Single Mode Fiber
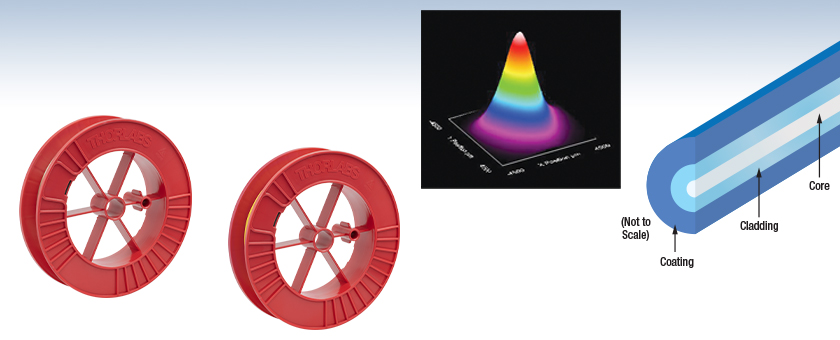
- Operating Wavelengths from 320 nm to 2200 nm
- Shipped from Stock with No Minimum Order
- Patch Cables Available for All Fibers
- Ø80 µm or Ø125 µm Cladding Available
Typical Output Beam Profile from a Single Mode Fiber
Some Fibers are Available with
a Ø900 µm Hytrel Jacket
Single Mode Fiber Cross Section
780HP
780 - 970 nm,
Ø245 µm Acrylate Coating
H1060-J9
980 - 1650 nm,
Ø900 µm Hytrel® Jacket

Please Wait

Stock Patch Cables Available with This Fiber | ||
---|---|---|
SM300 Fiber |
Custom cables are also available. Click here for details.
Features
- Single Mode Transmission from 320 to 430 nm
- Dual Acrylate Coating
- Pure Silica Core
- Shipped from Stock
- No Minimum Purchase Required
Thorlabs' SM300 fiber consists of an undoped, pure silica core surrounded by a depressed, fluorine-doped cladding. Since these fibers do not contain germania (GeO2), which causes electronic defects and color centers associated with the Ge-O bond, the primary cause of photodarkening is greatly reduced. As a result, power handling in the blue region is increased from several milliwats to several watts. The transmission-limiting effects caused by other nonlinearities (e.g., stimulated scattering) or even thermal damage are also increased over those of a conventional silica fiber doped with germanium. In the UV region, the SM300 will still exhibit some photodarkening, but will have superior performance compared to conventional fibers.
Item # | Operating Wavelength | Mode Field Diametera | Cladding | Coating | Cut-Off Wavelength |
---|---|---|---|---|---|
SM300 | 320 - 430 nm | 2.0 - 2.4 µm @ 350 nm | 125 ± 1 µm | 245 ± 15 µm | ≤310 nm |
Item # | Short-Term Bend Radius | Long-Term Bend Radius | Attenuation (Max) | Proof Test Level | NA | Core Indexb | Cladding Indexb |
---|---|---|---|---|---|---|---|
SM300 | ≥10 mm | ≥30 mm | ≤100 dB/km @ 350 nm ≤130 dB/km @ 430 nm |
1% (100 kpsi) | 0.12 - 0.14 | 320 nm: 1.48274 375 nm: 1.47314 430 nm: 1.46719 |
320 nm: 1.47703 375 nm: 1.46739 430 nm: 1.46142 |

Click to Enlarge
The left image shows the intensity profile of the beam propagated through the fiber overlaid on the fiber itself. The right image shows the standard intensity profile of the beam propagated through the fiber with the MFD and core diameter called out.
Definition of the Mode Field Diameter
The mode field diameter (MFD) is one measure of the beam width of light propagating in a single mode fiber. It is a function of wavelength, core radius, and the refractive indices of the core and cladding. While much of the light in an optical fiber is trapped within the fiber core, a small fraction propagates in the cladding. The light can be approximated as a Gaussian power distribution as shown to the right, where the MFD is the diameter at which the optical power is reduced to 1/e2 from its peak level.
Measurement of MFD
The measurement of MFD is accomplished by the Variable Aperture Method in the Far Field (VAMFF). An aperture is placed in the far field of the fiber output, and the intensity is measured. As successively smaller apertures are placed in the beam, the intensity levels are measured for each aperture; the data can then be plotted as power vs. the sine of the aperture half-angle (or the numerical aperture for an SM fiber).
The MFD is then determined using Petermann's second definition, which is a mathematical model that does not assume a specific shape of power distribution. The MFD in the near field can be determined from this far-field measurement using the Hankel Transform.
Quick Links |
---|
Damage at the Air / Glass Interface |
Intrinsic Damage Threshold |
Preparation and Handling of Optical Fibers |
Laser-Induced Damage in Silica Optical Fibers
The following tutorial details damage mechanisms relevant to unterminated (bare) fiber, terminated optical fiber, and other fiber components from laser light sources. These mechanisms include damage that occurs at the air / glass interface (when free-space coupling or when using connectors) and in the optical fiber itself. A fiber component, such as a bare fiber, patch cable, or fused coupler, may have multiple potential avenues for damage (e.g., connectors, fiber end faces, and the device itself). The maximum power that a fiber can handle will always be limited by the lowest limit of any of these damage mechanisms.
While the damage threshold can be estimated using scaling relations and general rules, absolute damage thresholds in optical fibers are very application dependent and user specific. Users can use this guide to estimate a safe power level that minimizes the risk of damage. Following all appropriate preparation and handling guidelines, users should be able to operate a fiber component up to the specified maximum power level; if no maximum is specified for a component, users should abide by the "practical safe level" described below for safe operation of the component. Factors that can reduce power handling and cause damage to a fiber component include, but are not limited to, misalignment during fiber coupling, contamination of the fiber end face, or imperfections in the fiber itself. For further discussion about an optical fiber’s power handling abilities for a specific application, please contact Thorlabs’ Tech Support.

Click to Enlarge
Undamaged Fiber End

Click to Enlarge
Damaged Fiber End
Damage at the Air / Glass Interface
There are several potential damage mechanisms that can occur at the air / glass interface. Light is incident on this interface when free-space coupling or when two fibers are mated using optical connectors. High-intensity light can damage the end face leading to reduced power handling and permanent damage to the fiber. For fibers terminated with optical connectors where the connectors are fixed to the fiber ends using epoxy, the heat generated by high-intensity light can burn the epoxy and leave residues on the fiber facet directly in the beam path.
Estimated Optical Power Densities on Air / Glass Interfacea | ||
---|---|---|
Type | Theoretical Damage Thresholdb | Practical Safe Levelc |
CW (Average Power) |
~1 MW/cm2 | ~250 kW/cm2 |
10 ns Pulsed (Peak Power) |
~5 GW/cm2 | ~1 GW/cm2 |
Damage Mechanisms on the Bare Fiber End Face
Damage mechanisms on a fiber end face can be modeled similarly to bulk optics, and industry-standard damage thresholds for UV Fused Silica substrates can be applied to silica-based fiber. However, unlike bulk optics, the relevant surface areas and beam diameters involved at the air / glass interface of an optical fiber are very small, particularly for coupling into single mode (SM) fiber. therefore, for a given power density, the power incident on the fiber needs to be lower for a smaller beam diameter.
The table to the right lists two thresholds for optical power densities: a theoretical damage threshold and a "practical safe level". In general, the theoretical damage threshold represents the estimated maximum power density that can be incident on the fiber end face without risking damage with very good fiber end face and coupling conditions. The "practical safe level" power density represents minimal risk of fiber damage. Operating a fiber or component beyond the practical safe level is possible, but users must follow the appropriate handling instructions and verify performance at low powers prior to use.
Calculating the Effective Area for Single Mode Fibers
The effective area for single mode (SM) fiber is defined by the mode field diameter (MFD), which is the cross-sectional area through which light propagates in the fiber; this area includes the fiber core and also a portion of the cladding. To achieve good efficiency when coupling into a single mode fiber, the diameter of the input beam must match the MFD of the fiber.
As an example, SM400 single mode fiber has a mode field diameter (MFD) of ~Ø3 µm operating at 400 nm, while the MFD for SMF-28 Ultra single mode fiber operating at 1550 nm is Ø10.5 µm. The effective area for these fibers can be calculated as follows:
SM400 Fiber: Area = Pi x (MFD/2)2 = Pi x (1.5 µm)2 = 7.07 µm2 = 7.07 x 10-8 cm2
SMF-28 Ultra Fiber: Area = Pi x (MFD/2)2 = Pi x (5.25 µm)2 = 86.6 µm2 = 8.66 x 10-7 cm2
To estimate the power level that a fiber facet can handle, the power density is multiplied by the effective area. Please note that this calculation assumes a uniform intensity profile, but most laser beams exhibit a Gaussian-like shape within single mode fiber, resulting in a higher power density at the center of the beam compared to the edges. Therefore, these calculations will slightly overestimate the power corresponding to the damage threshold or the practical safe level. Using the estimated power densities assuming a CW light source, we can determine the corresponding power levels as:
SM400 Fiber: 7.07 x 10-8 cm2 x 1 MW/cm2 = 7.1 x 10-8 MW = 71 mW (Theoretical Damage Threshold)
7.07 x 10-8 cm2 x 250 kW/cm2 = 1.8 x 10-5 kW = 18 mW (Practical Safe Level)
SMF-28 Ultra Fiber: 8.66 x 10-7 cm2 x 1 MW/cm2 = 8.7 x 10-7 MW = 870 mW (Theoretical Damage Threshold)
8.66 x 10-7 cm2 x 250 kW/cm2 = 2.1 x 10-4 kW = 210 mW (Practical Safe Level)
Effective Area of Multimode Fibers
The effective area of a multimode (MM) fiber is defined by the core diameter, which is typically far larger than the MFD of an SM fiber. For optimal coupling, Thorlabs recommends focusing a beam to a spot roughly 70 - 80% of the core diameter. The larger effective area of MM fibers lowers the power density on the fiber end face, allowing higher optical powers (typically on the order of kilowatts) to be coupled into multimode fiber without damage.
Damage Mechanisms Related to Ferrule / Connector Termination

Plot showing approximate input power that can be incident on a single mode silica optical fiber with a termination. Each line shows the estimated power level due to a specific damage mechanism. The maximum power handling is limited by the lowest power level from all relevant damage mechanisms (indicated by a solid line).
Fibers terminated with optical connectors have additional power handling considerations. Fiber is typically terminated using epoxy to bond the fiber to a ceramic or steel ferrule. When light is coupled into the fiber through a connector, light that does not enter the core and propagate down the fiber is scattered into the outer layers of the fiber, into the ferrule, and the epoxy used to hold the fiber in the ferrule. If the light is intense enough, it can burn the epoxy, causing it to vaporize and deposit a residue on the face of the connector. This results in localized absorption sites on the fiber end face that reduce coupling efficiency and increase scattering, causing further damage.
For several reasons, epoxy-related damage is dependent on the wavelength. In general, light scatters more strongly at short wavelengths than at longer wavelengths. Misalignment when coupling is also more likely due to the small MFD of short-wavelength SM fiber that also produces more scattered light.
To minimize the risk of burning the epoxy, fiber connectors can be constructed to have an epoxy-free air gap between the optical fiber and ferrule near the fiber end face. Our high-power multimode fiber patch cables use connectors with this design feature.
Determining Power Handling with Multiple Damage Mechanisms
When fiber cables or components have multiple avenues for damage (e.g., fiber patch cables), the maximum power handling is always limited by the lowest damage threshold that is relevant to the fiber component. In general, this represents the highest input power that can be incident on the patch cable end face and not the coupled output power.
As an illustrative example, the graph to the right shows an estimate of the power handling limitations of a single mode fiber patch cable due to damage to the fiber end face and damage via an optical connector. The total input power handling of a terminated fiber at a given wavelength is limited by the lower of the two limitations at any given wavelength (indicated by the solid lines). A single mode fiber operating at around 488 nm is primarily limited by damage to the fiber end face (blue solid line), but fibers operating at 1550 nm are limited by damage to the optical connector (red solid line).
In the case of a multimode fiber, the effective mode area is defined by the core diameter, which is larger than the effective mode area for SM fiber. This results in a lower power density on the fiber end face and allows higher optical powers (on the order of kilowatts) to be coupled into the fiber without damage (not shown in graph). However, the damage limit of the ferrule / connector termination remains unchanged and as a result, the maximum power handling for a multimode fiber is limited by the ferrule and connector termination.
Please note that these are rough estimates of power levels where damage is very unlikely with proper handling and alignment procedures. It is worth noting that optical fibers are frequently used at power levels above those described here. However, these applications typically require expert users and testing at lower powers first to minimize risk of damage. Even still, optical fiber components should be considered a consumable lab supply if used at high power levels.
Intrinsic Damage Threshold
In addition to damage mechanisms at the air / glass interface, optical fibers also display power handling limitations due to damage mechanisms within the optical fiber itself. These limitations will affect all fiber components as they are intrinsic to the fiber itself. Two categories of damage within the fiber are damage from bend losses and damage from photodarkening.
Bend Losses
Bend losses occur when a fiber is bent to a point where light traveling in the core is incident on the core/cladding interface at an angle higher than the critical angle, making total internal reflection impossible. Under these circumstances, light escapes the fiber, often in a localized area. The light escaping the fiber typically has a high power density, which burns the fiber coating as well as any surrounding furcation tubing.
A special category of optical fiber, called double-clad fiber, can reduce the risk of bend-loss damage by allowing the fiber’s cladding (2nd layer) to also function as a waveguide in addition to the core. By making the critical angle of the cladding/coating interface higher than the critical angle of the core/clad interface, light that escapes the core is loosely confined within the cladding. It will then leak out over a distance of centimeters or meters instead of at one localized spot within the fiber, minimizing the risk of damage. Thorlabs manufactures and sells 0.22 NA double-clad multimode fiber, which boasts very high, megawatt range power handling.
Photodarkening
A second damage mechanism, called photodarkening or solarization, can occur in fibers used with ultraviolet or short-wavelength visible light, particularly those with germanium-doped cores. Fibers used at these wavelengths will experience increased attenuation over time. The mechanism that causes photodarkening is largely unknown, but several fiber designs have been developed to mitigate it. For example, fibers with a very low hydroxyl ion (OH) content have been found to resist photodarkening and using other dopants, such as fluorine, can also reduce photodarkening.
Even with the above strategies in place, all fibers eventually experience photodarkening when used with UV or short-wavelength light, and thus, fibers used at these wavelengths should be considered consumables.
Preparation and Handling of Optical Fibers
General Cleaning and Operation Guidelines
These general cleaning and operation guidelines are recommended for all fiber optic products. Users should still follow specific guidelines for an individual product as outlined in the support documentation or manual. Damage threshold calculations only apply when all appropriate cleaning and handling procedures are followed.
-
All light sources should be turned off prior to installing or integrating optical fibers (terminated or bare). This ensures that focused beams of light are not incident on fragile parts of the connector or fiber, which can possibly cause damage.
-
The power-handling capability of an optical fiber is directly linked to the quality of the fiber/connector end face. Always inspect the fiber end prior to connecting the fiber to an optical system. The fiber end face should be clean and clear of dirt and other contaminants that can cause scattering of coupled light. Bare fiber should be cleaved prior to use and users should inspect the fiber end to ensure a good quality cleave is achieved.
-
If an optical fiber is to be spliced into the optical system, users should first verify that the splice is of good quality at a low optical power prior to high-power use. Poor splice quality may increase light scattering at the splice interface, which can be a source of fiber damage.
-
Users should use low power when aligning the system and optimizing coupling; this minimizes exposure of other parts of the fiber (other than the core) to light. Damage from scattered light can occur if a high power beam is focused on the cladding, coating, or connector.
Tips for Using Fiber at Higher Optical Power
Optical fibers and fiber components should generally be operated within safe power level limits, but under ideal conditions (very good optical alignment and very clean optical end faces), the power handling of a fiber component may be increased. Users must verify the performance and stability of a fiber component within their system prior to increasing input or output power and follow all necessary safety and operation instructions. The tips below are useful suggestions when considering increasing optical power in an optical fiber or component.
-
Splicing a fiber component into a system using a fiber splicer can increase power handling as it minimizes possibility of air/fiber interface damage. Users should follow all appropriate guidelines to prepare and make a high-quality fiber splice. Poor splices can lead to scattering or regions of highly localized heat at the splice interface that can damage the fiber.
-
After connecting the fiber or component, the system should be tested and aligned using a light source at low power. The system power can be ramped up slowly to the desired output power while periodically verifying all components are properly aligned and that coupling efficiency is not changing with respect to optical launch power.
-
Bend losses that result from sharply bending a fiber can cause light to leak from the fiber in the stressed area. When operating at high power, the localized heating that can occur when a large amount of light escapes a small localized area (the stressed region) can damage the fiber. Avoid disturbing or accidently bending fibers during operation to minimize bend losses.
-
Users should always choose the appropriate optical fiber for a given application. For example, large-mode-area fibers are a good alternative to standard single mode fibers in high-power applications as they provide good beam quality with a larger MFD, decreasing the power density on the air/fiber interface.
-
Step-index silica single mode fibers are normally not used for ultraviolet light or high-peak-power pulsed applications due to the high spatial power densities associated with these applications.
Posted Comments: | |
ILIYA SHOFMAN
 (posted 2024-10-09 14:51:12.75) Hello,
I'd like to inquire about the definition of NA in S405-XP. Is it at 1% or 13.5%(1/e^2) power? I believe this question has been asked before, and therefore it would be beneficial if the response is shared in the below forum.
Thank you! EGies
 (posted 2024-10-14 03:42:40.0) Thank you for contacting Thorlabs. The NA for S405-XP is defined using the classical physics definition, where NA = square root [(Refractive index of the core)^2 - (Refractive index of the cladding)^2]. I have reached out to you directly regarding this. Bogdanrvk BogdanemrWN
 (posted 2024-04-24 03:43:42.48) Manon Lallement
 (posted 2023-12-11 10:50:22.687) Hello,
Could you tell me what is the birefringence of your SM630 HP fiber please ?
Thank you in advance,
Best regards,
Manon Lallement cdolbashian
 (posted 2023-12-15 03:03:42.0) Thank you for reaching out to us with this inquiry. The SM630-HP fiber is a pure silica fiber with no stress rods within it. Nominally it is an isotropic material. That being said, by stressing the glass, perhaps with a paddle-style polarization controller, you can induce birefringence in the silica, and thus control phase and polarization directly. Ao Teng
 (posted 2023-04-13 13:09:23.8) Hello, I would like to consult the Mode Field Daimeter and NA of SM300. In my opinion, MFD should be equal to 1.22*wavelength / NA, that is 1.22*0.35 um / 0.12=3.56 um. But this value is far from the given MFD(2.0-2.4 um), so I would like to know the relationship between MFD and NA you listed. More, when using SM300 for fiber coupling at 393 nm, how should I perform some ZEMAX simulations based on MFD or NA to improve the coupling efficiency.
Thank you! cdolbashian
 (posted 2023-04-13 11:35:53.0) Thank you for reaching out to us with this inquiry. Above in the "MFD calculations" tab, we outline the method which we use to take these measurements. Regarding the simulation of these fibers within Optics Studio, I would recommend contacting Ansys or checking their knowledge base for some tips/tricks. Shreyas P
 (posted 2023-02-08 20:26:22.68) Hi, What is the exact core diameter for the SM800 and 780HP fibers? (sorry for using the wrong form; the feedback form for these fibers was not working)
Thanks! cdolbashian
 (posted 2023-02-17 11:31:00.0) Thank you for reaching out to us with this inquiry! I have contacted you directly to share the information we can provide. Ao Teng
 (posted 2023-01-16 22:22:55.167) Hello, I'd like to inquire about the definition of NA in SM300, SM400 and S405-XP.
Is it at 1% or 13.5%(1/e^2) power?
Thank you! jgreschler
 (posted 2023-01-17 09:09:25.0) Thank you for reaching out to Thorlabs. Additional specifications and definitions can be requested by contacting techsupport@thorlabs.com. I have reached out to you directly with details. B Little
 (posted 2022-07-27 10:13:42.157) Do you have any data on photodarkening of this fiber at 320 nm? We have experienced some and are worried that it might be prohibitive for our end goal of transmitting tens of mW of power.
(this is similar to but different from the previous question on damage threshold) jgreschler
 (posted 2022-08-04 02:48:23.0) Thank you for reaching out to Thorlabs. We do have some data regarding photodarkening of silica fibers over the UV range. I have reached out to you directly to provide this data and discuss damage thresholds. Stephen Webster
 (posted 2022-05-24 14:33:10.163) Please could you tell me the core diameter of the SM300 fibre? I need this to carry out a simulation of the beam propagation using Zemax. Thanks. jgreschler
 (posted 2022-05-24 04:10:56.0) Thank you for reaching out to Thorlabs. The calculated core diameter of this fiber is ~1.8um. Brooks Childers
 (posted 2021-06-01 13:08:23.503) The information in the "MFD Definition" tab on the page for single mode fiber products seems to indicate that Thorlabs, or someone else, has measured the actual mode field diameter of those fibers according to the VAMFF method. Is that true? cdolbashian
 (posted 2021-06-14 04:49:36.0) Thank you for reaching out to us at Thorlabs. As some of our fibers are vendor items, and we are not privy to their testing methods, we cannot guarantee the MFD characterization method of everything in a general sense. I have reached out to you directly to discuss this further. yeongdae
 (posted 2017-08-26 17:43:36.093) Hi. I was looking at 'Specs' and 'MFD Definition' tab of [Single Mode Fiber: 320 to 430 nm] page.
There, it says your 320 - 430 nm fiber's Mode Field Diameter is 2.0~2.4 microns. My measurement on this fiber actually gives twice that value.
My hypothesis is that MFD definition is sometimes confusing, as this value is also 2*omega_0 where omega_0 is "beam waist" following the definition of Wikipedia's [Gaussian beam] page. Maybe what you wrote as Mode Field Diameter is actaully omega_0 value??
Can you check this and give me a feedback, as I also want to make sure that my measurements were in fact correct?? tfrisch
 (posted 2017-09-14 03:53:23.0) Hello, thank you for contacting Thorlabs. I will reach out to you directly to compare our calculations. I'd be interested to see if you use a model that deviates from the Variable Aperture Method in the Far Field. vivien.loo
 (posted 2017-07-06 13:28:56.17) Hi,
SM300 has a pure undoped silica core, is it the same for SM600 and 630HP? nbayconich
 (posted 2017-08-08 09:56:51.0) Thank you for contacting Thorlabs. The SM600 and 630HP fibers have GeO2 doped cores. I will contact you directly with more information. goodwi63
 (posted 2017-01-26 16:07:49.89) I would like to know the core diameter for the SM300, and if it is not the smallest core diameter, which of your products has the smallest core diameter. pbui
 (posted 2017-01-30 04:23:11.0) Thank you for your inquiry. We will contact you directly to discuss your application requirements and recommend the appropriate fiber. soshenko.v
 (posted 2016-02-02 11:03:16.203) Hello, can you give some data for non-bridging oxygen centers in this fiber and its intrinsic fluorescence? Comparing to SM600, is fluorescence higher or lower?
Is this fiber somehow related (Thorlabs buys it from them or vice versa) to Nufern 630HP fiber? besembeson
 (posted 2016-02-04 03:19:11.0) Response from Bweh at Thorlabs USA: Thanks for contacting Thorlabs. We don't have such data at the moment for the SM300, and we don't have a fluorescence comparison with the SM600 either. Our 630HP has the same specifications as the Nufern 630HP. mchen
 (posted 2014-07-09 10:56:22.61) Hi, Can you please tell me what is the dispersion of SM2000 fiber? thanks, Mike jlow
 (posted 2014-08-07 10:17:45.0) Response from Jeremy at Thorlabs: The dispersion is estimated to be around 47ps/(nm*km) at 2000nm. lokirune
 (posted 2014-05-21 14:45:27.98) HI. I was using the SM450 and 460HP, and it seems to burn easily. Is there any data sheet for damage threshold for those fiber? Also, I used it before and find that it much easier to burn with pulse laser. It there any specific reason for that? pbui
 (posted 2014-06-02 09:46:36.0) There are no data sheets for damage threshold available, but it's possible to apply industry-standard damage thresholds for UV Fused Silica substrates to silica-based fibers. The surface areas and beam diameters involved at the air to glass interface are extremely small compared to bulk optics, especially with single mode (SM) fiber, and this results in very small damage thresholds. Assuming you're launching into bare fiber (no connectors), 250 kW/cm^2 is a practical value for Maximum Power Density for CW lasers, while for a 10 ns Pulsed (peak power) laser, the max may be around 1 GW/cm^2. We will contact you directly to find out more about your setup and to provide further details. helmofon
 (posted 2013-12-15 14:18:47.37) Dear Sir/Madam
I will be very grateful for the information about refractive index of core and clad of SMF - 28 @1550nm.
Thank You, Maciej jlow
 (posted 2013-12-17 08:50:38.0) Response from Jeremy at Thorlabs: The refractive index for the core and clad is around 1.4682 and 1.4615 respectively for SMF-28e+ at 1550nm. akselrod
 (posted 2013-03-12 18:02:09.78) I would like to know the dispersion of this fiber at around 400 nm. Can you pleas let me know this value? Thanks! Gleb jlow
 (posted 2013-04-11 15:40:00.0) Response from Jeremy at Thorlabs: Based on the generally used formula for waveguide dispersion and chromatic dispersion, the estimated dispersion for SM300 is on the order of -23 ps/(km-nm) at 400nm. That value can change depending on the actual numerical aperture and the cut-off wavelength of each spool of fiber. bdada
 (posted 2012-06-05 19:30:00.0) Response from Buki at Thorlabs to Alfred:
Thank you for participating in our feedback forum. Below is the refractive index of 780HP at 780nm:
Core = 1.4598
Clad = 1.4537
Please contact TechSupport@thorlabs.com if you have any questions. user
 (posted 2012-06-05 04:25:46.0) Dear Sir or Madame,
I want to know the refractive index of 780HP, then I will determine how long the fiber I will order.
Thank you in advance.
Alfred tcohen
 (posted 2012-03-01 14:33:00.0) Response from Tim at Thorlabs: Thank you for your feedback. The S405-HP has a core index of 1.46958 and clad index of 1.46428 measured at 405nm. The MFD @ 460nm is 3.2 +/- .5 um. Please use these as references but note that they are approximate and may vary from lot to lot. marko.vranicar
 (posted 2012-02-29 19:04:22.0) Dear Sir Or Madame,
Recently, we purchased the S405-HP fiber. We need to know the cladding and core refractive indices as well as the core radius at 473nm that I cannot find in specs.
I thank you in advance for your answer and assistance.
Best regards,
Marko |

Stock Patch Cables Available with These Fibers | ||
---|---|---|
SM400 Fiber |
SM450 Fiber |
Custom cables are also available. Click here for details.
Features
- SM Fiber at 400 nm to 680 nm
- Shipped from Stock
- Acrylate Jacket
- S405-XP: Pure Silica Core
- SM400: Pure Silica Core and Fluorine Doped Cladding
- No Minimum Purchase Required
Item # | Operating Wavelength | Mode Field Diameter | Cladding | Coating | Cut-Off Wavelength |
---|---|---|---|---|---|
S405-XP | 400 - 680 nm | 3.3 ± 0.5 µm @ 405 nm 4.6 ± 0.5 µm @ 630 nm |
125.0 ± 1.0 µm | 245.0 ± 15.0 µm | 380 ± 20 nm |
SM400 | 405 - 532 nm | 2.5 - 3.4 µm @ 480 nm | 125 ± 1 µm | 245 ± 15 µm | 305 - 400 nm |
SM450a | 488 - 633 nm | 2.8 - 4.1 µmb @ 488 nm | 125 ± 1.0 µm | 245 ± 15 µm | 350 - 470 nm |
460HP | 450 - 600 nm | 3.5 ± 0.5 µm @ 515 nm | 125 ± 1 µm | 245 ± 15 µm | 430 ± 20 nm |
Item # | Short-Term Bend Radius | Long-Term Bend Radius | Attenuation (Max) | NA | Core Index | Cladding Index |
---|---|---|---|---|---|---|
S405-XP | ≥6 mm | ≥13 mm | ≤30.0 dB/km @ 630 nm ≤30.0 dB/km @ 488 nm |
0.12 | Calld | Calld |
SM400 | ≥10 mm | ≥30 mm | ≤50 dB/km @ 430 nm ≤30 dB/km @ 532 nm |
0.12 - 0.14 | 405 nm: 1.46958e 467 nm: 1.46435e 532 nm: 1.46071e |
405 nm: 1.46382e 467 nm: 1.45857e 532 nm: 1.45491e |
SM450 | ≥5 mm | ≥25 mm | ≤50 dB/km @ 488 nmc | 0.10 - 0.14 | 488 nm: 1.46645f 514 nm: 1.46501f |
488 nm: 1.46302f 514 nm: 1.46159f |
460HP | ≥6 mm | ≥13 mm | ≤30 dB/km @ 515 nm | 0.13 | Calld | Calld |

Click to Enlarge
The left image shows the intensity profile of the beam propagated through the fiber overlaid on the fiber itself. The right image shows the standard intensity profile of the beam propagated through the fiber with the MFD and core diameter called out.
Definition of the Mode Field Diameter
The mode field diameter (MFD) is one measure of the beam width of light propagating in a single mode fiber. It is a function of wavelength, core radius, and the refractive indices of the core and cladding. While much of the light in an optical fiber is trapped within the fiber core, a small fraction propagates in the cladding. The light can be approximated as a Gaussian power distribution as shown to the right, where the MFD is the diameter at which the optical power is reduced to 1/e2 from its peak level.
Measurement of MFD
The measurement of MFD is accomplished by the Variable Aperture Method in the Far Field (VAMFF). An aperture is placed in the far field of the fiber output, and the intensity is measured. As successively smaller apertures are placed in the beam, the intensity levels are measured for each aperture; the data can then be plotted as power vs. the sine of the aperture half-angle (or the numerical aperture for an SM fiber).
The MFD is then determined using Petermann's second definition, which is a mathematical model that does not assume a specific shape of power distribution. The MFD in the near field can be determined from this far-field measurement using the Hankel Transform.
Quick Links |
---|
Damage at the Air / Glass Interface |
Intrinsic Damage Threshold |
Preparation and Handling of Optical Fibers |
Laser-Induced Damage in Silica Optical Fibers
The following tutorial details damage mechanisms relevant to unterminated (bare) fiber, terminated optical fiber, and other fiber components from laser light sources. These mechanisms include damage that occurs at the air / glass interface (when free-space coupling or when using connectors) and in the optical fiber itself. A fiber component, such as a bare fiber, patch cable, or fused coupler, may have multiple potential avenues for damage (e.g., connectors, fiber end faces, and the device itself). The maximum power that a fiber can handle will always be limited by the lowest limit of any of these damage mechanisms.
While the damage threshold can be estimated using scaling relations and general rules, absolute damage thresholds in optical fibers are very application dependent and user specific. Users can use this guide to estimate a safe power level that minimizes the risk of damage. Following all appropriate preparation and handling guidelines, users should be able to operate a fiber component up to the specified maximum power level; if no maximum is specified for a component, users should abide by the "practical safe level" described below for safe operation of the component. Factors that can reduce power handling and cause damage to a fiber component include, but are not limited to, misalignment during fiber coupling, contamination of the fiber end face, or imperfections in the fiber itself. For further discussion about an optical fiber’s power handling abilities for a specific application, please contact Thorlabs’ Tech Support.

Click to Enlarge
Undamaged Fiber End

Click to Enlarge
Damaged Fiber End
Damage at the Air / Glass Interface
There are several potential damage mechanisms that can occur at the air / glass interface. Light is incident on this interface when free-space coupling or when two fibers are mated using optical connectors. High-intensity light can damage the end face leading to reduced power handling and permanent damage to the fiber. For fibers terminated with optical connectors where the connectors are fixed to the fiber ends using epoxy, the heat generated by high-intensity light can burn the epoxy and leave residues on the fiber facet directly in the beam path.
Estimated Optical Power Densities on Air / Glass Interfacea | ||
---|---|---|
Type | Theoretical Damage Thresholdb | Practical Safe Levelc |
CW (Average Power) |
~1 MW/cm2 | ~250 kW/cm2 |
10 ns Pulsed (Peak Power) |
~5 GW/cm2 | ~1 GW/cm2 |
Damage Mechanisms on the Bare Fiber End Face
Damage mechanisms on a fiber end face can be modeled similarly to bulk optics, and industry-standard damage thresholds for UV Fused Silica substrates can be applied to silica-based fiber. However, unlike bulk optics, the relevant surface areas and beam diameters involved at the air / glass interface of an optical fiber are very small, particularly for coupling into single mode (SM) fiber. therefore, for a given power density, the power incident on the fiber needs to be lower for a smaller beam diameter.
The table to the right lists two thresholds for optical power densities: a theoretical damage threshold and a "practical safe level". In general, the theoretical damage threshold represents the estimated maximum power density that can be incident on the fiber end face without risking damage with very good fiber end face and coupling conditions. The "practical safe level" power density represents minimal risk of fiber damage. Operating a fiber or component beyond the practical safe level is possible, but users must follow the appropriate handling instructions and verify performance at low powers prior to use.
Calculating the Effective Area for Single Mode Fibers
The effective area for single mode (SM) fiber is defined by the mode field diameter (MFD), which is the cross-sectional area through which light propagates in the fiber; this area includes the fiber core and also a portion of the cladding. To achieve good efficiency when coupling into a single mode fiber, the diameter of the input beam must match the MFD of the fiber.
As an example, SM400 single mode fiber has a mode field diameter (MFD) of ~Ø3 µm operating at 400 nm, while the MFD for SMF-28 Ultra single mode fiber operating at 1550 nm is Ø10.5 µm. The effective area for these fibers can be calculated as follows:
SM400 Fiber: Area = Pi x (MFD/2)2 = Pi x (1.5 µm)2 = 7.07 µm2 = 7.07 x 10-8 cm2
SMF-28 Ultra Fiber: Area = Pi x (MFD/2)2 = Pi x (5.25 µm)2 = 86.6 µm2 = 8.66 x 10-7 cm2
To estimate the power level that a fiber facet can handle, the power density is multiplied by the effective area. Please note that this calculation assumes a uniform intensity profile, but most laser beams exhibit a Gaussian-like shape within single mode fiber, resulting in a higher power density at the center of the beam compared to the edges. Therefore, these calculations will slightly overestimate the power corresponding to the damage threshold or the practical safe level. Using the estimated power densities assuming a CW light source, we can determine the corresponding power levels as:
SM400 Fiber: 7.07 x 10-8 cm2 x 1 MW/cm2 = 7.1 x 10-8 MW = 71 mW (Theoretical Damage Threshold)
7.07 x 10-8 cm2 x 250 kW/cm2 = 1.8 x 10-5 kW = 18 mW (Practical Safe Level)
SMF-28 Ultra Fiber: 8.66 x 10-7 cm2 x 1 MW/cm2 = 8.7 x 10-7 MW = 870 mW (Theoretical Damage Threshold)
8.66 x 10-7 cm2 x 250 kW/cm2 = 2.1 x 10-4 kW = 210 mW (Practical Safe Level)
Effective Area of Multimode Fibers
The effective area of a multimode (MM) fiber is defined by the core diameter, which is typically far larger than the MFD of an SM fiber. For optimal coupling, Thorlabs recommends focusing a beam to a spot roughly 70 - 80% of the core diameter. The larger effective area of MM fibers lowers the power density on the fiber end face, allowing higher optical powers (typically on the order of kilowatts) to be coupled into multimode fiber without damage.
Damage Mechanisms Related to Ferrule / Connector Termination

Plot showing approximate input power that can be incident on a single mode silica optical fiber with a termination. Each line shows the estimated power level due to a specific damage mechanism. The maximum power handling is limited by the lowest power level from all relevant damage mechanisms (indicated by a solid line).
Fibers terminated with optical connectors have additional power handling considerations. Fiber is typically terminated using epoxy to bond the fiber to a ceramic or steel ferrule. When light is coupled into the fiber through a connector, light that does not enter the core and propagate down the fiber is scattered into the outer layers of the fiber, into the ferrule, and the epoxy used to hold the fiber in the ferrule. If the light is intense enough, it can burn the epoxy, causing it to vaporize and deposit a residue on the face of the connector. This results in localized absorption sites on the fiber end face that reduce coupling efficiency and increase scattering, causing further damage.
For several reasons, epoxy-related damage is dependent on the wavelength. In general, light scatters more strongly at short wavelengths than at longer wavelengths. Misalignment when coupling is also more likely due to the small MFD of short-wavelength SM fiber that also produces more scattered light.
To minimize the risk of burning the epoxy, fiber connectors can be constructed to have an epoxy-free air gap between the optical fiber and ferrule near the fiber end face. Our high-power multimode fiber patch cables use connectors with this design feature.
Determining Power Handling with Multiple Damage Mechanisms
When fiber cables or components have multiple avenues for damage (e.g., fiber patch cables), the maximum power handling is always limited by the lowest damage threshold that is relevant to the fiber component. In general, this represents the highest input power that can be incident on the patch cable end face and not the coupled output power.
As an illustrative example, the graph to the right shows an estimate of the power handling limitations of a single mode fiber patch cable due to damage to the fiber end face and damage via an optical connector. The total input power handling of a terminated fiber at a given wavelength is limited by the lower of the two limitations at any given wavelength (indicated by the solid lines). A single mode fiber operating at around 488 nm is primarily limited by damage to the fiber end face (blue solid line), but fibers operating at 1550 nm are limited by damage to the optical connector (red solid line).
In the case of a multimode fiber, the effective mode area is defined by the core diameter, which is larger than the effective mode area for SM fiber. This results in a lower power density on the fiber end face and allows higher optical powers (on the order of kilowatts) to be coupled into the fiber without damage (not shown in graph). However, the damage limit of the ferrule / connector termination remains unchanged and as a result, the maximum power handling for a multimode fiber is limited by the ferrule and connector termination.
Please note that these are rough estimates of power levels where damage is very unlikely with proper handling and alignment procedures. It is worth noting that optical fibers are frequently used at power levels above those described here. However, these applications typically require expert users and testing at lower powers first to minimize risk of damage. Even still, optical fiber components should be considered a consumable lab supply if used at high power levels.
Intrinsic Damage Threshold
In addition to damage mechanisms at the air / glass interface, optical fibers also display power handling limitations due to damage mechanisms within the optical fiber itself. These limitations will affect all fiber components as they are intrinsic to the fiber itself. Two categories of damage within the fiber are damage from bend losses and damage from photodarkening.
Bend Losses
Bend losses occur when a fiber is bent to a point where light traveling in the core is incident on the core/cladding interface at an angle higher than the critical angle, making total internal reflection impossible. Under these circumstances, light escapes the fiber, often in a localized area. The light escaping the fiber typically has a high power density, which burns the fiber coating as well as any surrounding furcation tubing.
A special category of optical fiber, called double-clad fiber, can reduce the risk of bend-loss damage by allowing the fiber’s cladding (2nd layer) to also function as a waveguide in addition to the core. By making the critical angle of the cladding/coating interface higher than the critical angle of the core/clad interface, light that escapes the core is loosely confined within the cladding. It will then leak out over a distance of centimeters or meters instead of at one localized spot within the fiber, minimizing the risk of damage. Thorlabs manufactures and sells 0.22 NA double-clad multimode fiber, which boasts very high, megawatt range power handling.
Photodarkening
A second damage mechanism, called photodarkening or solarization, can occur in fibers used with ultraviolet or short-wavelength visible light, particularly those with germanium-doped cores. Fibers used at these wavelengths will experience increased attenuation over time. The mechanism that causes photodarkening is largely unknown, but several fiber designs have been developed to mitigate it. For example, fibers with a very low hydroxyl ion (OH) content have been found to resist photodarkening and using other dopants, such as fluorine, can also reduce photodarkening.
Even with the above strategies in place, all fibers eventually experience photodarkening when used with UV or short-wavelength light, and thus, fibers used at these wavelengths should be considered consumables.
Preparation and Handling of Optical Fibers
General Cleaning and Operation Guidelines
These general cleaning and operation guidelines are recommended for all fiber optic products. Users should still follow specific guidelines for an individual product as outlined in the support documentation or manual. Damage threshold calculations only apply when all appropriate cleaning and handling procedures are followed.
-
All light sources should be turned off prior to installing or integrating optical fibers (terminated or bare). This ensures that focused beams of light are not incident on fragile parts of the connector or fiber, which can possibly cause damage.
-
The power-handling capability of an optical fiber is directly linked to the quality of the fiber/connector end face. Always inspect the fiber end prior to connecting the fiber to an optical system. The fiber end face should be clean and clear of dirt and other contaminants that can cause scattering of coupled light. Bare fiber should be cleaved prior to use and users should inspect the fiber end to ensure a good quality cleave is achieved.
-
If an optical fiber is to be spliced into the optical system, users should first verify that the splice is of good quality at a low optical power prior to high-power use. Poor splice quality may increase light scattering at the splice interface, which can be a source of fiber damage.
-
Users should use low power when aligning the system and optimizing coupling; this minimizes exposure of other parts of the fiber (other than the core) to light. Damage from scattered light can occur if a high power beam is focused on the cladding, coating, or connector.
Tips for Using Fiber at Higher Optical Power
Optical fibers and fiber components should generally be operated within safe power level limits, but under ideal conditions (very good optical alignment and very clean optical end faces), the power handling of a fiber component may be increased. Users must verify the performance and stability of a fiber component within their system prior to increasing input or output power and follow all necessary safety and operation instructions. The tips below are useful suggestions when considering increasing optical power in an optical fiber or component.
-
Splicing a fiber component into a system using a fiber splicer can increase power handling as it minimizes possibility of air/fiber interface damage. Users should follow all appropriate guidelines to prepare and make a high-quality fiber splice. Poor splices can lead to scattering or regions of highly localized heat at the splice interface that can damage the fiber.
-
After connecting the fiber or component, the system should be tested and aligned using a light source at low power. The system power can be ramped up slowly to the desired output power while periodically verifying all components are properly aligned and that coupling efficiency is not changing with respect to optical launch power.
-
Bend losses that result from sharply bending a fiber can cause light to leak from the fiber in the stressed area. When operating at high power, the localized heating that can occur when a large amount of light escapes a small localized area (the stressed region) can damage the fiber. Avoid disturbing or accidently bending fibers during operation to minimize bend losses.
-
Users should always choose the appropriate optical fiber for a given application. For example, large-mode-area fibers are a good alternative to standard single mode fibers in high-power applications as they provide good beam quality with a larger MFD, decreasing the power density on the air/fiber interface.
-
Step-index silica single mode fibers are normally not used for ultraviolet light or high-peak-power pulsed applications due to the high spatial power densities associated with these applications.
Posted Comments: | |
Taylor Davis
 (posted 2024-08-12 08:08:34.957) What is the exact material breakdown (core/cladding/coating) of the fiber? The spec sheet and website seem to differ slightly. My guess is Pure silica core, no cladding, and UV-cured dual acrylate coating. Is that right? cdolbashian
 (posted 2024-08-14 11:33:40.0) Thank you for reaching out to us with this inquiry. I have contacted you directly to share all of the information which we have available regarding this fiber. 跃 徐
 (posted 2023-06-29 11:33:41.95) 您好,请问这款光纤在450nm、520nm和650nm三个波段的模场直径分别是多少 jpolaris
 (posted 2023-07-03 03:44:40.0) Customer feedback translation:
"Hello, what are the mode field diameters of this fiber in the three bands of 450 nm, 520 nm and 650 nm?"
Answer:
感谢联系Thorlabs!根据理论计算,S405-XP在450nm、520nm和650nm三个波段的模场直径分别为~3.0 μm@450nm, ~3.5 μm@520nm, ~4.8 μm@650nm,供您参考。
Translated answer:
Thanks for contacting Thorlabs! According to theoretical calculations, the mode field diameters of S405-XP in the three bands of 450 nm, 520 nm and 650 nm are ~3.0 μm @ 450nm, ~3.5 μm @ 520nm, ~4.8 μm @ 650nm respectively, for your reference. bdada
 (posted 2011-03-08 18:45:00.0) Response from Buki:
Thank you for your feedback Michael. For the 460HP fiber, at 532nm, the cladding refractive index is about 1.461, and the core refractive index is about 1.467.
For the S460-HP, at 633nm, the core refractive index is about 1.46873 and the cladding refractive index is about 1.46298. michael.ireland
 (posted 2011-03-07 17:47:54.0) I need to know the cladding refractive index (at ~550nm or some nearby wavelength) for the 460HP and S460-HP fibers. This doesnt seem to be given in the spec sheets. bdada
 (posted 2011-03-07 15:24:00.0) Response from Buki.
For single mode fiber, a flat cleave would provide a good optical surface that makes it unnecessary for the end to be polished. We have two products for fiber cleaving: XL411 and S90W. cmarkle
 (posted 2011-03-07 13:37:42.0) I recently bought some optical fiber (460hp) from you guys and was wondering how to polish the ends. My application does not require a connector but it seems the polishing kits do. Can you Help? Adam
 (posted 2010-03-31 19:40:48.0) A response from Adam at Thorlabs to fahd: We have three methods for stripping this type of fiber. The first is using a mechanical stripper, which would not work for your application. The next two might:
Method 2: Chemical
Dip in solvent for a few minutes. Jackets will absorb the solvent
and swell up. Grab fiber between thumb and index finger (with some
tissue in between) and rub swollen portion off.
Method 3: Hot Sulfuric Acid
Hot sulfuric acid (T=150-180°C). Dip a few minutes or until all
acrylate is dissolved. Rinse in clean water after excess acid is
drained off. Then, rinse in acetone, then isopropyl alcohol and
blow dry.
I will email directly with more information about method 2. fahd_ali2000
 (posted 2009-11-24 05:37:46.0) Hello, i have bought SMF-28-100. I have a problem of stripping this fiber. I want to strip from middle in 1 meter fiber but could not, it always break.
its very rough from inside. dont know what to do.
I appreciate if you can help me.
thanks
bye |

Stock Patch Cables Available with These Fibers | ||
---|---|---|
SM600 Fiber |
Custom cables are also available. Click here for details.
Features
- Shipped from Stock
- No Minimums
- True Single Mode Operation for HeNe and All Visible Laser Diodes
- Acrylate Coating
- Exceptional Core/Clad Concentricity
- 630HP Offers Tight Second Mode Cut-Off Tolerances
Item # | Operating Wavelength | Mode Field Diameter | Cladding | Coating | Cut-Off Wavelengthc |
---|---|---|---|---|---|
SM600 | 633 -780 nma | 3.6 - 5.3 µm @ 633 nmb | 125 ± 1 µm | 245 ± 15 µm | 500 - 600 nm |
S630-HP | 630 - 860 nm | 4.2 ± 0.5 µm @ 630 nm | 125 ± 1.0 µm | 245 ± 15 µm | 590 ± 30 nm |
630HP | 600 - 770 nm | 4.0 ± 0.5 µm @ 630 nm | 125 ± 1 µm | 245 ± 15 µm | 570 ± 30 nm |
Item # | Short-Term Bend Radius | Long-Term Bend Radius | Max Attenuation | NA | Core Index | Cladding Index |
---|---|---|---|---|---|---|
SM600 | ≥5 mm | ≥25 mm | ≤15 dB/kmd | 0.10 - 0.14 | 600 nm: 1.46147e 700 nm: 1.45872e 800 nm: 1.45675e |
600 nm: 1.45804e 700 nm: 1.45530e 800 nm: 1.45332e |
S630-HP | ≥6 mm | ≥13 mm | ≤10 dB/km @ 630 nm | 0.12 | Callf | Callf |
630HP | ≥6 mm | ≥13 mm | ≤12 dB/km @ 630 nm | 0.13 | Callf | Callf |

Click to Enlarge
The left image shows the intensity profile of the beam propagated through the fiber overlaid on the fiber itself. The right image shows the standard intensity profile of the beam propagated through the fiber with the MFD and core diameter called out.
Definition of the Mode Field Diameter
The mode field diameter (MFD) is one measure of the beam width of light propagating in a single mode fiber. It is a function of wavelength, core radius, and the refractive indices of the core and cladding. While much of the light in an optical fiber is trapped within the fiber core, a small fraction propagates in the cladding. The light can be approximated as a Gaussian power distribution as shown to the right, where the MFD is the diameter at which the optical power is reduced to 1/e2 from its peak level.
Measurement of MFD
The measurement of MFD is accomplished by the Variable Aperture Method in the Far Field (VAMFF). An aperture is placed in the far field of the fiber output, and the intensity is measured. As successively smaller apertures are placed in the beam, the intensity levels are measured for each aperture; the data can then be plotted as power vs. the sine of the aperture half-angle (or the numerical aperture for an SM fiber).
The MFD is then determined using Petermann's second definition, which is a mathematical model that does not assume a specific shape of power distribution. The MFD in the near field can be determined from this far-field measurement using the Hankel Transform.
Quick Links |
---|
Damage at the Air / Glass Interface |
Intrinsic Damage Threshold |
Preparation and Handling of Optical Fibers |
Laser-Induced Damage in Silica Optical Fibers
The following tutorial details damage mechanisms relevant to unterminated (bare) fiber, terminated optical fiber, and other fiber components from laser light sources. These mechanisms include damage that occurs at the air / glass interface (when free-space coupling or when using connectors) and in the optical fiber itself. A fiber component, such as a bare fiber, patch cable, or fused coupler, may have multiple potential avenues for damage (e.g., connectors, fiber end faces, and the device itself). The maximum power that a fiber can handle will always be limited by the lowest limit of any of these damage mechanisms.
While the damage threshold can be estimated using scaling relations and general rules, absolute damage thresholds in optical fibers are very application dependent and user specific. Users can use this guide to estimate a safe power level that minimizes the risk of damage. Following all appropriate preparation and handling guidelines, users should be able to operate a fiber component up to the specified maximum power level; if no maximum is specified for a component, users should abide by the "practical safe level" described below for safe operation of the component. Factors that can reduce power handling and cause damage to a fiber component include, but are not limited to, misalignment during fiber coupling, contamination of the fiber end face, or imperfections in the fiber itself. For further discussion about an optical fiber’s power handling abilities for a specific application, please contact Thorlabs’ Tech Support.

Click to Enlarge
Undamaged Fiber End

Click to Enlarge
Damaged Fiber End
Damage at the Air / Glass Interface
There are several potential damage mechanisms that can occur at the air / glass interface. Light is incident on this interface when free-space coupling or when two fibers are mated using optical connectors. High-intensity light can damage the end face leading to reduced power handling and permanent damage to the fiber. For fibers terminated with optical connectors where the connectors are fixed to the fiber ends using epoxy, the heat generated by high-intensity light can burn the epoxy and leave residues on the fiber facet directly in the beam path.
Estimated Optical Power Densities on Air / Glass Interfacea | ||
---|---|---|
Type | Theoretical Damage Thresholdb | Practical Safe Levelc |
CW (Average Power) |
~1 MW/cm2 | ~250 kW/cm2 |
10 ns Pulsed (Peak Power) |
~5 GW/cm2 | ~1 GW/cm2 |
Damage Mechanisms on the Bare Fiber End Face
Damage mechanisms on a fiber end face can be modeled similarly to bulk optics, and industry-standard damage thresholds for UV Fused Silica substrates can be applied to silica-based fiber. However, unlike bulk optics, the relevant surface areas and beam diameters involved at the air / glass interface of an optical fiber are very small, particularly for coupling into single mode (SM) fiber. therefore, for a given power density, the power incident on the fiber needs to be lower for a smaller beam diameter.
The table to the right lists two thresholds for optical power densities: a theoretical damage threshold and a "practical safe level". In general, the theoretical damage threshold represents the estimated maximum power density that can be incident on the fiber end face without risking damage with very good fiber end face and coupling conditions. The "practical safe level" power density represents minimal risk of fiber damage. Operating a fiber or component beyond the practical safe level is possible, but users must follow the appropriate handling instructions and verify performance at low powers prior to use.
Calculating the Effective Area for Single Mode Fibers
The effective area for single mode (SM) fiber is defined by the mode field diameter (MFD), which is the cross-sectional area through which light propagates in the fiber; this area includes the fiber core and also a portion of the cladding. To achieve good efficiency when coupling into a single mode fiber, the diameter of the input beam must match the MFD of the fiber.
As an example, SM400 single mode fiber has a mode field diameter (MFD) of ~Ø3 µm operating at 400 nm, while the MFD for SMF-28 Ultra single mode fiber operating at 1550 nm is Ø10.5 µm. The effective area for these fibers can be calculated as follows:
SM400 Fiber: Area = Pi x (MFD/2)2 = Pi x (1.5 µm)2 = 7.07 µm2 = 7.07 x 10-8 cm2
SMF-28 Ultra Fiber: Area = Pi x (MFD/2)2 = Pi x (5.25 µm)2 = 86.6 µm2 = 8.66 x 10-7 cm2
To estimate the power level that a fiber facet can handle, the power density is multiplied by the effective area. Please note that this calculation assumes a uniform intensity profile, but most laser beams exhibit a Gaussian-like shape within single mode fiber, resulting in a higher power density at the center of the beam compared to the edges. Therefore, these calculations will slightly overestimate the power corresponding to the damage threshold or the practical safe level. Using the estimated power densities assuming a CW light source, we can determine the corresponding power levels as:
SM400 Fiber: 7.07 x 10-8 cm2 x 1 MW/cm2 = 7.1 x 10-8 MW = 71 mW (Theoretical Damage Threshold)
7.07 x 10-8 cm2 x 250 kW/cm2 = 1.8 x 10-5 kW = 18 mW (Practical Safe Level)
SMF-28 Ultra Fiber: 8.66 x 10-7 cm2 x 1 MW/cm2 = 8.7 x 10-7 MW = 870 mW (Theoretical Damage Threshold)
8.66 x 10-7 cm2 x 250 kW/cm2 = 2.1 x 10-4 kW = 210 mW (Practical Safe Level)
Effective Area of Multimode Fibers
The effective area of a multimode (MM) fiber is defined by the core diameter, which is typically far larger than the MFD of an SM fiber. For optimal coupling, Thorlabs recommends focusing a beam to a spot roughly 70 - 80% of the core diameter. The larger effective area of MM fibers lowers the power density on the fiber end face, allowing higher optical powers (typically on the order of kilowatts) to be coupled into multimode fiber without damage.
Damage Mechanisms Related to Ferrule / Connector Termination

Plot showing approximate input power that can be incident on a single mode silica optical fiber with a termination. Each line shows the estimated power level due to a specific damage mechanism. The maximum power handling is limited by the lowest power level from all relevant damage mechanisms (indicated by a solid line).
Fibers terminated with optical connectors have additional power handling considerations. Fiber is typically terminated using epoxy to bond the fiber to a ceramic or steel ferrule. When light is coupled into the fiber through a connector, light that does not enter the core and propagate down the fiber is scattered into the outer layers of the fiber, into the ferrule, and the epoxy used to hold the fiber in the ferrule. If the light is intense enough, it can burn the epoxy, causing it to vaporize and deposit a residue on the face of the connector. This results in localized absorption sites on the fiber end face that reduce coupling efficiency and increase scattering, causing further damage.
For several reasons, epoxy-related damage is dependent on the wavelength. In general, light scatters more strongly at short wavelengths than at longer wavelengths. Misalignment when coupling is also more likely due to the small MFD of short-wavelength SM fiber that also produces more scattered light.
To minimize the risk of burning the epoxy, fiber connectors can be constructed to have an epoxy-free air gap between the optical fiber and ferrule near the fiber end face. Our high-power multimode fiber patch cables use connectors with this design feature.
Determining Power Handling with Multiple Damage Mechanisms
When fiber cables or components have multiple avenues for damage (e.g., fiber patch cables), the maximum power handling is always limited by the lowest damage threshold that is relevant to the fiber component. In general, this represents the highest input power that can be incident on the patch cable end face and not the coupled output power.
As an illustrative example, the graph to the right shows an estimate of the power handling limitations of a single mode fiber patch cable due to damage to the fiber end face and damage via an optical connector. The total input power handling of a terminated fiber at a given wavelength is limited by the lower of the two limitations at any given wavelength (indicated by the solid lines). A single mode fiber operating at around 488 nm is primarily limited by damage to the fiber end face (blue solid line), but fibers operating at 1550 nm are limited by damage to the optical connector (red solid line).
In the case of a multimode fiber, the effective mode area is defined by the core diameter, which is larger than the effective mode area for SM fiber. This results in a lower power density on the fiber end face and allows higher optical powers (on the order of kilowatts) to be coupled into the fiber without damage (not shown in graph). However, the damage limit of the ferrule / connector termination remains unchanged and as a result, the maximum power handling for a multimode fiber is limited by the ferrule and connector termination.
Please note that these are rough estimates of power levels where damage is very unlikely with proper handling and alignment procedures. It is worth noting that optical fibers are frequently used at power levels above those described here. However, these applications typically require expert users and testing at lower powers first to minimize risk of damage. Even still, optical fiber components should be considered a consumable lab supply if used at high power levels.
Intrinsic Damage Threshold
In addition to damage mechanisms at the air / glass interface, optical fibers also display power handling limitations due to damage mechanisms within the optical fiber itself. These limitations will affect all fiber components as they are intrinsic to the fiber itself. Two categories of damage within the fiber are damage from bend losses and damage from photodarkening.
Bend Losses
Bend losses occur when a fiber is bent to a point where light traveling in the core is incident on the core/cladding interface at an angle higher than the critical angle, making total internal reflection impossible. Under these circumstances, light escapes the fiber, often in a localized area. The light escaping the fiber typically has a high power density, which burns the fiber coating as well as any surrounding furcation tubing.
A special category of optical fiber, called double-clad fiber, can reduce the risk of bend-loss damage by allowing the fiber’s cladding (2nd layer) to also function as a waveguide in addition to the core. By making the critical angle of the cladding/coating interface higher than the critical angle of the core/clad interface, light that escapes the core is loosely confined within the cladding. It will then leak out over a distance of centimeters or meters instead of at one localized spot within the fiber, minimizing the risk of damage. Thorlabs manufactures and sells 0.22 NA double-clad multimode fiber, which boasts very high, megawatt range power handling.
Photodarkening
A second damage mechanism, called photodarkening or solarization, can occur in fibers used with ultraviolet or short-wavelength visible light, particularly those with germanium-doped cores. Fibers used at these wavelengths will experience increased attenuation over time. The mechanism that causes photodarkening is largely unknown, but several fiber designs have been developed to mitigate it. For example, fibers with a very low hydroxyl ion (OH) content have been found to resist photodarkening and using other dopants, such as fluorine, can also reduce photodarkening.
Even with the above strategies in place, all fibers eventually experience photodarkening when used with UV or short-wavelength light, and thus, fibers used at these wavelengths should be considered consumables.
Preparation and Handling of Optical Fibers
General Cleaning and Operation Guidelines
These general cleaning and operation guidelines are recommended for all fiber optic products. Users should still follow specific guidelines for an individual product as outlined in the support documentation or manual. Damage threshold calculations only apply when all appropriate cleaning and handling procedures are followed.
-
All light sources should be turned off prior to installing or integrating optical fibers (terminated or bare). This ensures that focused beams of light are not incident on fragile parts of the connector or fiber, which can possibly cause damage.
-
The power-handling capability of an optical fiber is directly linked to the quality of the fiber/connector end face. Always inspect the fiber end prior to connecting the fiber to an optical system. The fiber end face should be clean and clear of dirt and other contaminants that can cause scattering of coupled light. Bare fiber should be cleaved prior to use and users should inspect the fiber end to ensure a good quality cleave is achieved.
-
If an optical fiber is to be spliced into the optical system, users should first verify that the splice is of good quality at a low optical power prior to high-power use. Poor splice quality may increase light scattering at the splice interface, which can be a source of fiber damage.
-
Users should use low power when aligning the system and optimizing coupling; this minimizes exposure of other parts of the fiber (other than the core) to light. Damage from scattered light can occur if a high power beam is focused on the cladding, coating, or connector.
Tips for Using Fiber at Higher Optical Power
Optical fibers and fiber components should generally be operated within safe power level limits, but under ideal conditions (very good optical alignment and very clean optical end faces), the power handling of a fiber component may be increased. Users must verify the performance and stability of a fiber component within their system prior to increasing input or output power and follow all necessary safety and operation instructions. The tips below are useful suggestions when considering increasing optical power in an optical fiber or component.
-
Splicing a fiber component into a system using a fiber splicer can increase power handling as it minimizes possibility of air/fiber interface damage. Users should follow all appropriate guidelines to prepare and make a high-quality fiber splice. Poor splices can lead to scattering or regions of highly localized heat at the splice interface that can damage the fiber.
-
After connecting the fiber or component, the system should be tested and aligned using a light source at low power. The system power can be ramped up slowly to the desired output power while periodically verifying all components are properly aligned and that coupling efficiency is not changing with respect to optical launch power.
-
Bend losses that result from sharply bending a fiber can cause light to leak from the fiber in the stressed area. When operating at high power, the localized heating that can occur when a large amount of light escapes a small localized area (the stressed region) can damage the fiber. Avoid disturbing or accidently bending fibers during operation to minimize bend losses.
-
Users should always choose the appropriate optical fiber for a given application. For example, large-mode-area fibers are a good alternative to standard single mode fibers in high-power applications as they provide good beam quality with a larger MFD, decreasing the power density on the air/fiber interface.
-
Step-index silica single mode fibers are normally not used for ultraviolet light or high-peak-power pulsed applications due to the high spatial power densities associated with these applications.
Posted Comments: | |
Taylor Davis
 (posted 2024-08-12 08:06:06.767) Could you please provide the exact materials (core/cladding/coating) used in the 630HP fiber? It is somewhat unclear between the spec sheet and the website. Nearest I can tell, I'm guessing a pure silica core (never mentioned), no cladding, and UV-cured dual acrylate coating? Is that right? cdolbashian
 (posted 2024-08-14 11:33:41.0) Thank you for reaching out to us with this inquiry. I have contacted you directly to share all of the information which we have available regarding this fiber. nhatquang85
 (posted 2018-08-28 00:39:21.39) Dear Thorlabs,
I am using four types of fiber: SMF-28, S630HP, 630HP, and 780HP.
I would like to know the dispersion at around 532 nm and the zero dispersion of the fibers. Could you please let me know these value?
Thanks! nbayconich
 (posted 2018-10-26 09:44:50.0) Thank you for contacting Thorlabs. SMF-28 is designed to have zero dispersion at 1310nm for telecom communications.
The dispersion at 532nm for S630-HP about -450(ps/km*nm). Please note this is theoretical data and not something that we spec. I will reach out to you with more information. david.panak
 (posted 2018-03-12 12:43:49.113) are your P1-630AR-2 AR coated fibers that are made with SM600 fiber "compatible" with the TNQ630HF 1x4 fiber couplers made with 630HP fiber? What amount of loss should I expect at a FC-FC coupler? nbayconich
 (posted 2018-03-21 01:48:47.0) Thank you for contacting Thorlabs. You can couple SM600 fiber to 630HP fiber however there will be some additional loss due to mode field diameter mis-match between SM600 to 630HP. The MFD of 630HP is typically 4µm ±0.5µm where as SM600 can range from 3.6 - 5.3µm. Our typical insertion loss per FC/PC connection for SM600 fiber patch cables will be about 2 dB which includes loss due to the mechanical tolerances of the bore alignment and concentricity of the fiber. In the case of a MFD mismatch between 630HP and SM600 this would result in a 0.34 dB per connection assuming the centers of the fiber core are aligned not including lateral misalignment.
AR coated ends of the P1-630AR-2 must only be used with an air to glass interface. I will reach out to you directly with more information. Thorlabs
 (posted 2010-12-07 15:53:01.0) Response from Javier at Thorlabs to Peter: We will gladly send you a quotation. we will contact you shortly to get your contact details. taenzer
 (posted 2010-12-07 14:54:24.0) please send me offer for 2000 m of single mode fibre SM600
thanks
Peter Taenzer, Germany |

Stock Patch Cables Available with These Fibers | ||
---|---|---|
780HP Fiber |
SM800-5.6-125 Fiber |
Custom cables are also available. Click here for details.
Features
- Shipped from Stock
- No Minimums
- Acrylate Jacket
- Exceptional Uniformity
- Exceptional Core/Clad Concentricity
- 780HP Offers Tight Second Mode Cut-Off Tolerances
- SM800G80 Offers Enhanced Bend Insensitivity
Item # | Operating Wavelength | Mode Field Diameter | Cladding | Coating | Cut-Off Wavelength |
---|---|---|---|---|---|
780HP | 780 - 970 nm | 5.0 ± 0.5 µm @ 850 nm | 125 ± 1 µm | 245 ± 15 µm | 730 ± 30 nm |
SM800-5.6-125 | 830 - 980 nma | 4.7 - 6.9 µmb @ 830 nm | 125 ± 1.0 µm | 245 ± 15 µm | 660 - 800 nm |
SM800G80 | 830 - 980 nma | 3.75 - 4.9 µm @ 830 nm | 80 ± 1 µm | 170 ± 10 µm | 660 - 800 nm |
Item # | Short-Term Bend Radius | Long-Term Bend Radius | Attenuation (Max) | NA | Core Index | Cladding Index |
---|---|---|---|---|---|---|
780HP | ≥6 mm | ≥13 mm | ≤4.0 dB/km @ 780 nm ≤3.5 dB/km @ 850 nm |
0.13 | Calld | Calld |
SM800-5.6-125 | ≥5 mm | ≥25 mm | <5 dB/kmc | 0.10 - 0.14 | 830 nm: 1.45625e | 830 nm: 1.45282e |
SM800G80 | ≥5 mm | ≥12 mm (or 38 mm for 25 Year Life) |
≤3.0 dB/kmc | 0.14 - 0.18 | 830 nm: 1.45954f | 830 nm: 1.45282f |

Click to Enlarge
The left image shows the intensity profile of the beam propagated through the fiber overlaid on the fiber itself. The right image shows the standard intensity profile of the beam propagated through the fiber with the MFD and core diameter called out.
Definition of the Mode Field Diameter
The mode field diameter (MFD) is one measure of the beam width of light propagating in a single mode fiber. It is a function of wavelength, core radius, and the refractive indices of the core and cladding. While much of the light in an optical fiber is trapped within the fiber core, a small fraction propagates in the cladding. The light can be approximated as a Gaussian power distribution as shown to the right, where the MFD is the diameter at which the optical power is reduced to 1/e2 from its peak level.
Measurement of MFD
The measurement of MFD is accomplished by the Variable Aperture Method in the Far Field (VAMFF). An aperture is placed in the far field of the fiber output, and the intensity is measured. As successively smaller apertures are placed in the beam, the intensity levels are measured for each aperture; the data can then be plotted as power vs. the sine of the aperture half-angle (or the numerical aperture for an SM fiber).
The MFD is then determined using Petermann's second definition, which is a mathematical model that does not assume a specific shape of power distribution. The MFD in the near field can be determined from this far-field measurement using the Hankel Transform.
Quick Links |
---|
Damage at the Air / Glass Interface |
Intrinsic Damage Threshold |
Preparation and Handling of Optical Fibers |
Laser-Induced Damage in Silica Optical Fibers
The following tutorial details damage mechanisms relevant to unterminated (bare) fiber, terminated optical fiber, and other fiber components from laser light sources. These mechanisms include damage that occurs at the air / glass interface (when free-space coupling or when using connectors) and in the optical fiber itself. A fiber component, such as a bare fiber, patch cable, or fused coupler, may have multiple potential avenues for damage (e.g., connectors, fiber end faces, and the device itself). The maximum power that a fiber can handle will always be limited by the lowest limit of any of these damage mechanisms.
While the damage threshold can be estimated using scaling relations and general rules, absolute damage thresholds in optical fibers are very application dependent and user specific. Users can use this guide to estimate a safe power level that minimizes the risk of damage. Following all appropriate preparation and handling guidelines, users should be able to operate a fiber component up to the specified maximum power level; if no maximum is specified for a component, users should abide by the "practical safe level" described below for safe operation of the component. Factors that can reduce power handling and cause damage to a fiber component include, but are not limited to, misalignment during fiber coupling, contamination of the fiber end face, or imperfections in the fiber itself. For further discussion about an optical fiber’s power handling abilities for a specific application, please contact Thorlabs’ Tech Support.

Click to Enlarge
Undamaged Fiber End

Click to Enlarge
Damaged Fiber End
Damage at the Air / Glass Interface
There are several potential damage mechanisms that can occur at the air / glass interface. Light is incident on this interface when free-space coupling or when two fibers are mated using optical connectors. High-intensity light can damage the end face leading to reduced power handling and permanent damage to the fiber. For fibers terminated with optical connectors where the connectors are fixed to the fiber ends using epoxy, the heat generated by high-intensity light can burn the epoxy and leave residues on the fiber facet directly in the beam path.
Estimated Optical Power Densities on Air / Glass Interfacea | ||
---|---|---|
Type | Theoretical Damage Thresholdb | Practical Safe Levelc |
CW (Average Power) |
~1 MW/cm2 | ~250 kW/cm2 |
10 ns Pulsed (Peak Power) |
~5 GW/cm2 | ~1 GW/cm2 |
Damage Mechanisms on the Bare Fiber End Face
Damage mechanisms on a fiber end face can be modeled similarly to bulk optics, and industry-standard damage thresholds for UV Fused Silica substrates can be applied to silica-based fiber. However, unlike bulk optics, the relevant surface areas and beam diameters involved at the air / glass interface of an optical fiber are very small, particularly for coupling into single mode (SM) fiber. therefore, for a given power density, the power incident on the fiber needs to be lower for a smaller beam diameter.
The table to the right lists two thresholds for optical power densities: a theoretical damage threshold and a "practical safe level". In general, the theoretical damage threshold represents the estimated maximum power density that can be incident on the fiber end face without risking damage with very good fiber end face and coupling conditions. The "practical safe level" power density represents minimal risk of fiber damage. Operating a fiber or component beyond the practical safe level is possible, but users must follow the appropriate handling instructions and verify performance at low powers prior to use.
Calculating the Effective Area for Single Mode Fibers
The effective area for single mode (SM) fiber is defined by the mode field diameter (MFD), which is the cross-sectional area through which light propagates in the fiber; this area includes the fiber core and also a portion of the cladding. To achieve good efficiency when coupling into a single mode fiber, the diameter of the input beam must match the MFD of the fiber.
As an example, SM400 single mode fiber has a mode field diameter (MFD) of ~Ø3 µm operating at 400 nm, while the MFD for SMF-28 Ultra single mode fiber operating at 1550 nm is Ø10.5 µm. The effective area for these fibers can be calculated as follows:
SM400 Fiber: Area = Pi x (MFD/2)2 = Pi x (1.5 µm)2 = 7.07 µm2 = 7.07 x 10-8 cm2
SMF-28 Ultra Fiber: Area = Pi x (MFD/2)2 = Pi x (5.25 µm)2 = 86.6 µm2 = 8.66 x 10-7 cm2
To estimate the power level that a fiber facet can handle, the power density is multiplied by the effective area. Please note that this calculation assumes a uniform intensity profile, but most laser beams exhibit a Gaussian-like shape within single mode fiber, resulting in a higher power density at the center of the beam compared to the edges. Therefore, these calculations will slightly overestimate the power corresponding to the damage threshold or the practical safe level. Using the estimated power densities assuming a CW light source, we can determine the corresponding power levels as:
SM400 Fiber: 7.07 x 10-8 cm2 x 1 MW/cm2 = 7.1 x 10-8 MW = 71 mW (Theoretical Damage Threshold)
7.07 x 10-8 cm2 x 250 kW/cm2 = 1.8 x 10-5 kW = 18 mW (Practical Safe Level)
SMF-28 Ultra Fiber: 8.66 x 10-7 cm2 x 1 MW/cm2 = 8.7 x 10-7 MW = 870 mW (Theoretical Damage Threshold)
8.66 x 10-7 cm2 x 250 kW/cm2 = 2.1 x 10-4 kW = 210 mW (Practical Safe Level)
Effective Area of Multimode Fibers
The effective area of a multimode (MM) fiber is defined by the core diameter, which is typically far larger than the MFD of an SM fiber. For optimal coupling, Thorlabs recommends focusing a beam to a spot roughly 70 - 80% of the core diameter. The larger effective area of MM fibers lowers the power density on the fiber end face, allowing higher optical powers (typically on the order of kilowatts) to be coupled into multimode fiber without damage.
Damage Mechanisms Related to Ferrule / Connector Termination

Plot showing approximate input power that can be incident on a single mode silica optical fiber with a termination. Each line shows the estimated power level due to a specific damage mechanism. The maximum power handling is limited by the lowest power level from all relevant damage mechanisms (indicated by a solid line).
Fibers terminated with optical connectors have additional power handling considerations. Fiber is typically terminated using epoxy to bond the fiber to a ceramic or steel ferrule. When light is coupled into the fiber through a connector, light that does not enter the core and propagate down the fiber is scattered into the outer layers of the fiber, into the ferrule, and the epoxy used to hold the fiber in the ferrule. If the light is intense enough, it can burn the epoxy, causing it to vaporize and deposit a residue on the face of the connector. This results in localized absorption sites on the fiber end face that reduce coupling efficiency and increase scattering, causing further damage.
For several reasons, epoxy-related damage is dependent on the wavelength. In general, light scatters more strongly at short wavelengths than at longer wavelengths. Misalignment when coupling is also more likely due to the small MFD of short-wavelength SM fiber that also produces more scattered light.
To minimize the risk of burning the epoxy, fiber connectors can be constructed to have an epoxy-free air gap between the optical fiber and ferrule near the fiber end face. Our high-power multimode fiber patch cables use connectors with this design feature.
Determining Power Handling with Multiple Damage Mechanisms
When fiber cables or components have multiple avenues for damage (e.g., fiber patch cables), the maximum power handling is always limited by the lowest damage threshold that is relevant to the fiber component. In general, this represents the highest input power that can be incident on the patch cable end face and not the coupled output power.
As an illustrative example, the graph to the right shows an estimate of the power handling limitations of a single mode fiber patch cable due to damage to the fiber end face and damage via an optical connector. The total input power handling of a terminated fiber at a given wavelength is limited by the lower of the two limitations at any given wavelength (indicated by the solid lines). A single mode fiber operating at around 488 nm is primarily limited by damage to the fiber end face (blue solid line), but fibers operating at 1550 nm are limited by damage to the optical connector (red solid line).
In the case of a multimode fiber, the effective mode area is defined by the core diameter, which is larger than the effective mode area for SM fiber. This results in a lower power density on the fiber end face and allows higher optical powers (on the order of kilowatts) to be coupled into the fiber without damage (not shown in graph). However, the damage limit of the ferrule / connector termination remains unchanged and as a result, the maximum power handling for a multimode fiber is limited by the ferrule and connector termination.
Please note that these are rough estimates of power levels where damage is very unlikely with proper handling and alignment procedures. It is worth noting that optical fibers are frequently used at power levels above those described here. However, these applications typically require expert users and testing at lower powers first to minimize risk of damage. Even still, optical fiber components should be considered a consumable lab supply if used at high power levels.
Intrinsic Damage Threshold
In addition to damage mechanisms at the air / glass interface, optical fibers also display power handling limitations due to damage mechanisms within the optical fiber itself. These limitations will affect all fiber components as they are intrinsic to the fiber itself. Two categories of damage within the fiber are damage from bend losses and damage from photodarkening.
Bend Losses
Bend losses occur when a fiber is bent to a point where light traveling in the core is incident on the core/cladding interface at an angle higher than the critical angle, making total internal reflection impossible. Under these circumstances, light escapes the fiber, often in a localized area. The light escaping the fiber typically has a high power density, which burns the fiber coating as well as any surrounding furcation tubing.
A special category of optical fiber, called double-clad fiber, can reduce the risk of bend-loss damage by allowing the fiber’s cladding (2nd layer) to also function as a waveguide in addition to the core. By making the critical angle of the cladding/coating interface higher than the critical angle of the core/clad interface, light that escapes the core is loosely confined within the cladding. It will then leak out over a distance of centimeters or meters instead of at one localized spot within the fiber, minimizing the risk of damage. Thorlabs manufactures and sells 0.22 NA double-clad multimode fiber, which boasts very high, megawatt range power handling.
Photodarkening
A second damage mechanism, called photodarkening or solarization, can occur in fibers used with ultraviolet or short-wavelength visible light, particularly those with germanium-doped cores. Fibers used at these wavelengths will experience increased attenuation over time. The mechanism that causes photodarkening is largely unknown, but several fiber designs have been developed to mitigate it. For example, fibers with a very low hydroxyl ion (OH) content have been found to resist photodarkening and using other dopants, such as fluorine, can also reduce photodarkening.
Even with the above strategies in place, all fibers eventually experience photodarkening when used with UV or short-wavelength light, and thus, fibers used at these wavelengths should be considered consumables.
Preparation and Handling of Optical Fibers
General Cleaning and Operation Guidelines
These general cleaning and operation guidelines are recommended for all fiber optic products. Users should still follow specific guidelines for an individual product as outlined in the support documentation or manual. Damage threshold calculations only apply when all appropriate cleaning and handling procedures are followed.
-
All light sources should be turned off prior to installing or integrating optical fibers (terminated or bare). This ensures that focused beams of light are not incident on fragile parts of the connector or fiber, which can possibly cause damage.
-
The power-handling capability of an optical fiber is directly linked to the quality of the fiber/connector end face. Always inspect the fiber end prior to connecting the fiber to an optical system. The fiber end face should be clean and clear of dirt and other contaminants that can cause scattering of coupled light. Bare fiber should be cleaved prior to use and users should inspect the fiber end to ensure a good quality cleave is achieved.
-
If an optical fiber is to be spliced into the optical system, users should first verify that the splice is of good quality at a low optical power prior to high-power use. Poor splice quality may increase light scattering at the splice interface, which can be a source of fiber damage.
-
Users should use low power when aligning the system and optimizing coupling; this minimizes exposure of other parts of the fiber (other than the core) to light. Damage from scattered light can occur if a high power beam is focused on the cladding, coating, or connector.
Tips for Using Fiber at Higher Optical Power
Optical fibers and fiber components should generally be operated within safe power level limits, but under ideal conditions (very good optical alignment and very clean optical end faces), the power handling of a fiber component may be increased. Users must verify the performance and stability of a fiber component within their system prior to increasing input or output power and follow all necessary safety and operation instructions. The tips below are useful suggestions when considering increasing optical power in an optical fiber or component.
-
Splicing a fiber component into a system using a fiber splicer can increase power handling as it minimizes possibility of air/fiber interface damage. Users should follow all appropriate guidelines to prepare and make a high-quality fiber splice. Poor splices can lead to scattering or regions of highly localized heat at the splice interface that can damage the fiber.
-
After connecting the fiber or component, the system should be tested and aligned using a light source at low power. The system power can be ramped up slowly to the desired output power while periodically verifying all components are properly aligned and that coupling efficiency is not changing with respect to optical launch power.
-
Bend losses that result from sharply bending a fiber can cause light to leak from the fiber in the stressed area. When operating at high power, the localized heating that can occur when a large amount of light escapes a small localized area (the stressed region) can damage the fiber. Avoid disturbing or accidently bending fibers during operation to minimize bend losses.
-
Users should always choose the appropriate optical fiber for a given application. For example, large-mode-area fibers are a good alternative to standard single mode fibers in high-power applications as they provide good beam quality with a larger MFD, decreasing the power density on the air/fiber interface.
-
Step-index silica single mode fibers are normally not used for ultraviolet light or high-peak-power pulsed applications due to the high spatial power densities associated with these applications.
Posted Comments: | |
No Comments Posted |

Stock Patch Cables Available with These Fibers | ||
---|---|---|
SM980-5.8-125 Fiber |
Custom cables are also available. Click here for details.
Features
- Shipped from Stock
- No Minimums
- HI1060-100 and HI1060-J9 have Ø900 µm Tight-Buffer Hytrel Outer Jackets
- SM980-5.8-125 has a MFD Matched to Other Fibers used in EDFA Pump Laser Pigtails
- 980HP and 1060XP Offer a Tight Second Mode Cut-Off Tolerance
- SM980G80 Offers Enhanced Bend Insensitivity
Item # | Operating Wavelength | Mode Field Diameter | Cladding | Coating | Cut-Off Wavelength |
---|---|---|---|---|---|
SM980-5.8-125 | 980 - 1550 nm | 5.3 - 6.4 µm @ 980 nma | 125 ± 1 µm | 245 ± 15 µm | 870 - 970 nm |
SM980G80 | 980 - 1550 nm | 4.2 - 4.9 µm @ 980 nm | 80 ± 1 µm | 170 ± 10 µm | 870 - 970 nm |
1060XP | 980 - 1600 nm | 5.9 ± 0.5 µm @ 980 nm 6.2 ± 0.5 µm @ 1060 nm 9.5 ± 0.5 µm @ 1550 nm |
125 ± 0.5 µm | 245 ± 10 µm | 920 ± 30 nm |
980HP | 980 - 1600 nm | 4.2 ± 0.5 µm @ 980 nm 6.8 ± 0.5 µm @ 1550 nm |
125 ± 1 µm | 245 ± 15 µm | 920 ± 30 nm |
HI1060-J9 | 980 - 1650 nm | 5.9 ± 0.3 µm @ 980 nm 6.2 ± 0.3 µm @ 1060 nm |
125 ± 0.5 µm | 245 ± 10 µm | 920 ± 50 nm |
Item # | Short-Term Bend Radius | Long-Term Bend Radius | Attenuation (Max) | NA | Core Index | Cladding Index |
---|---|---|---|---|---|---|
SM980-5.8-125 | ≥5 mm | ≥25 mm | ≤2.0 dB/kmb | 0.13 - 0.15 | 970 nm: 1.45660c 1310 nm: 1.45259c 1650 nm: 1.44854c |
970 nm: 1.45081c 1310 nm: 1.44680c 1650 nm: 1.44275c |
SM980G80 | ≥5 mm | ≥12 mm (or 38 mm for 25 Year Life) | ≤2 dB/km | 0.17 - 0.19 | 980 nm: 1.46058d 1310 nm: 1.45670d 1650 nm: 1.45265d |
980 nm: 1.45068d 1310 nm: 1.44680d 1650 nm: 1.44275d |
1060XP | ≥6 mm | ≥13 mm | ≤2.1 dB/km @ 980 nm ≤1.5 dB/km @ 1060 nm |
0.14 | Calle | Calle |
980HP | ≥6 mm | ≥13 mm | ≤3.5 dB/km @ 980 nm | 0.20 | Calle | Calle |
HI1060-J9 | - | - | 2.1 dB/km @ 980 nm 1.5 dB/km @1060 nm |
0.14 | Proprietaryf | Proprietaryf |

Click to Enlarge
The left image shows the intensity profile of the beam propagated through the fiber overlaid on the fiber itself. The right image shows the standard intensity profile of the beam propagated through the fiber with the MFD and core diameter called out.
Definition of the Mode Field Diameter
The mode field diameter (MFD) is one measure of the beam width of light propagating in a single mode fiber. It is a function of wavelength, core radius, and the refractive indices of the core and cladding. While much of the light in an optical fiber is trapped within the fiber core, a small fraction propagates in the cladding. The light can be approximated as a Gaussian power distribution as shown to the right, where the MFD is the diameter at which the optical power is reduced to 1/e2 from its peak level.
Measurement of MFD
The measurement of MFD is accomplished by the Variable Aperture Method in the Far Field (VAMFF). An aperture is placed in the far field of the fiber output, and the intensity is measured. As successively smaller apertures are placed in the beam, the intensity levels are measured for each aperture; the data can then be plotted as power vs. the sine of the aperture half-angle (or the numerical aperture for an SM fiber).
The MFD is then determined using Petermann's second definition, which is a mathematical model that does not assume a specific shape of power distribution. The MFD in the near field can be determined from this far-field measurement using the Hankel Transform.
Quick Links |
---|
Damage at the Air / Glass Interface |
Intrinsic Damage Threshold |
Preparation and Handling of Optical Fibers |
Laser-Induced Damage in Silica Optical Fibers
The following tutorial details damage mechanisms relevant to unterminated (bare) fiber, terminated optical fiber, and other fiber components from laser light sources. These mechanisms include damage that occurs at the air / glass interface (when free-space coupling or when using connectors) and in the optical fiber itself. A fiber component, such as a bare fiber, patch cable, or fused coupler, may have multiple potential avenues for damage (e.g., connectors, fiber end faces, and the device itself). The maximum power that a fiber can handle will always be limited by the lowest limit of any of these damage mechanisms.
While the damage threshold can be estimated using scaling relations and general rules, absolute damage thresholds in optical fibers are very application dependent and user specific. Users can use this guide to estimate a safe power level that minimizes the risk of damage. Following all appropriate preparation and handling guidelines, users should be able to operate a fiber component up to the specified maximum power level; if no maximum is specified for a component, users should abide by the "practical safe level" described below for safe operation of the component. Factors that can reduce power handling and cause damage to a fiber component include, but are not limited to, misalignment during fiber coupling, contamination of the fiber end face, or imperfections in the fiber itself. For further discussion about an optical fiber’s power handling abilities for a specific application, please contact Thorlabs’ Tech Support.

Click to Enlarge
Undamaged Fiber End

Click to Enlarge
Damaged Fiber End
Damage at the Air / Glass Interface
There are several potential damage mechanisms that can occur at the air / glass interface. Light is incident on this interface when free-space coupling or when two fibers are mated using optical connectors. High-intensity light can damage the end face leading to reduced power handling and permanent damage to the fiber. For fibers terminated with optical connectors where the connectors are fixed to the fiber ends using epoxy, the heat generated by high-intensity light can burn the epoxy and leave residues on the fiber facet directly in the beam path.
Estimated Optical Power Densities on Air / Glass Interfacea | ||
---|---|---|
Type | Theoretical Damage Thresholdb | Practical Safe Levelc |
CW (Average Power) |
~1 MW/cm2 | ~250 kW/cm2 |
10 ns Pulsed (Peak Power) |
~5 GW/cm2 | ~1 GW/cm2 |
Damage Mechanisms on the Bare Fiber End Face
Damage mechanisms on a fiber end face can be modeled similarly to bulk optics, and industry-standard damage thresholds for UV Fused Silica substrates can be applied to silica-based fiber. However, unlike bulk optics, the relevant surface areas and beam diameters involved at the air / glass interface of an optical fiber are very small, particularly for coupling into single mode (SM) fiber. therefore, for a given power density, the power incident on the fiber needs to be lower for a smaller beam diameter.
The table to the right lists two thresholds for optical power densities: a theoretical damage threshold and a "practical safe level". In general, the theoretical damage threshold represents the estimated maximum power density that can be incident on the fiber end face without risking damage with very good fiber end face and coupling conditions. The "practical safe level" power density represents minimal risk of fiber damage. Operating a fiber or component beyond the practical safe level is possible, but users must follow the appropriate handling instructions and verify performance at low powers prior to use.
Calculating the Effective Area for Single Mode Fibers
The effective area for single mode (SM) fiber is defined by the mode field diameter (MFD), which is the cross-sectional area through which light propagates in the fiber; this area includes the fiber core and also a portion of the cladding. To achieve good efficiency when coupling into a single mode fiber, the diameter of the input beam must match the MFD of the fiber.
As an example, SM400 single mode fiber has a mode field diameter (MFD) of ~Ø3 µm operating at 400 nm, while the MFD for SMF-28 Ultra single mode fiber operating at 1550 nm is Ø10.5 µm. The effective area for these fibers can be calculated as follows:
SM400 Fiber: Area = Pi x (MFD/2)2 = Pi x (1.5 µm)2 = 7.07 µm2 = 7.07 x 10-8 cm2
SMF-28 Ultra Fiber: Area = Pi x (MFD/2)2 = Pi x (5.25 µm)2 = 86.6 µm2 = 8.66 x 10-7 cm2
To estimate the power level that a fiber facet can handle, the power density is multiplied by the effective area. Please note that this calculation assumes a uniform intensity profile, but most laser beams exhibit a Gaussian-like shape within single mode fiber, resulting in a higher power density at the center of the beam compared to the edges. Therefore, these calculations will slightly overestimate the power corresponding to the damage threshold or the practical safe level. Using the estimated power densities assuming a CW light source, we can determine the corresponding power levels as:
SM400 Fiber: 7.07 x 10-8 cm2 x 1 MW/cm2 = 7.1 x 10-8 MW = 71 mW (Theoretical Damage Threshold)
7.07 x 10-8 cm2 x 250 kW/cm2 = 1.8 x 10-5 kW = 18 mW (Practical Safe Level)
SMF-28 Ultra Fiber: 8.66 x 10-7 cm2 x 1 MW/cm2 = 8.7 x 10-7 MW = 870 mW (Theoretical Damage Threshold)
8.66 x 10-7 cm2 x 250 kW/cm2 = 2.1 x 10-4 kW = 210 mW (Practical Safe Level)
Effective Area of Multimode Fibers
The effective area of a multimode (MM) fiber is defined by the core diameter, which is typically far larger than the MFD of an SM fiber. For optimal coupling, Thorlabs recommends focusing a beam to a spot roughly 70 - 80% of the core diameter. The larger effective area of MM fibers lowers the power density on the fiber end face, allowing higher optical powers (typically on the order of kilowatts) to be coupled into multimode fiber without damage.
Damage Mechanisms Related to Ferrule / Connector Termination

Plot showing approximate input power that can be incident on a single mode silica optical fiber with a termination. Each line shows the estimated power level due to a specific damage mechanism. The maximum power handling is limited by the lowest power level from all relevant damage mechanisms (indicated by a solid line).
Fibers terminated with optical connectors have additional power handling considerations. Fiber is typically terminated using epoxy to bond the fiber to a ceramic or steel ferrule. When light is coupled into the fiber through a connector, light that does not enter the core and propagate down the fiber is scattered into the outer layers of the fiber, into the ferrule, and the epoxy used to hold the fiber in the ferrule. If the light is intense enough, it can burn the epoxy, causing it to vaporize and deposit a residue on the face of the connector. This results in localized absorption sites on the fiber end face that reduce coupling efficiency and increase scattering, causing further damage.
For several reasons, epoxy-related damage is dependent on the wavelength. In general, light scatters more strongly at short wavelengths than at longer wavelengths. Misalignment when coupling is also more likely due to the small MFD of short-wavelength SM fiber that also produces more scattered light.
To minimize the risk of burning the epoxy, fiber connectors can be constructed to have an epoxy-free air gap between the optical fiber and ferrule near the fiber end face. Our high-power multimode fiber patch cables use connectors with this design feature.
Determining Power Handling with Multiple Damage Mechanisms
When fiber cables or components have multiple avenues for damage (e.g., fiber patch cables), the maximum power handling is always limited by the lowest damage threshold that is relevant to the fiber component. In general, this represents the highest input power that can be incident on the patch cable end face and not the coupled output power.
As an illustrative example, the graph to the right shows an estimate of the power handling limitations of a single mode fiber patch cable due to damage to the fiber end face and damage via an optical connector. The total input power handling of a terminated fiber at a given wavelength is limited by the lower of the two limitations at any given wavelength (indicated by the solid lines). A single mode fiber operating at around 488 nm is primarily limited by damage to the fiber end face (blue solid line), but fibers operating at 1550 nm are limited by damage to the optical connector (red solid line).
In the case of a multimode fiber, the effective mode area is defined by the core diameter, which is larger than the effective mode area for SM fiber. This results in a lower power density on the fiber end face and allows higher optical powers (on the order of kilowatts) to be coupled into the fiber without damage (not shown in graph). However, the damage limit of the ferrule / connector termination remains unchanged and as a result, the maximum power handling for a multimode fiber is limited by the ferrule and connector termination.
Please note that these are rough estimates of power levels where damage is very unlikely with proper handling and alignment procedures. It is worth noting that optical fibers are frequently used at power levels above those described here. However, these applications typically require expert users and testing at lower powers first to minimize risk of damage. Even still, optical fiber components should be considered a consumable lab supply if used at high power levels.
Intrinsic Damage Threshold
In addition to damage mechanisms at the air / glass interface, optical fibers also display power handling limitations due to damage mechanisms within the optical fiber itself. These limitations will affect all fiber components as they are intrinsic to the fiber itself. Two categories of damage within the fiber are damage from bend losses and damage from photodarkening.
Bend Losses
Bend losses occur when a fiber is bent to a point where light traveling in the core is incident on the core/cladding interface at an angle higher than the critical angle, making total internal reflection impossible. Under these circumstances, light escapes the fiber, often in a localized area. The light escaping the fiber typically has a high power density, which burns the fiber coating as well as any surrounding furcation tubing.
A special category of optical fiber, called double-clad fiber, can reduce the risk of bend-loss damage by allowing the fiber’s cladding (2nd layer) to also function as a waveguide in addition to the core. By making the critical angle of the cladding/coating interface higher than the critical angle of the core/clad interface, light that escapes the core is loosely confined within the cladding. It will then leak out over a distance of centimeters or meters instead of at one localized spot within the fiber, minimizing the risk of damage. Thorlabs manufactures and sells 0.22 NA double-clad multimode fiber, which boasts very high, megawatt range power handling.
Photodarkening
A second damage mechanism, called photodarkening or solarization, can occur in fibers used with ultraviolet or short-wavelength visible light, particularly those with germanium-doped cores. Fibers used at these wavelengths will experience increased attenuation over time. The mechanism that causes photodarkening is largely unknown, but several fiber designs have been developed to mitigate it. For example, fibers with a very low hydroxyl ion (OH) content have been found to resist photodarkening and using other dopants, such as fluorine, can also reduce photodarkening.
Even with the above strategies in place, all fibers eventually experience photodarkening when used with UV or short-wavelength light, and thus, fibers used at these wavelengths should be considered consumables.
Preparation and Handling of Optical Fibers
General Cleaning and Operation Guidelines
These general cleaning and operation guidelines are recommended for all fiber optic products. Users should still follow specific guidelines for an individual product as outlined in the support documentation or manual. Damage threshold calculations only apply when all appropriate cleaning and handling procedures are followed.
-
All light sources should be turned off prior to installing or integrating optical fibers (terminated or bare). This ensures that focused beams of light are not incident on fragile parts of the connector or fiber, which can possibly cause damage.
-
The power-handling capability of an optical fiber is directly linked to the quality of the fiber/connector end face. Always inspect the fiber end prior to connecting the fiber to an optical system. The fiber end face should be clean and clear of dirt and other contaminants that can cause scattering of coupled light. Bare fiber should be cleaved prior to use and users should inspect the fiber end to ensure a good quality cleave is achieved.
-
If an optical fiber is to be spliced into the optical system, users should first verify that the splice is of good quality at a low optical power prior to high-power use. Poor splice quality may increase light scattering at the splice interface, which can be a source of fiber damage.
-
Users should use low power when aligning the system and optimizing coupling; this minimizes exposure of other parts of the fiber (other than the core) to light. Damage from scattered light can occur if a high power beam is focused on the cladding, coating, or connector.
Tips for Using Fiber at Higher Optical Power
Optical fibers and fiber components should generally be operated within safe power level limits, but under ideal conditions (very good optical alignment and very clean optical end faces), the power handling of a fiber component may be increased. Users must verify the performance and stability of a fiber component within their system prior to increasing input or output power and follow all necessary safety and operation instructions. The tips below are useful suggestions when considering increasing optical power in an optical fiber or component.
-
Splicing a fiber component into a system using a fiber splicer can increase power handling as it minimizes possibility of air/fiber interface damage. Users should follow all appropriate guidelines to prepare and make a high-quality fiber splice. Poor splices can lead to scattering or regions of highly localized heat at the splice interface that can damage the fiber.
-
After connecting the fiber or component, the system should be tested and aligned using a light source at low power. The system power can be ramped up slowly to the desired output power while periodically verifying all components are properly aligned and that coupling efficiency is not changing with respect to optical launch power.
-
Bend losses that result from sharply bending a fiber can cause light to leak from the fiber in the stressed area. When operating at high power, the localized heating that can occur when a large amount of light escapes a small localized area (the stressed region) can damage the fiber. Avoid disturbing or accidently bending fibers during operation to minimize bend losses.
-
Users should always choose the appropriate optical fiber for a given application. For example, large-mode-area fibers are a good alternative to standard single mode fibers in high-power applications as they provide good beam quality with a larger MFD, decreasing the power density on the air/fiber interface.
-
Step-index silica single mode fibers are normally not used for ultraviolet light or high-peak-power pulsed applications due to the high spatial power densities associated with these applications.
Posted Comments: | |
Mika C
 (posted 2024-01-22 11:17:55.75) Hello, I am looking for more detailed attenuation data as a function of wavelength for SM980-5.8-125. Specifically, I would like to know the attenuation of this fiber at 1092 nm. ksosnowski
 (posted 2024-01-25 12:56:29.0) Hello Mika, thanks for reaching out to Thorlabs. Based on some test data we've seen, the typical attenuation is close to 1dB/km around 1090nm. The transmission at this point is slightly better than the edge of performance which is = 2dB/km at 980nm. I have reached out directly to discuss your application further. roemee817
 (posted 2017-01-04 14:16:08.457) I have some questions about your product whose part number is SM980-5.8-125.
I will use 1550 nm fiber.
What is the maximum fiber input power available??
Thank you for reading me! tfrisch
 (posted 2017-01-04 09:02:46.0) Hello, thank you for contacting Thorlabs. The max power that can be coupled into a fiber depends on several factors including termination and the quality of the beam coupled. 300mW is a good rule of thumb for any fiber connector that may have an adhesive. For a bare cleaved fiber and a beam that is aligned with high coupling efficiency, a few watts should be achievable. Be sure coupling efficiency is high before power is increased. I will reach out to you directly about the details of what goes into that. bnewell
 (posted 2016-10-28 09:59:43.15) Hello, we use HI1060-100 optical fiber. We currently use a heated stripper, but we would like to understand if there are alternative methods that offer less risk of fiber damage. Would you be able to recommend any? Thank you. tfrisch
 (posted 2016-10-31 05:49:39.0) Hello, thank you for contacting Thorlabs. I have reached out to you directly about your applications. |

Stock Patch Cables Available with These Fibers | ||
---|---|---|
SMF-28 Ultra Fiber |
1550BHP Fiber |
Custom cables are also available. Click here for details.
Features
- Shipped from Stock
- No Minimums
- Most Fibers have Acrylate Coatings
- SM1550P has Polyimide Coating for High-Temperature Performance in the Telecom Region
- SMF-28-100, SMF-28-1000, and SMF-28-J9 have Ø900 µm Tight-Buffer Hytrel Outer Jackets
- CCC1310-J9 has a Ø900 µm Tight-Buffer PVC Outer Jacket
- Exceptional Core/Clad Concentricity Specifications
- 1550BHP Offers Tight Second Mode Cut-off Tolerances
- SM1250G80, CCC1310-J9, and SM1500G80 Offer Enhanced Bend Insensitivity (See the Specs Tab for Information)
- DCF4 Fiber Features Low Negative Dispersion (See the Full Web Presentation for Details)
Item # | Operating Wavelength | Mode Field Diameter | Cladding | Coating | Cut-Off Wavelength |
---|---|---|---|---|---|
SMF-28-J9 | 1260 - 1625 nm | 9.2 ± 0.4 µm @ 1310 nm 10.4 ± 0.5 µm @ 1550 nm |
125 ± 0.7 µm | 242 ± 5 µm | <1260 nm |
CCC1310-J9 | 1260 - 1625 nm | 8.6 ± 0.4 µm @ 1310 nm 9.7 ± 0.5 µm @ 1550 nm |
125 ± 0.7 µm | 242 ± 5 µm | ≤1260 nm |
1310BHP | 1300 - 1625 nm | 8.6 ± 0.5 µm @ 1310 nm 9.7 ± 0.5 µm @ 1550 nm |
125 ± 1.0 µm | 245 ± 15 µm | 1260 ± 30 nm |
SM1550P | 1310 - 1550 nm | 9.0 µm @ 1310 nm | 125 +1 / -3 µm | 145 ± 5 µm | <1260 nm |
SM1250G80 | 1310 - 1550 nm | 8.2 - 9.9 µm @ 1310 nm | 80 ± 1 µm | 170 ± 10 µm | 1150 - 1250 nm |
1550BHP | 1460 - 1620 nm | 9.5 ± 0.5 µm @ 1550 nm | 125 ± 1.0 µm | 245 ± 15 µm | 1400 ± 50 nm |
SM1500G80 | 1520 - 1650 nm | 6.0 - 6.8 µm @ 1550 nm | 80 ± 1 µm | 170 ± 10 µm | 1350 - 1520 nm |
DCF4 | 1530 - 1565 nm | 8.85 - 9.60 µm @ 1550 nm | 125 ± 1.0 µm | 250 ± 5 µm | ≤1500 nm |
Item # | Short-Term Bend Radius | Long-Term Bend Radius | Attenuation (Max) | NA | Core Index | Cladding Index |
---|---|---|---|---|---|---|
SMF-28-J9 | - | - | ≤0.32 dB/km @ 1310 nm ≤0.18 dB/km @ 1550 nm |
0.14a | Proprietaryb | Proprietaryb |
CCC1310-J9 | - | - | ≤0.35 dB/km @ 1310 nm ≤0.20 dB/km @ 1550 nm |
0.14 | 1310 nm: 1.4670 1550 nm: 1.4677 |
- |
1310BHP | ≥6 mm | ≥13 mm | ≤0.5 dB/km @ 1310 nm & 1550 nm | 0.13 | Callc | Callc |
SM1550P | ≥13 mm | ≥25 mm | <0.7 dB/kmd | 0.12 ± 0.02 | Proprietaryb | Proprietaryb |
SM1250G80 | ≥5 mm | ≥12 mm (or 38 mm for 25 Year Life) | ≤2 dB/km | 0.11 - 0.13 | 1310 nm: 1.45094e 1550 nm: 1.44813e |
1310 nm: 1.44680e 1550 nm: 1.44399e |
1550BHP | ≥6 mm | ≥13 mm | ≤0.5 dB/km @ 1550 nm | 0.13 | Callc | Callc |
SM1500G80 | ≥5 mm | ≥12 mm (or 38 mm for 25 Year Life) | ≤0.5 dB/km | 0.19 - 0.21 | 1550 nm: 1.45636f | 1550 nm: 1.44399f |
DCF4 | - | - | ≤0.210 dB/km @ 1550 nm | - | Proprietaryb | Proprietaryb |

Click to Enlarge
The left image shows the intensity profile of the beam propagated through the fiber overlaid on the fiber itself. The right image shows the standard intensity profile of the beam propagated through the fiber with the MFD and core diameter called out.
Definition of the Mode Field Diameter
The mode field diameter (MFD) is one measure of the beam width of light propagating in a single mode fiber. It is a function of wavelength, core radius, and the refractive indices of the core and cladding. While much of the light in an optical fiber is trapped within the fiber core, a small fraction propagates in the cladding. The light can be approximated as a Gaussian power distribution as shown to the right, where the MFD is the diameter at which the optical power is reduced to 1/e2 from its peak level.
Measurement of MFD
The measurement of MFD is accomplished by the Variable Aperture Method in the Far Field (VAMFF). An aperture is placed in the far field of the fiber output, and the intensity is measured. As successively smaller apertures are placed in the beam, the intensity levels are measured for each aperture; the data can then be plotted as power vs. the sine of the aperture half-angle (or the numerical aperture for an SM fiber).
The MFD is then determined using Petermann's second definition, which is a mathematical model that does not assume a specific shape of power distribution. The MFD in the near field can be determined from this far-field measurement using the Hankel Transform.
Quick Links |
---|
Damage at the Air / Glass Interface |
Intrinsic Damage Threshold |
Preparation and Handling of Optical Fibers |
Laser-Induced Damage in Silica Optical Fibers
The following tutorial details damage mechanisms relevant to unterminated (bare) fiber, terminated optical fiber, and other fiber components from laser light sources. These mechanisms include damage that occurs at the air / glass interface (when free-space coupling or when using connectors) and in the optical fiber itself. A fiber component, such as a bare fiber, patch cable, or fused coupler, may have multiple potential avenues for damage (e.g., connectors, fiber end faces, and the device itself). The maximum power that a fiber can handle will always be limited by the lowest limit of any of these damage mechanisms.
While the damage threshold can be estimated using scaling relations and general rules, absolute damage thresholds in optical fibers are very application dependent and user specific. Users can use this guide to estimate a safe power level that minimizes the risk of damage. Following all appropriate preparation and handling guidelines, users should be able to operate a fiber component up to the specified maximum power level; if no maximum is specified for a component, users should abide by the "practical safe level" described below for safe operation of the component. Factors that can reduce power handling and cause damage to a fiber component include, but are not limited to, misalignment during fiber coupling, contamination of the fiber end face, or imperfections in the fiber itself. For further discussion about an optical fiber’s power handling abilities for a specific application, please contact Thorlabs’ Tech Support.

Click to Enlarge
Undamaged Fiber End

Click to Enlarge
Damaged Fiber End
Damage at the Air / Glass Interface
There are several potential damage mechanisms that can occur at the air / glass interface. Light is incident on this interface when free-space coupling or when two fibers are mated using optical connectors. High-intensity light can damage the end face leading to reduced power handling and permanent damage to the fiber. For fibers terminated with optical connectors where the connectors are fixed to the fiber ends using epoxy, the heat generated by high-intensity light can burn the epoxy and leave residues on the fiber facet directly in the beam path.
Estimated Optical Power Densities on Air / Glass Interfacea | ||
---|---|---|
Type | Theoretical Damage Thresholdb | Practical Safe Levelc |
CW (Average Power) |
~1 MW/cm2 | ~250 kW/cm2 |
10 ns Pulsed (Peak Power) |
~5 GW/cm2 | ~1 GW/cm2 |
Damage Mechanisms on the Bare Fiber End Face
Damage mechanisms on a fiber end face can be modeled similarly to bulk optics, and industry-standard damage thresholds for UV Fused Silica substrates can be applied to silica-based fiber. However, unlike bulk optics, the relevant surface areas and beam diameters involved at the air / glass interface of an optical fiber are very small, particularly for coupling into single mode (SM) fiber. therefore, for a given power density, the power incident on the fiber needs to be lower for a smaller beam diameter.
The table to the right lists two thresholds for optical power densities: a theoretical damage threshold and a "practical safe level". In general, the theoretical damage threshold represents the estimated maximum power density that can be incident on the fiber end face without risking damage with very good fiber end face and coupling conditions. The "practical safe level" power density represents minimal risk of fiber damage. Operating a fiber or component beyond the practical safe level is possible, but users must follow the appropriate handling instructions and verify performance at low powers prior to use.
Calculating the Effective Area for Single Mode Fibers
The effective area for single mode (SM) fiber is defined by the mode field diameter (MFD), which is the cross-sectional area through which light propagates in the fiber; this area includes the fiber core and also a portion of the cladding. To achieve good efficiency when coupling into a single mode fiber, the diameter of the input beam must match the MFD of the fiber.
As an example, SM400 single mode fiber has a mode field diameter (MFD) of ~Ø3 µm operating at 400 nm, while the MFD for SMF-28 Ultra single mode fiber operating at 1550 nm is Ø10.5 µm. The effective area for these fibers can be calculated as follows:
SM400 Fiber: Area = Pi x (MFD/2)2 = Pi x (1.5 µm)2 = 7.07 µm2 = 7.07 x 10-8 cm2
SMF-28 Ultra Fiber: Area = Pi x (MFD/2)2 = Pi x (5.25 µm)2 = 86.6 µm2 = 8.66 x 10-7 cm2
To estimate the power level that a fiber facet can handle, the power density is multiplied by the effective area. Please note that this calculation assumes a uniform intensity profile, but most laser beams exhibit a Gaussian-like shape within single mode fiber, resulting in a higher power density at the center of the beam compared to the edges. Therefore, these calculations will slightly overestimate the power corresponding to the damage threshold or the practical safe level. Using the estimated power densities assuming a CW light source, we can determine the corresponding power levels as:
SM400 Fiber: 7.07 x 10-8 cm2 x 1 MW/cm2 = 7.1 x 10-8 MW = 71 mW (Theoretical Damage Threshold)
7.07 x 10-8 cm2 x 250 kW/cm2 = 1.8 x 10-5 kW = 18 mW (Practical Safe Level)
SMF-28 Ultra Fiber: 8.66 x 10-7 cm2 x 1 MW/cm2 = 8.7 x 10-7 MW = 870 mW (Theoretical Damage Threshold)
8.66 x 10-7 cm2 x 250 kW/cm2 = 2.1 x 10-4 kW = 210 mW (Practical Safe Level)
Effective Area of Multimode Fibers
The effective area of a multimode (MM) fiber is defined by the core diameter, which is typically far larger than the MFD of an SM fiber. For optimal coupling, Thorlabs recommends focusing a beam to a spot roughly 70 - 80% of the core diameter. The larger effective area of MM fibers lowers the power density on the fiber end face, allowing higher optical powers (typically on the order of kilowatts) to be coupled into multimode fiber without damage.
Damage Mechanisms Related to Ferrule / Connector Termination

Plot showing approximate input power that can be incident on a single mode silica optical fiber with a termination. Each line shows the estimated power level due to a specific damage mechanism. The maximum power handling is limited by the lowest power level from all relevant damage mechanisms (indicated by a solid line).
Fibers terminated with optical connectors have additional power handling considerations. Fiber is typically terminated using epoxy to bond the fiber to a ceramic or steel ferrule. When light is coupled into the fiber through a connector, light that does not enter the core and propagate down the fiber is scattered into the outer layers of the fiber, into the ferrule, and the epoxy used to hold the fiber in the ferrule. If the light is intense enough, it can burn the epoxy, causing it to vaporize and deposit a residue on the face of the connector. This results in localized absorption sites on the fiber end face that reduce coupling efficiency and increase scattering, causing further damage.
For several reasons, epoxy-related damage is dependent on the wavelength. In general, light scatters more strongly at short wavelengths than at longer wavelengths. Misalignment when coupling is also more likely due to the small MFD of short-wavelength SM fiber that also produces more scattered light.
To minimize the risk of burning the epoxy, fiber connectors can be constructed to have an epoxy-free air gap between the optical fiber and ferrule near the fiber end face. Our high-power multimode fiber patch cables use connectors with this design feature.
Determining Power Handling with Multiple Damage Mechanisms
When fiber cables or components have multiple avenues for damage (e.g., fiber patch cables), the maximum power handling is always limited by the lowest damage threshold that is relevant to the fiber component. In general, this represents the highest input power that can be incident on the patch cable end face and not the coupled output power.
As an illustrative example, the graph to the right shows an estimate of the power handling limitations of a single mode fiber patch cable due to damage to the fiber end face and damage via an optical connector. The total input power handling of a terminated fiber at a given wavelength is limited by the lower of the two limitations at any given wavelength (indicated by the solid lines). A single mode fiber operating at around 488 nm is primarily limited by damage to the fiber end face (blue solid line), but fibers operating at 1550 nm are limited by damage to the optical connector (red solid line).
In the case of a multimode fiber, the effective mode area is defined by the core diameter, which is larger than the effective mode area for SM fiber. This results in a lower power density on the fiber end face and allows higher optical powers (on the order of kilowatts) to be coupled into the fiber without damage (not shown in graph). However, the damage limit of the ferrule / connector termination remains unchanged and as a result, the maximum power handling for a multimode fiber is limited by the ferrule and connector termination.
Please note that these are rough estimates of power levels where damage is very unlikely with proper handling and alignment procedures. It is worth noting that optical fibers are frequently used at power levels above those described here. However, these applications typically require expert users and testing at lower powers first to minimize risk of damage. Even still, optical fiber components should be considered a consumable lab supply if used at high power levels.
Intrinsic Damage Threshold
In addition to damage mechanisms at the air / glass interface, optical fibers also display power handling limitations due to damage mechanisms within the optical fiber itself. These limitations will affect all fiber components as they are intrinsic to the fiber itself. Two categories of damage within the fiber are damage from bend losses and damage from photodarkening.
Bend Losses
Bend losses occur when a fiber is bent to a point where light traveling in the core is incident on the core/cladding interface at an angle higher than the critical angle, making total internal reflection impossible. Under these circumstances, light escapes the fiber, often in a localized area. The light escaping the fiber typically has a high power density, which burns the fiber coating as well as any surrounding furcation tubing.
A special category of optical fiber, called double-clad fiber, can reduce the risk of bend-loss damage by allowing the fiber’s cladding (2nd layer) to also function as a waveguide in addition to the core. By making the critical angle of the cladding/coating interface higher than the critical angle of the core/clad interface, light that escapes the core is loosely confined within the cladding. It will then leak out over a distance of centimeters or meters instead of at one localized spot within the fiber, minimizing the risk of damage. Thorlabs manufactures and sells 0.22 NA double-clad multimode fiber, which boasts very high, megawatt range power handling.
Photodarkening
A second damage mechanism, called photodarkening or solarization, can occur in fibers used with ultraviolet or short-wavelength visible light, particularly those with germanium-doped cores. Fibers used at these wavelengths will experience increased attenuation over time. The mechanism that causes photodarkening is largely unknown, but several fiber designs have been developed to mitigate it. For example, fibers with a very low hydroxyl ion (OH) content have been found to resist photodarkening and using other dopants, such as fluorine, can also reduce photodarkening.
Even with the above strategies in place, all fibers eventually experience photodarkening when used with UV or short-wavelength light, and thus, fibers used at these wavelengths should be considered consumables.
Preparation and Handling of Optical Fibers
General Cleaning and Operation Guidelines
These general cleaning and operation guidelines are recommended for all fiber optic products. Users should still follow specific guidelines for an individual product as outlined in the support documentation or manual. Damage threshold calculations only apply when all appropriate cleaning and handling procedures are followed.
-
All light sources should be turned off prior to installing or integrating optical fibers (terminated or bare). This ensures that focused beams of light are not incident on fragile parts of the connector or fiber, which can possibly cause damage.
-
The power-handling capability of an optical fiber is directly linked to the quality of the fiber/connector end face. Always inspect the fiber end prior to connecting the fiber to an optical system. The fiber end face should be clean and clear of dirt and other contaminants that can cause scattering of coupled light. Bare fiber should be cleaved prior to use and users should inspect the fiber end to ensure a good quality cleave is achieved.
-
If an optical fiber is to be spliced into the optical system, users should first verify that the splice is of good quality at a low optical power prior to high-power use. Poor splice quality may increase light scattering at the splice interface, which can be a source of fiber damage.
-
Users should use low power when aligning the system and optimizing coupling; this minimizes exposure of other parts of the fiber (other than the core) to light. Damage from scattered light can occur if a high power beam is focused on the cladding, coating, or connector.
Tips for Using Fiber at Higher Optical Power
Optical fibers and fiber components should generally be operated within safe power level limits, but under ideal conditions (very good optical alignment and very clean optical end faces), the power handling of a fiber component may be increased. Users must verify the performance and stability of a fiber component within their system prior to increasing input or output power and follow all necessary safety and operation instructions. The tips below are useful suggestions when considering increasing optical power in an optical fiber or component.
-
Splicing a fiber component into a system using a fiber splicer can increase power handling as it minimizes possibility of air/fiber interface damage. Users should follow all appropriate guidelines to prepare and make a high-quality fiber splice. Poor splices can lead to scattering or regions of highly localized heat at the splice interface that can damage the fiber.
-
After connecting the fiber or component, the system should be tested and aligned using a light source at low power. The system power can be ramped up slowly to the desired output power while periodically verifying all components are properly aligned and that coupling efficiency is not changing with respect to optical launch power.
-
Bend losses that result from sharply bending a fiber can cause light to leak from the fiber in the stressed area. When operating at high power, the localized heating that can occur when a large amount of light escapes a small localized area (the stressed region) can damage the fiber. Avoid disturbing or accidently bending fibers during operation to minimize bend losses.
-
Users should always choose the appropriate optical fiber for a given application. For example, large-mode-area fibers are a good alternative to standard single mode fibers in high-power applications as they provide good beam quality with a larger MFD, decreasing the power density on the air/fiber interface.
-
Step-index silica single mode fibers are normally not used for ultraviolet light or high-peak-power pulsed applications due to the high spatial power densities associated with these applications.
Posted Comments: | |
Sudipta Nayak
 (posted 2023-07-31 16:21:34.15) hello
would it be possible to get pigtailed sinlge mode fibers with very small core diameters?
Sudipta jpolaris
 (posted 2023-08-01 06:29:05.0) Thank you for contacting Thorlabs. Our single-mode fibers come in a variety of different core sizes. I have reached out to you directly to discuss what is needed for your application. |

Features
- SM Fiber for 1850 - 2200 nm
- Shipped from Stock
- No Minimums
- Ge-Doped Silica Core, Pure Silica Cladding, and a UV Cured Acrylate Coating
- Exceptional Core/Clad Concentricity Specifications
- Low Bend Losses (See Specs Tab)
Item # | Operating Wavelength | MFD | Core Diameter | Cladding Diameter | Coating Diameter | Cut-Off Wavelength |
---|---|---|---|---|---|---|
SM1950 | 1850 - 2200 nm | 8.0 µm @ 1950 nm | 7 µm | 125 ± 1 µm | 245 ± 10 µm | 1720 ± 80 nm |
Item # | Coating Concentricity | Core-Clad Concentricity | Typical Attenuation | NA | Core Index | Cladding Index |
---|---|---|---|---|---|---|
SM1950 | <5 µm | <0.5 µm | 5 dB/km (0.005 dB/m) @ 1.9 µm | 0.20 | Calla | Calla |
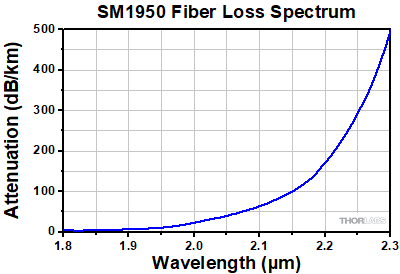
Click to Enlarge
Click for Raw Data
This plot contains the measured attenuation for SM1950 fiber across the single mode wavelength range (1850 nm - 2200 nm).

Click to Enlarge
Click for Raw Data
This plot contains the measured attenuation for a single loop of SM1950 fiber at nine different bend radii. The shaded region in the plot denotes the single mode wavelength range (1.85 - 2.2 µm).

Click to Enlarge
The left image shows the intensity profile of the beam propagated through the fiber overlaid on the fiber itself. The right image shows the standard intensity profile of the beam propagated through the fiber with the MFD and core diameter called out.
Definition of the Mode Field Diameter
The mode field diameter (MFD) is one measure of the beam width of light propagating in a single mode fiber. It is a function of wavelength, core radius, and the refractive indices of the core and cladding. While much of the light in an optical fiber is trapped within the fiber core, a small fraction propagates in the cladding. The light can be approximated as a Gaussian power distribution as shown to the right, where the MFD is the diameter at which the optical power is reduced to 1/e2 from its peak level.
Measurement of MFD
The measurement of MFD is accomplished by the Variable Aperture Method in the Far Field (VAMFF). An aperture is placed in the far field of the fiber output, and the intensity is measured. As successively smaller apertures are placed in the beam, the intensity levels are measured for each aperture; the data can then be plotted as power vs. the sine of the aperture half-angle (or the numerical aperture for an SM fiber).
The MFD is then determined using Petermann's second definition, which is a mathematical model that does not assume a specific shape of power distribution. The MFD in the near field can be determined from this far-field measurement using the Hankel Transform.
Quick Links |
---|
Damage at the Air / Glass Interface |
Intrinsic Damage Threshold |
Preparation and Handling of Optical Fibers |
Laser-Induced Damage in Silica Optical Fibers
The following tutorial details damage mechanisms relevant to unterminated (bare) fiber, terminated optical fiber, and other fiber components from laser light sources. These mechanisms include damage that occurs at the air / glass interface (when free-space coupling or when using connectors) and in the optical fiber itself. A fiber component, such as a bare fiber, patch cable, or fused coupler, may have multiple potential avenues for damage (e.g., connectors, fiber end faces, and the device itself). The maximum power that a fiber can handle will always be limited by the lowest limit of any of these damage mechanisms.
While the damage threshold can be estimated using scaling relations and general rules, absolute damage thresholds in optical fibers are very application dependent and user specific. Users can use this guide to estimate a safe power level that minimizes the risk of damage. Following all appropriate preparation and handling guidelines, users should be able to operate a fiber component up to the specified maximum power level; if no maximum is specified for a component, users should abide by the "practical safe level" described below for safe operation of the component. Factors that can reduce power handling and cause damage to a fiber component include, but are not limited to, misalignment during fiber coupling, contamination of the fiber end face, or imperfections in the fiber itself. For further discussion about an optical fiber’s power handling abilities for a specific application, please contact Thorlabs’ Tech Support.

Click to Enlarge
Undamaged Fiber End

Click to Enlarge
Damaged Fiber End
Damage at the Air / Glass Interface
There are several potential damage mechanisms that can occur at the air / glass interface. Light is incident on this interface when free-space coupling or when two fibers are mated using optical connectors. High-intensity light can damage the end face leading to reduced power handling and permanent damage to the fiber. For fibers terminated with optical connectors where the connectors are fixed to the fiber ends using epoxy, the heat generated by high-intensity light can burn the epoxy and leave residues on the fiber facet directly in the beam path.
Estimated Optical Power Densities on Air / Glass Interfacea | ||
---|---|---|
Type | Theoretical Damage Thresholdb | Practical Safe Levelc |
CW (Average Power) |
~1 MW/cm2 | ~250 kW/cm2 |
10 ns Pulsed (Peak Power) |
~5 GW/cm2 | ~1 GW/cm2 |
Damage Mechanisms on the Bare Fiber End Face
Damage mechanisms on a fiber end face can be modeled similarly to bulk optics, and industry-standard damage thresholds for UV Fused Silica substrates can be applied to silica-based fiber. However, unlike bulk optics, the relevant surface areas and beam diameters involved at the air / glass interface of an optical fiber are very small, particularly for coupling into single mode (SM) fiber. therefore, for a given power density, the power incident on the fiber needs to be lower for a smaller beam diameter.
The table to the right lists two thresholds for optical power densities: a theoretical damage threshold and a "practical safe level". In general, the theoretical damage threshold represents the estimated maximum power density that can be incident on the fiber end face without risking damage with very good fiber end face and coupling conditions. The "practical safe level" power density represents minimal risk of fiber damage. Operating a fiber or component beyond the practical safe level is possible, but users must follow the appropriate handling instructions and verify performance at low powers prior to use.
Calculating the Effective Area for Single Mode Fibers
The effective area for single mode (SM) fiber is defined by the mode field diameter (MFD), which is the cross-sectional area through which light propagates in the fiber; this area includes the fiber core and also a portion of the cladding. To achieve good efficiency when coupling into a single mode fiber, the diameter of the input beam must match the MFD of the fiber.
As an example, SM400 single mode fiber has a mode field diameter (MFD) of ~Ø3 µm operating at 400 nm, while the MFD for SMF-28 Ultra single mode fiber operating at 1550 nm is Ø10.5 µm. The effective area for these fibers can be calculated as follows:
SM400 Fiber: Area = Pi x (MFD/2)2 = Pi x (1.5 µm)2 = 7.07 µm2 = 7.07 x 10-8 cm2
SMF-28 Ultra Fiber: Area = Pi x (MFD/2)2 = Pi x (5.25 µm)2 = 86.6 µm2 = 8.66 x 10-7 cm2
To estimate the power level that a fiber facet can handle, the power density is multiplied by the effective area. Please note that this calculation assumes a uniform intensity profile, but most laser beams exhibit a Gaussian-like shape within single mode fiber, resulting in a higher power density at the center of the beam compared to the edges. Therefore, these calculations will slightly overestimate the power corresponding to the damage threshold or the practical safe level. Using the estimated power densities assuming a CW light source, we can determine the corresponding power levels as:
SM400 Fiber: 7.07 x 10-8 cm2 x 1 MW/cm2 = 7.1 x 10-8 MW = 71 mW (Theoretical Damage Threshold)
7.07 x 10-8 cm2 x 250 kW/cm2 = 1.8 x 10-5 kW = 18 mW (Practical Safe Level)
SMF-28 Ultra Fiber: 8.66 x 10-7 cm2 x 1 MW/cm2 = 8.7 x 10-7 MW = 870 mW (Theoretical Damage Threshold)
8.66 x 10-7 cm2 x 250 kW/cm2 = 2.1 x 10-4 kW = 210 mW (Practical Safe Level)
Effective Area of Multimode Fibers
The effective area of a multimode (MM) fiber is defined by the core diameter, which is typically far larger than the MFD of an SM fiber. For optimal coupling, Thorlabs recommends focusing a beam to a spot roughly 70 - 80% of the core diameter. The larger effective area of MM fibers lowers the power density on the fiber end face, allowing higher optical powers (typically on the order of kilowatts) to be coupled into multimode fiber without damage.
Damage Mechanisms Related to Ferrule / Connector Termination

Plot showing approximate input power that can be incident on a single mode silica optical fiber with a termination. Each line shows the estimated power level due to a specific damage mechanism. The maximum power handling is limited by the lowest power level from all relevant damage mechanisms (indicated by a solid line).
Fibers terminated with optical connectors have additional power handling considerations. Fiber is typically terminated using epoxy to bond the fiber to a ceramic or steel ferrule. When light is coupled into the fiber through a connector, light that does not enter the core and propagate down the fiber is scattered into the outer layers of the fiber, into the ferrule, and the epoxy used to hold the fiber in the ferrule. If the light is intense enough, it can burn the epoxy, causing it to vaporize and deposit a residue on the face of the connector. This results in localized absorption sites on the fiber end face that reduce coupling efficiency and increase scattering, causing further damage.
For several reasons, epoxy-related damage is dependent on the wavelength. In general, light scatters more strongly at short wavelengths than at longer wavelengths. Misalignment when coupling is also more likely due to the small MFD of short-wavelength SM fiber that also produces more scattered light.
To minimize the risk of burning the epoxy, fiber connectors can be constructed to have an epoxy-free air gap between the optical fiber and ferrule near the fiber end face. Our high-power multimode fiber patch cables use connectors with this design feature.
Determining Power Handling with Multiple Damage Mechanisms
When fiber cables or components have multiple avenues for damage (e.g., fiber patch cables), the maximum power handling is always limited by the lowest damage threshold that is relevant to the fiber component. In general, this represents the highest input power that can be incident on the patch cable end face and not the coupled output power.
As an illustrative example, the graph to the right shows an estimate of the power handling limitations of a single mode fiber patch cable due to damage to the fiber end face and damage via an optical connector. The total input power handling of a terminated fiber at a given wavelength is limited by the lower of the two limitations at any given wavelength (indicated by the solid lines). A single mode fiber operating at around 488 nm is primarily limited by damage to the fiber end face (blue solid line), but fibers operating at 1550 nm are limited by damage to the optical connector (red solid line).
In the case of a multimode fiber, the effective mode area is defined by the core diameter, which is larger than the effective mode area for SM fiber. This results in a lower power density on the fiber end face and allows higher optical powers (on the order of kilowatts) to be coupled into the fiber without damage (not shown in graph). However, the damage limit of the ferrule / connector termination remains unchanged and as a result, the maximum power handling for a multimode fiber is limited by the ferrule and connector termination.
Please note that these are rough estimates of power levels where damage is very unlikely with proper handling and alignment procedures. It is worth noting that optical fibers are frequently used at power levels above those described here. However, these applications typically require expert users and testing at lower powers first to minimize risk of damage. Even still, optical fiber components should be considered a consumable lab supply if used at high power levels.
Intrinsic Damage Threshold
In addition to damage mechanisms at the air / glass interface, optical fibers also display power handling limitations due to damage mechanisms within the optical fiber itself. These limitations will affect all fiber components as they are intrinsic to the fiber itself. Two categories of damage within the fiber are damage from bend losses and damage from photodarkening.
Bend Losses
Bend losses occur when a fiber is bent to a point where light traveling in the core is incident on the core/cladding interface at an angle higher than the critical angle, making total internal reflection impossible. Under these circumstances, light escapes the fiber, often in a localized area. The light escaping the fiber typically has a high power density, which burns the fiber coating as well as any surrounding furcation tubing.
A special category of optical fiber, called double-clad fiber, can reduce the risk of bend-loss damage by allowing the fiber’s cladding (2nd layer) to also function as a waveguide in addition to the core. By making the critical angle of the cladding/coating interface higher than the critical angle of the core/clad interface, light that escapes the core is loosely confined within the cladding. It will then leak out over a distance of centimeters or meters instead of at one localized spot within the fiber, minimizing the risk of damage. Thorlabs manufactures and sells 0.22 NA double-clad multimode fiber, which boasts very high, megawatt range power handling.
Photodarkening
A second damage mechanism, called photodarkening or solarization, can occur in fibers used with ultraviolet or short-wavelength visible light, particularly those with germanium-doped cores. Fibers used at these wavelengths will experience increased attenuation over time. The mechanism that causes photodarkening is largely unknown, but several fiber designs have been developed to mitigate it. For example, fibers with a very low hydroxyl ion (OH) content have been found to resist photodarkening and using other dopants, such as fluorine, can also reduce photodarkening.
Even with the above strategies in place, all fibers eventually experience photodarkening when used with UV or short-wavelength light, and thus, fibers used at these wavelengths should be considered consumables.
Preparation and Handling of Optical Fibers
General Cleaning and Operation Guidelines
These general cleaning and operation guidelines are recommended for all fiber optic products. Users should still follow specific guidelines for an individual product as outlined in the support documentation or manual. Damage threshold calculations only apply when all appropriate cleaning and handling procedures are followed.
-
All light sources should be turned off prior to installing or integrating optical fibers (terminated or bare). This ensures that focused beams of light are not incident on fragile parts of the connector or fiber, which can possibly cause damage.
-
The power-handling capability of an optical fiber is directly linked to the quality of the fiber/connector end face. Always inspect the fiber end prior to connecting the fiber to an optical system. The fiber end face should be clean and clear of dirt and other contaminants that can cause scattering of coupled light. Bare fiber should be cleaved prior to use and users should inspect the fiber end to ensure a good quality cleave is achieved.
-
If an optical fiber is to be spliced into the optical system, users should first verify that the splice is of good quality at a low optical power prior to high-power use. Poor splice quality may increase light scattering at the splice interface, which can be a source of fiber damage.
-
Users should use low power when aligning the system and optimizing coupling; this minimizes exposure of other parts of the fiber (other than the core) to light. Damage from scattered light can occur if a high power beam is focused on the cladding, coating, or connector.
Tips for Using Fiber at Higher Optical Power
Optical fibers and fiber components should generally be operated within safe power level limits, but under ideal conditions (very good optical alignment and very clean optical end faces), the power handling of a fiber component may be increased. Users must verify the performance and stability of a fiber component within their system prior to increasing input or output power and follow all necessary safety and operation instructions. The tips below are useful suggestions when considering increasing optical power in an optical fiber or component.
-
Splicing a fiber component into a system using a fiber splicer can increase power handling as it minimizes possibility of air/fiber interface damage. Users should follow all appropriate guidelines to prepare and make a high-quality fiber splice. Poor splices can lead to scattering or regions of highly localized heat at the splice interface that can damage the fiber.
-
After connecting the fiber or component, the system should be tested and aligned using a light source at low power. The system power can be ramped up slowly to the desired output power while periodically verifying all components are properly aligned and that coupling efficiency is not changing with respect to optical launch power.
-
Bend losses that result from sharply bending a fiber can cause light to leak from the fiber in the stressed area. When operating at high power, the localized heating that can occur when a large amount of light escapes a small localized area (the stressed region) can damage the fiber. Avoid disturbing or accidently bending fibers during operation to minimize bend losses.
-
Users should always choose the appropriate optical fiber for a given application. For example, large-mode-area fibers are a good alternative to standard single mode fibers in high-power applications as they provide good beam quality with a larger MFD, decreasing the power density on the air/fiber interface.
-
Step-index silica single mode fibers are normally not used for ultraviolet light or high-peak-power pulsed applications due to the high spatial power densities associated with these applications.
Posted Comments: | |
No Comments Posted |