Tape
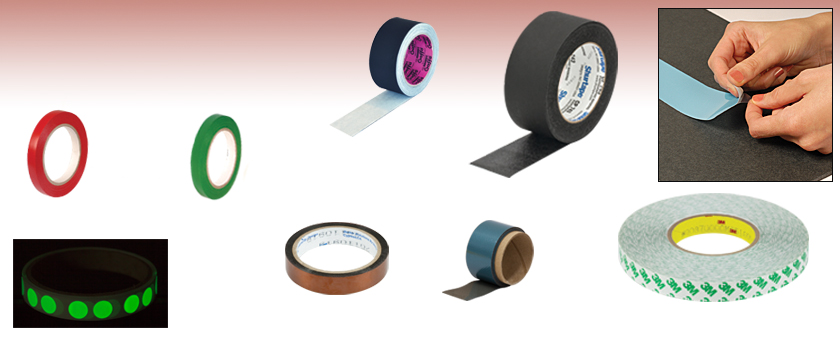
- Black Masking Tape
- Color and Photoluminescent Vinyl Tape
- Double-Sided Adhesive Tape
- Conductive and Insulating Tapes
VTR-050
Red Vinyl Tape
VTG-050
Green Vinyl Tape
T205-1.0
Black Aluminum
Foil Tape
T743-2.0
Black Masking Tape
PLT2
Photoluminescent
Stickers (Shown
with the Lights off)
KAP22-075
Insulating Kapton Tape
TCDT1
Thermally Conductive
Double-Sided Tape
DST1950
Double-Sided Tape
TCDT2

Please Wait
Thorlabs offers various types of tape for many different lab applications.
Our tape selections include the following:
- High-Performance or Standard Black Masking Tape
- Aluminum Foil Blackout Tape
- Colored Vinyl Tape (Red, Yellow, or Green)
- Double-Sided Adhesive Tape
- Double-Sided Optically Clear Adhesive Tape
- Double-Sided Conductive Tape
- Insulating Kapton Tape
- Photoluminescent Stickers
Summary of Lamination Process | ||
---|---|---|
Pre-Bake in Dry, Clean Oven (Plastic Substrate Only) |
Temperature | 85 °C |
Duration | 2 - 5 Hours | |
Sample Preparation | Environment | Class 10K Cleanroom or Better |
Temperature | ≥24 °C | |
Tools | Wipes, Air Ionizer Gun, Isopropyl Alcohol | |
Lamination | Environment | Class 10K Cleanroom or Better |
Temperature | ≥24 °C | |
Tools | Vacuum Table or Polyester Tape, Roller | |
Autoclave | Temperature | 30 - 60 °C |
Pressure | 70 - 100 PSI | |
Duration | 20 - 60 Minutes |
Recommended Tools and Environmental Conditions for
OCA8146-2 & OCA8146-3
- Class 10K Cleanroom or Better
- Vacuum Table or Glass Table Work Station
- Clean Rubber Roller, Autoclave, and Polyester Tape
- Wipes without Free Floating Fibers, Air Ionizer Gun, and Isopropyl Alcohol
3M's Optically Clear Double-Sided Adhesive Tape (OCA) offers exceptional bonding for smooth, transparent substrates such as glass or plastic. Plastic substrates (e.g., PC and PMMA) absorb moisture and outgas when exposed to high temperature or humidity. This causes bubbles to appear in laminated parts and reduces the optical transparency. To avoid this potential problem, plastics can be baked at 85 °C for 2 - 5 hours in order to drive the moisture out of the substrate. The table to the right gives a summary of the steps in the lamination process detailed below.
Lamination Process
Substrate Preparation
1) If using a plastic substrate, bake it at 85 °C for 2 - 5 hours. Before laminating a substrate first clean all surfaces to be bonded together. Use a soft, dust-free cloth or wipe (such as Thorlabs' CP-100 Premium Optical Cleaning Pads) and isopropyl alcohol to clean the substrate surfaces. Inspect the surfaces to ensure that they are clean, dry, and free of dust and other contaminants.
2) Secure the first substrate to a flat, clean surface with the cleaned side up. Ideally the substrate will be secured with a vacuum table, but in the absence of such, polyester masking tape can be used to secure the substrate.
Lamination
3) Remove the first liner from the OCA film. The OCAs come with three tape handles on each sheet to aid the user in removing the film without touching the OCA (see image to the right).
4) Align the OCA with the substrate and use the rubber roller to adhere the OCA onto the secured substrate. Be sure to squeeze out all the air to avoid air pockets in the lamination.
5) Remove the back side liner and align the second substrate (cleaned surface facing the OCA). Roll down on the second substrate to squeeze all the air from the laminated surfaces.
Autoclave
6) An autoclave is typically used as the final step in the lamination process. It uses heat and pressure to squeeze out any remaining air from the laminated surfaces. For the purpose of lamination, a dry autoclave must be used. See the table above for the autoclave settings. After the autoclave is complete, the lamination process if finished.
Posted Comments: | |
jean-francois lupi
 (posted 2021-11-10 08:37:59.11) Hi,
I have a question concerning tour double-sided tape (DST1950) :
is this product waterproof ? jgreschler
 (posted 2021-12-01 09:34:04.0) Thank you for reaching out to Thorlabs. 3M has confirmed that this tape achieves an IP67 rating when applied dry (dust proof, 1m water submersion for 30 minutes). In most cases water resistance will last much longer but it is not intended for continuous water immersion. Tapes do have a WVTR (water vapor transmission rate) and will eventually pass on some water vapor. Ivo Aubrecht
 (posted 2019-06-18 07:34:13.99) What is the carrier of your black masking types? What is the thickness?
I would like to use a laser marker (at 1064nm, 10W) for cutting openings of various types in them and use them as masks in exposition of photoresist plates. Another application would be for defining an area of interest on a sample before its inspection by means of various devices - a microscope, a scatterometer, a spectrometer etc. In either case low tack and absolutely no residua after removing the mask is essential.
I have had some experience with a low tack black tape for advertising purposes which I use to minimize reflections by the rear side of a photoresist plate. I verified that I can cut the opening with that laser marker.
I would like to test your tapes too. I am planning to attend Laser World of ..2019 in Munich.
Would it be possible to get sample amounts of the types (some 50-100cm)?
Any recommendations which of the types would suit best? llamb
 (posted 2019-06-18 09:21:43.0) Thank you for contacting Thorlabs. Our T137- tape is 0.0049" thick. Our T743- tape is 0.0065" thick. Our T205- tape is 0.0035" thick. I have reached out to you directly to discuss your application further and to discuss possible samples. |

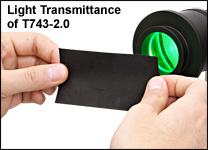
Click to Enlarge
High-Performance Black Masking Tape
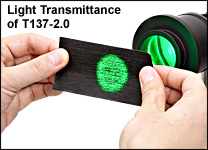
Click to Enlarge
Black Masking Tape
- 1" (25 mm) and 2" (50 mm) Wide Versions Available
- Paper-Based Masking Tape for General Purpose or Blackout Applications
- Aluminum Foil Tape for Total Blackout Applications
- Can be Torn by Hand and Removed Easily Without Leaving Residue
- Not Intended for Use in Laser Safety Applications
Thorlabs offers a standard and high-performance black masking tape, as well as an aluminum foil masking tape. All types of tape can be torn by hand, are easy to remove, and do not leave a residue. The T137-1.0 and T137-2.0 black masking tape can be used for general applications. For applications requiring minimal ambient light transmission, the T743-1.0 or T743-2.0 high-performance black masking tape is recommended. For total blackout requirements or high-power applications, we offer the T205-1.0 or T205-2.0 non-reflective, flame-retardant aluminum tape. This foil tape has been tested to withstand up to 10 seconds of exposure from a 20 W, Ø6 mm, 10.6 µm laser beam.
In the photographs shown above, a collimated LED (Item # M530L2-C2) with approximately 170 mW output power was used to illustrate how the T743-2.0 high-performance tape allows very little light transmission as compared to the T137-2.0 standard black masking tape. The table below gives the measured power and percent transmittance when various wavelengths of light were incident upon each type of tape.
Black Tape Performance | |||
---|---|---|---|
Incident Power | Measured Output Power (% Transmittance) | ||
T137-2.0 Masking Tape | T743-2.0 High-Performance Masking Tape | T205-2.0 Aluminum Foil Tape | |
1.07 mW at 635 nm | 1.34 µW (0.13%) | 0.90 µW (0.08%) | Zero (0%) |
4.79 mW at 635 nm | 5.92 µW (0.12%) | 0.24 µW (<0.01%) | Zero (0%) |
1.41 mW at 632.991a | 3.36 µW (0.24%) | 0.012 µW (<0.01%) | Zero (0%) |
20.34 mW at 850 nmb | 28.74 µW (0.14%) | 1.04 µW (<0.01%) | 0.0006 µW (<1 x 10-5%) |

- 1/2" (12.7 mm) Wide Vinyl Tape
- 108' (32.9 m) Long Roll
- Available in Red, Green, or Yellow
Colored rolls of vinyl tape are ideal for color coding fibers cables, electrical cables, tools, and samples. The semi-gloss finish can be written on with permanent marker, and the tape can be used in environments from 40 °F to 170 °F (5 °C to 76 °C), although it is best to apply the tape at room temperature.

- White, Double-Sided Tape with 3M Adhesive 375
- 10.2 mils (0.26 mm) Thick
- 3/4" Wide x 180' Long (19 mm x 55 m)
- Bonds on Contact to Almost any Surface
- Bonds are Durable with High Peel and Shear Strength
- Resistance to UV Light, Solvents, Plasticizers, and High Temperatures
This 3M tape is 10.2 mils (0.26 mm) thick, double-coated with 375 adhesive, and is made from PVC. The tape features a high peel and shear strength, excellent resistance to UV light, good solvent and plasticizer resistance, and long-term temperature performance up to 158 °F. There are many applications for the tape including mounting optics, hardware, fiber, sensors, etc.

- 3M Optically Clear Double-Sided Acrylic Adhesive Tape
- >99% Transmission and <1% Haze Level
- Alternative to UV-Cured Optical Adhesives
- Provides a High Bond Strength to a Variety of Surfaces
- Sold in a Pack of 20 Sheets
3M's Optically Clear Double-Sided Tape provides high cohesive and peel strength to reliably bond many transparent substrates or optical devices and is an alternative to our UV-curing optical adhesive. This tape is ideal for bonding optical films together, such as a lenslet foil to a polarizer foil or glass substrate. Additionally, it can be used with bare Indium Tin Oxide (ITO) surfaces. Two thicknesses are available, 2 mils (0.050 mm) and 3 mils (0.075 mm); the thinner sheet offers slightly better transmission where as the thicker sheet is less likely to tear or break during application.
When properly applied, it can resist splashes from acetone, isopropyl alcohol, and cleaners. Furthermore, immersion in water has no measurable effect on the strength and durability of the tape’s bond. For maximum bond strength, the surfaces of the mating pieces should be thoroughly cleaned and dried.
This optically clear, double-sided tape offers high temperature resistance as well as long-term durability without yellowing, delaminating, or degrading. A pressure-sensitive rotary cutter may be used to cut the sheets if necessary. See the Tape Bonding tab for detailed instructions on how to use this tape.
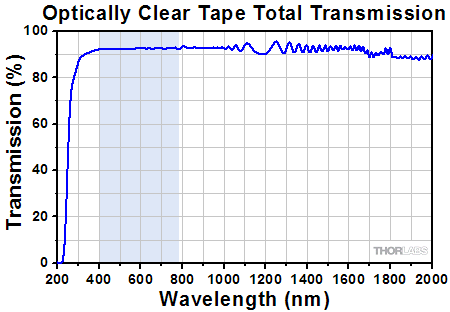
Click to Enlarge
Total transmission through one sheet of OCA8146-3 optically clear tape. The shaded region highlights the designed wavelength range for the tape. The transmission for the OCA8146-2 will be similar to this plot, but with slightly better performance.
Item # | OCA8146-2 | OCA8146-3 |
---|---|---|
Wavelength Range | 400 - 780 nm | |
Material | Acrylic | |
Sheet Size | 250 mm × 210 mm (9.84" × 8.27") |
250 mm × 195 mm (9.84" × 7.68") |
Sheet Thickness | 2 mils (0.050 mm) | 3 mils (0.075 mm) |
Transmissiona | >99% | |
Haze Levelb | <1% | |
Refractive Index @ 589.3 nm | 1.4740 ± 0.0005 @ 25 °C | |
Dielectric Constant | 5.14 @ 1 kHz | |
Peel Adhesion to Glassc | 54 N/100 mm | 58 N/100 mm |
Short Term Temperature | 177 °C (Max) | |
Long Term Temperature | -40 to 85 °C |

- Thermally Conductive Double-Sided Acrylic Adhesive Tape
- 0.009" (0.229 mm) Thick
- Two Options:
- TCDT1: 1" Wide x 48" Long (25.4 mm x 1219 mm)
- TCDT2: 2" Wide x 24" Long (50.8 mm 610 mm)
- Great Alternative to Heat-Cured Adhesives, Screw Mounting, or Clip Mounting
- Provides a High Bond Strength to a Variety of Surfaces
- Can be Removed without Damaging Parts
The thermally conductive, double-sided tape consists of a superior bond strength, pressure-sensitive acrylic adhesive loaded with titanium diboride and applied to an expanded aluminum carrier. The tape is embossed with an innovative pattern for maximum conformability and minimal air pockets and offers excellent thermal, mechanical, environmental, and chemical properties. Our thermally conductive double-sided tape can bond heat sinks and thermal plates to components without the use of clips, screws, other mechanical fasteners, or additional thermal compounds and can be removed after the application without damage to the component.
Usage Instructions
This tape requires pressure to bond. At room temperature, we recommend holding components together with a minimum of 10 psi for 15 seconds, or preferably 30 psi for 5 seconds.
Before application, ensure that bonding surfaces are free from oil, dust, or any contamination that may affect bonding. Wearing gloves, wipe surfaces with a clean, lint-free cloth dampened with industrial solvents such as acetone or isopropyl alcohol. When cutting tape to size, we recommend cutting it slightly smaller than the area to be taped.
Apply the tape to the center of the heat sink bonding area and smooth over the entire surface with a hand or roller. More pressure produces better wetting out of the adhesive to the contact surfaces. A twisting motion during assembly of the two bonding surfaces will typically improve wetting. Note that typically 70% of the ultimate adhesive bond strength is achieved with initial application, and 80-90% is reached within 15 minutes. Ultimate adhesive strength is achieved within 36 hours; however, the next handling step can typically occur immediately following the initial application.
To remove, carefully insert a thin, short blade into the bond line at a corner between the components. Remove the blade and insert a spatula into the wedge. Slowly twist the spatula blade so that it exerts a slight upward pressure. As the two surfaces start to separate, move the spatula blade deeper into the bond line and continue the twisting motion and upward force. After the two components are separated, the tape can be removed and discarded.
If adhesive remains on the surfaces, it should be removed. Adhesive is best removed by wiping with a clean, lint-free cloth dampened with solvent. Use sufficient solvent to remove all adhesive. Parts must be free of solvent before applying more adhesive.
Item # | TCDT1 | TCDT2 |
---|---|---|
Construction | ||
Carrier | Expanded Al | |
Color | Grey | |
Thickness | 0.009" ± 0.001" (0.229 mm ± 0.03 mm) | |
Thermal | ||
Thermal Impedance @ <1 psi | 0.25 °C-in2/W (1.7 °C-cm2/W) | |
Thermal Conductivity | 1.40 W/m-K | |
Electrical | ||
Voltage Breakdown | N/A | |
Volume Resistivity | 0.013 ohm-cm | |
Flammability Rating (E140244) | Not Rated | |
Lap Shear Adhesion | 70 psi (0.483 MPa) |
Item # | TCDT1 | TCDT2 | |
---|---|---|---|
Mechanical | |||
Die Shear Adhesion |
|||
Aluminum | 135 psi (0.931 MPa) @ 25 °C 25 psi (0.172 MPa) @ 150 °C |
||
Copper | 115 psi (0.793 MPa) @ 25 °C 35 psi (0.241 MPa) @ 150 °C |
||
Aluminum Oxide | 125 psi (0.862 MPa) @ 25 °C 40 psi (0.276 MPa) @ 150 °C |
||
Creep Adhesion |
|||
25°C, 12 psi (0.083 MPa) | >50 days | ||
150°C, 12 psi (0.083 MPa) | >50 days | ||
Adhesive CTE, -40 to 150 °C | 400 ppm/°C | ||
Dimensions | 1" x 48" (25.4 mm x 1219 mm) |
2" x 24" (50.8 mm x 610 mm) |

Specifications | |
---|---|
Width | 3/4" (1.9 cm) |
Length | 36 yds (32.9 m) |
Kapton Type | HN |
Film Thickness | 1.0 Mil (0.03 mm) |
Total Thickness | 2.5 Mil (0.07 mm) |
Color | Amber |
Adhesive | Cross-Linked Silicon |
Breaking Strengtha | 30 lb/in (5.4 kg/cm) |
Elongation at Break | 60% |
Adhesion to Steel | 18 oz/in (200 g/cm) |
Dielectric Strength | 7,500 Volts |
Insulation Class | 356 °F (180 °C) |
Temperature Rangeb | -100 °F to 500 °F (-73 °C to 260 °C) |
Storage Conditions | Dry Location between 55 °F and 85 °F (13 °C and 30 °C) |
- Removes Easily without Leaving a Residue
- Wide Usage Range: -100 °F to 500 °F (-73°C to 260 °C)
- Substitute for Standard Electrical Tape in Cooled and Heated Environments
- Excellent for Insulation, Masking, or Packaging Applications
This high-temperature tape is made from DuPont's trademark Kapton®† film and a cross-linked silicon adhesive. The tape is flame-resistant, will withstand short-term intermittent temperatures to 600 °F, and can be used as electrical and thermal insulation. Compared to electrical tape, it removes easily without leaving a residue, making it ideal for packing, temporarily securing components, or powder coating applications.
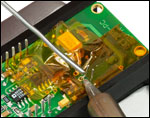
Click to Enlarge
Kapton Tape can be used to protect a circuit board during soldering.
Kapton tape is commonly used as a wire and cable wrap as well as to protect electrical components during soldering. It is effective for both hand-soldering and mass soldering applications, such as wave soldering. In the electronics industry, Kapton tape is applied to circuit boards before wave soldering to shield gold fingers from the solder material and prevent unwanted electrical connections. The tape is also easy to trim with a razor blade and can be used as a temporary dust cover for ports in devices.
†Kapton® is a registered trademark of DuPont Electronics, Inc.

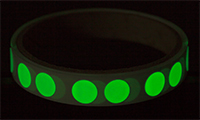
Click to Enlarge
PLT2 Shown with the Lights Off
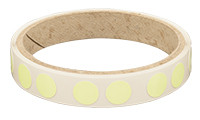
Click to Enlarge
PLT2 Shown with the Lights On
- Ideal for Dark Rooms
- Mark Equipment, Doorways, Walkways, or Table Edges
- 100 Ø1/2" (Ø12.7 mm) Sticker Dots per Roll
- Glow Time of up to 12 Hours
These vinyl photoluminescent stickers are ideal for marking doorways, table edges, and walkways, making movement within a dark room safer and easier. They can also be used to make it easier to locate equipment in a dark room. Each roll contains 100 Ø1/2" (Ø12.7 mm) photoluminescent sticker dots that have a glow time of up to 12 hours. Shown to the right is a comparison of how the photoluminescent dots appear with the lights on and off.
Each sticker charges in under three minutes. For information regarding the charge and glow times of these photoluminescent stickers, please click on the red docs icon below.