/M | - |
Ø2" Optics | ||||
2 Hex Adjusters | -K2S2 | -K2T2 | -K2F2 | - |
2 Adjuster Knobs | -K2S1 | -K2T1 | -K2F1 | - |
2 Piezoelectric Adjusters | -K2S2P | - | - | - |
2 Vertical Adjusters | -K2VS2 -K2VS2L |
- | - | - |
3 Hex Adjusters | -K2S3 | -K2T3 | -K2F3 | - |
3 Adjuster Knobs | -K2 | -K2T | -K2F | - |
Ø3" Optics | ||||
2 Side Hole Adjusters | -K3S4 | - | - | - |
3 Side Hole Adjusters | -K3S5 | - | - | - |
Ø4" Optics | ||||
2 Side Hole Adjusters | - | - | -K4F4 | - |
Ø6" Optics | ||||
2 Side Hole Adjusters | - | - | -K6F4 | - |
Polaris XY Translation Mounts for Round Optics | ||
---|---|---|
Optic Retention Method | SM Threaded | Representative Photos |
Ø1/2" Optics | ![]() ![]() |
|
2 Hex Adjusters (X/Y) | -05CXY | |
-05XY | ||
3 Adjuster Knobs (Tip/Tilt/Z) & 2 Hex Adjusters (X/Y) |
-K05XY | |
Ø1" Optics | ||
2 Hex Adjusters (X/Y) | -1XY | |
3 Adjuster Knobs (Tip/Tilt/Z) & 2 Hex Adjusters (X/Y) |
-K1XY | |
Ø1.5" Optics | ||
2 Hex Adjusters (X/Y) & 3 Adjuster Knobs (Tip/Tilt/Z)zzz |
-K15XY |
Polaris Fixed Mounts for Round Optics | ||||||
---|---|---|---|---|---|---|
Optic Retention Method | Side Lock | Low Distortion |
Glue-In | Representative Photos |
||
Ø1/2" Optics | ![]() ![]() ![]() ![]() |
|||||
Optimized for Mirrors | - | -B05F | -C05G | |||
Optimized for Beamsplitters | -B05S | - | -B05G | |||
Optimized for Lenses | - | - | -L05G | |||
Ø19 mm (Ø3/4") Optics | ||||||
Optimized for Mirrors | -19S50/M | - | - | |||
Ø1" Optics | ||||||
Optimized for Mirrors | - | -B1F | -C1G | |||
Optimized for Beamsplitters | -B1S | - | -B1G | |||
Optimized for Lenses | - | - | -L1G | |||
Ø2" Optics | ||||||
Optimized for Mirrors | - | -B2F | -C2G | |||
Optimized for Beamsplitters | -B2S | - | - |
Polaris Kinematic 1.8" x 1.8" Platform Mount | ||
---|---|---|
Optomech Retention Method | Tapped Holes & Counterbores |
![]() |
2 Adjuster Knobs | -K1M4(/M) |
Accessories for Polaris Mounts | |
---|---|
Description | Representative Photos |
Ø1/2" Posts for Polaris Mounts | ![]() |
Ø1" Posts for Polaris Mounts | |
Non-Bridging Clamping Arms | ![]() |
45° Mounting Adapter | ![]() |

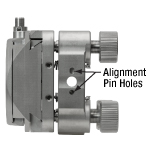
Click to Enlarge
Polaris mounts have two holes for Ø2 mm alignment pins by the #8 (M4) mounting bores for alignment.
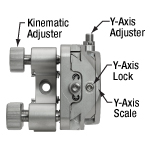
Click to Enlarge
Kinematic and Y-axis translation features are shown above. The X-axis adjuster and lock are also visible but not labelled.
- SM05 (0.535"-40) Threading for Mounting Ø1/2" Optics up to 0.20" (5 mm) Thick
- ±4° Tip/Tilt Range
- ±2.0 mm X/Y Translation Range and 3 mm Z Translation
- Matched Actuator/Body Pairs
- <5 µrad Deviation after 13.5 °C Temperature Cycling (See the Test Data Tab for Details)
The POLARIS-K05XY 5-Axis Kinematic Mount for Ø1/2" Optics offers ±4° of tip/tilt adjustment, ±2.0 mm of X/Y travel, and 3 mm of Z translation and is designed to provide easy high-resolution adjustment and long-term alignment stability. The mount features a patent pending flexure preloading mechanism that keeps the translation smooth and repeatable. It is also designed to be compatible with cleanroom and vacuum applications.
The POLARIS-K05XY mount features three 1/4"-100 adjusters for tip/tilt/Z translation and two 3/16"-130 adjusters for X/Y translation. The tip/tilt/Z actuators feature removable knobs and all five actuators have 5/64" (2.0 mm) hex drives. With the knobs removed, all actuators may be adjusted with our HKTS-5/64 Hex Key Thumbscrews (sold separately below), the hex on the end of the SA1 tool, or any other 5/64" (2.0 mm) hex wrench.
The tip/tilt/Z adjusters can be locked using POLARIS-LN1 lock nuts (sold separately below) and the X/Y travel adjusters on this mount can be locked using the integrated translation locks with a 5/64" (2.0 mm) hex or with POLARIS-LN05 lock nuts (also sold separately below). Note that the integrated locks for the X and Y axes are adjacent to the adjuster for the other axis, as illustrated for the Y-axis in the left photo above. For long-term X/Y locking stability, we recommend using both the adjuster lock nuts and the translation locks.
A stainless steel retaining ring (included) is used to hold optics up to 0.20" (5 mm) thick. Additional retaining rings (Item # POLARIS-SM05RR) can also be purchased separately. This mount is also equipped with two engraved X- and Y-axis scales that provide a translation reference with 0.5 mm tick spacing.
Post mounting is provided by two #8 (M4) bores at 90°. For custom mounting configurations, two holes for Ø2 mm alignment pins are located on each mounting face (as shown in the photo above) for setting a precise location and mounting angle. Standard DIN 7-m6 ground dowel pins are recommended. We recommend using this mount with a stainless steel post, such as our Ø1" Posts for Polaris Mirror Mounts.
Please note that this mount is designed for Ø1/2" optics and is not intended for use with Ø12.5 mm metric optics.

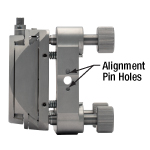
Click to Enlarge
Polaris mounts have two holes for Ø2 mm alignment pins by the #8 (M4) mounting bores for alignment.
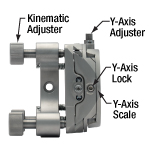
Click to Enlarge
Kinematic and Y-axis translation features are shown above. The X-axis adjuster and lock are also visible but not labelled.
- SM1 (1.035"-40) Threading for Mounting Ø1" Optics up to 0.20" (5 mm) Thick
- ±3.4° Tip/Tilt Range
- ±2.0 mm X/Y Translation Range and 6 mm Z Translation
- Matched Actuator/Body Pairs
- <5 µrad Deviation after 9 °C Temperature Cycling (See the Test Data Tab for Details)
The POLARIS-K1XY 5-Axis Kinematic Mount for Ø1" Optics offers ±3.4° of tip/tilt adjustment, ±2.0 mm of X/Y travel, and 6 mm of Z translation and is designed to provide easy high-resolution adjustment and long-term alignment stability. The mount features a patent pending flexure preloading mechanism that keeps the translation smooth and repeatable. It is also designed to be compatible with cleanroom and vacuum applications.
The POLARIS-K1XY mount features three 1/4"-100 adjusters for tip/tilt/Z translation and two 3/16"-130 adjusters for X/Y translation. The tip/tilt/Z actuators feature removable knobs and all five actuators have 5/64" (2.0 mm) hex drives. With the knobs removed, all actuators may be adjusted with our HKTS-5/64 Hex Key Thumbscrews (sold separately below), the hex on the end of the SA1 tool, or any other 5/64" (2.0 mm) hex wrench.
The tip/tilt/Z adjusters can be locked using POLARIS-LN1 lock nuts (sold separately below) and the X/Y travel adjusters on this mount can be locked using the integrated translation locks with a 5/64" (2.0 mm) hex or with POLARIS-LN05 lock nuts (also sold separately below). Note that the integrated locks for the X and Y axes are adjacent to the adjuster for the other axis, as illustrated for the Y-axis in the left photo above. For long-term X/Y locking stability, we recommend using both the adjuster lock nuts and the translation locks.
A stainless steel retaining ring (included) is used to hold optics up to 0.20" (5 mm) thick. Additional retaining rings (Item # POLARIS-SM1RR) can also be purchased separately. This mount is also equipped with two engraved X- and Y-axis scales that provide a translation reference with 0.5 mm tick spacing.
Post mounting is provided by two #8 (M4) bores at 90°. For custom mounting configurations, two holes for Ø2 mm alignment pins are located on each mounting face (as shown in the photo above) for setting a precise location and mounting angle. Standard DIN 7-m6 ground dowel pins are recommended. We recommend using this mount with a stainless steel post, such as our Ø1" Posts for Polaris Mirror Mounts.
Please note that this mount is designed for Ø1" optics and is not intended for use with Ø25 mm metric optics.

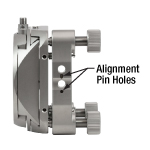
Click to Enlarge
Polaris mounts have two holes for Ø2 mm alignment pins by the central #8 (M4) mounting bore for alignment.
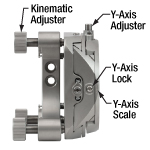
Click to Enlarge
Kinematic and Y-axis translation features are shown above. The X-axis adjuster and lock are also visible but not labelled.
- SM1.5 (1.535"-40) Threading for Mounting Ø1.5" Optics up to 0.20" (5 mm) Thick
- ±3.4° Tip/Tilt Range
- ±2.0 mm X/Y Translation Range and 6 mm Z Translation
- Matched Actuator/Body Pairs
- <5 µrad Deviation after 15 °C Temperature Cycling (See the Test Data Tab for Details)
The POLARIS-K15XY 5-Axis Kinematic Mount for Ø1.5" Optics offers ±3.4° of tip/tilt adjustment, ±2.0 mm of X/Y travel, and 6 mm of Z translation and is designed to provide easy high-resolution adjustment and long-term alignment stability. The mount features a patent pending flexure preloading mechanism that keeps the translation smooth and repeatable. It is also designed to be compatible with cleanroom and vacuum applications.
The POLARIS-K15XY mount features three 1/4"-100 adjusters for tip/tilt/Z translation and two 3/16"-130 adjusters for X/Y translation. The tip/tilt/Z actuators feature removable knobs and all five actuators have 5/64" (2.0 mm) hex drives. With the knobs removed, all actuators may be adjusted with our HKTS-5/64 Hex Key Thumbscrews (sold separately below), the hex on the end of the SA1 tool, or any other 5/64" (2.0 mm) hex wrench.
The tip/tilt/Z adjusters can be locked using POLARIS-LN1 lock nuts (sold separately below) and the X/Y travel adjusters on this mount can be locked using the integrated translation locks with a 5/64" (2.0 mm) hex or with POLARIS-LN05 lock nuts (also sold separately below). Note that the integrated locks for the X and Y axes are adjacent to the adjuster for the other axis, as illustrated for the Y-axis in the left photo above. For long-term X/Y locking stability, we recommend using both the adjuster lock nuts and the translation locks.
A stainless steel retaining ring (included) is used to hold optics up to 0.20" (5 mm) thick. Additional retaining rings can also be purchased separately by contacting Tech Support. This mount is also equipped with two engraved X- and Y-axis scales that provide a translation reference with 0.5 mm tick spacing.
Post mounting is provided by four #8 (M4) bores. For custom mounting configurations, two holes for Ø2 mm alignment pins are located on each mounting face (as shown in the photo above) for setting a precise location and mounting angle. Standard DIN 7-m6 ground dowel pins are recommended. We recommend using this mount with a stainless steel post, such as our Ø1" Posts for Polaris Mirror Mounts.
Please note that this mount is designed for Ø1.5" optics and is not intended for use with Ø37.5 mm metric optics.

- For Convenient Adjustment of 5/64" and 2 mm Hex-Driven Actuators
- Red Anodized Adjustment Knob with Engraved Hex Size
- Replaceable Hex Tip
- Sold in Packages of 4
These 5/64" Hex Key Adjuster Thumbscrews allow for quick adjustment of many 5/64" and 2 mm hex-driven actuators (or standard actuators with the knobs removed). These temporary knobs can be left in the screw's hex socket between adjustments for convenience (see photo to the right). An 8-32 setscrew (5/64" hex) secures the replaceable hex bit, which can be reversed if the tip is stripped. Contact Tech Support to order replacement hex key bits.
We offer hex key thumbscrews in sizes from 0.050" to 3/16" and 2 mm to 5 mm.

To install a lock nut without cross threading, gently place the lock nut against the end of the adjuster. "Unscrew" the nut until the threads of the nut and the adjuster align before threading the nut onto the adjuster. This animation shows the installation of a POLARIS-LN1 lock nut on a POLARIS-K1F1 low distortion mount.
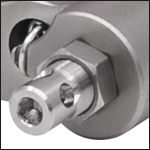
Click for Details
POLARIS-LN05 Lock Nuts on a POLARIS-K19S4 Mount
- Provide Long-Term Adjuster Stability
- Compatible with Select Polaris Mounts
- POLARIS-LN05 Lock Nut has 3/16"-130 Internal Threading
- POLARIS-LN1 Lock Nut has 1/4"-100 Internal Threading
These lock nuts are designed for use with Polaris kinematic mounts that do not use low-profile adjusters. The POLARIS-LN05 lock nut can be used with 3/16"-130 adjusters, while the POLARIS-LN1 lock nut is for 1/4"-100 adjusters. Designed for long-term adjuster stability or applications that are exposed to shock and vibration, these lock nuts are pre-greased with the same ultra-high-vacuum-compatible, low-outgassing PTFE grease as the Polaris mounts and have been tested for adjuster fit.
For applications that require frequent tuning of the adjusters, the lock nuts only need to be lightly tightened by hand to a torque of approximately 4 to 8 oz-in (0.03 to 0.06 N·m). If long-term stability is required, the torque wrenches below can be used to apply the appropriate amount of torque to each lock nut (see the table below for torque values). POLARIS-LN05 lock nuts require a 6 mm hex tool for tightening, while POLARIS-LN1 lock nuts require a 13 mm hex tool. To avoid cross threading the lock nut, place it against the adjuster and "unscrew" the lock nut until you feel a slight drop; then thread the lock nut onto the adjuster.

- Provides Long-Term Adjuster Stability
- Compatible with Select Polaris Mounts
- Low Profile: Ø0.33" (Ø8.4 mm) x 0.08" (1.9 mm) Thick
- Tighten Along Rotational Axis Using the POLARIS-T2 Spanner Wrench
This locking collar is compatible with Polaris mounts that have 1/4"-100 adjusters, excluding the piezo-driven mounts and mounts with low-profile adjusters (Item #s POLARIS-K1E3 and POLARIS-K1E2). Designed for long-term adjuster stability or applications that are exposed to shock and vibration, these locking collars are pre-greased with the same ultra-high-vacuum-compatible, low-outgassing PTFE grease as the Polaris mounts and have been tested for adjuster fit.
The POLARIS-T2 spanner wrench has been specifically designed for use in securing the POLARIS-LNS1 locking collar. The double spanner head enables complete engagement while the design allows locking collar adjustments to be along the same line as the adjuster itself. A center through hole allows a 2 mm ball driver to pass through the spanner wrench, so that the adjuster can be held in position while the locking collar is engaged.
For applications that require frequent tuning of the adjusters, the locking collar only needs to be lightly tightened to a torque of approximately 4 to 8 oz-in (0.03 to 0.06 N·m). For long-term stability, we recommend tightening to a torque of 32 oz-in, which can be achieved by using our TW13 preset torque wrench (sold below) in combination with the POLARIS-T2 spanner wrench. To avoid cross threading the locking collar, place it against the adjuster and "unscrew" the collar until you feel a slight drop; then thread the collar onto the adjuster.

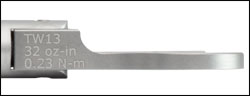
Click to Enlarge
Each wrench is engraved with its preset torque value and Item #.
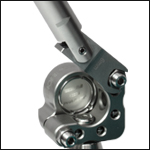
Click for Details
TW6 Torque Wrench Used to Secure POLARIS-LN05 Lock Nut on POLARIS-K05T2 Mirror Mount
- Preset Wrenches for Polaris Lock Nuts & Spanner Wrenches (See Table Below for Compatibility):
- TW6: 6 mm Hex, 24 oz-in
- TW13: 13 mm Hex, 32 oz-in
- Break-Over Design Ensures Proper Torque is Applied
- Ideal for Applications Requiring Long-Term Locking
These torque wrenches have a preset torque value to secure the lock nuts on Polaris mounts for long-term locking; see the table below for specifications. When the preset torque value has been achieved, the break-over design will cause the pivoting joint to "break," as shown to the lower right. The wrench's hex head will move back into place once the force is removed. This design prevents further force from being applied to the lock nut. Engraved guidelines indicate the angle the wrench should pivot in order to apply the specified torque; pivoting the handle past these guidelines will over-torque the lock nut. Each wrench is also engraved with its preset torque value, torque direction, wrench size, and Item # for easy identification in the field.
These wrenches are designed to be compatible with cleanroom and vacuum chamber applications. They are chemically cleaned using the Carpenter AAA passivation method to remove sulfur, iron, and contaminants from the surface. After passivation, they are assembled in a clean environment and double vacuum bagged to eliminate contamination when transported into a cleanroom. Every wrench has a bead-blasted finish to minimize reflections when working with setups that include lasers.
Please note that these wrenches are not intended for use in applications where adjusters are frequently tuned, as these applications typically require torque values of 4 to 8 oz-in (0.03 to 0.06 N·m).
Item # | Hex | Torque | Torque Accuracy | Compatible Items |
---|---|---|---|---|
TW6 | 6 mm | 24 oz-in (0.17 N•m) | ±1.44 oz-in (0.010 N•m) | POLARIS-LN05 3/16"-130 Lock Nut |
TW13 | 13 mm | 32 oz-in (0.23 N•m) | ±1.92 oz-in (0.014 N•m) | POLARIS-LN1 1/4"-100 Lock Nut POLARIS-LN4 3/8"-100 Lock Nut POLARIS-T2 Spanner Wrench for POLARIS-LNS1 Locking Collar POLARIS-T3 Spanner Wrench for POLARIS-LNS05 Locking Collar |

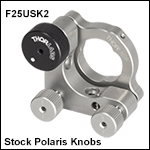
Click to Enlarge
F25USK2 Knob Shown Attached to a POLARIS-K1E Mirror Mount
- Ø0.925" Knob for Additional Angular Resolution
- Clearance Hole Allows Access to Hex Socket of the Adjuster
This removable adjustment knob is compatible with many of our 1/4"-100 adjusters, including those used in the Ø1", Ø1.5", and Ø2" Polaris Kinematic Mounts and our Polaris Kinematic Platform Mount. The larger Ø0.925" size provides additional angular resolution over the standard Polaris knobs.
Please note that the F25USK2 knob is not compatible with Polaris mounts that use side-hole adjusters. The recessed bore of knob is not deep enough to allow the knob to engage the threads on the side-hole adjuster.