2" (50 mm) Motorized Actuators
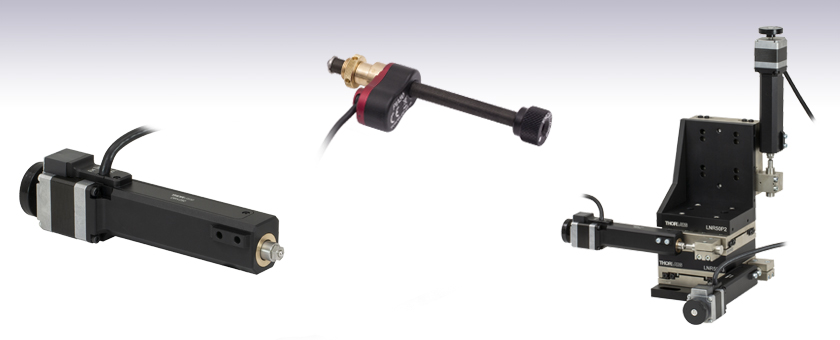
- Piezo Inertia or Stepper Actuators with 50 mm of Travel
- High Load Capacities
- No Backlash
Application Idea
Three LNR50DD Stages
in XYZ Configuration
with DRV250 Motors
DRV250
50 mm Travel
Stepper Motor Actuator
PIA50
50 mm Travel
Piezo Inertia Actuator

Please Wait

Recommended Controllers
BSC201, BSC202, or BSC203
- 409,600 Microsteps per Revolution
- 48 V Output at 25 W
- Trapezoidal and
'S-Curve' Velocity Profiles
Features
- Designed for Use with LNR50 TravelMax™ Stages
- ±1.6 µm Unidirectional Repeatability
- Maximum Pushing Force: 180 N
- Preload to Eliminate Backlash
- Non-Rotating Tip
- 25 mm Travel Version also Available
Key Specificationsa | |
---|---|
Travel Range | 50 mm (1.97") |
Unidirectional Repeatability | ±1.6 µm |
Bidirectional Repeatability | ±3.9 µm |
Maximum Pushing Forceb | 180 N |
Maximum Velocity | 50 mm/s |
Maximum Acceleration | 50 mm/s2 |
Limit Switches | Hall Effect |
Homing Repeatability | ±3.6 µm |
Feedback | Nonec |
Motor Type | 2-Phase Stepper Motor |
Full Step Angle | 1.8° |
Lead Screw Pitch | 1.0 mm |
Microsteps per Revolution | 409 600 |
Actuator Mass | 0.66 kg |
Compatible Controllersd | BSC201, BSC202, BSC203, or MST602 |
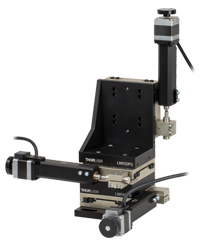
Click to Enlarge
A 3-axis LNR50DD 2" travel stage shown with the manual adjusters replaced by DRV250 actuators.
The DRV250 offers 50 mm (1.97") of travel and a unidirectional repeatability of ±1.6 μm. When used with one of our stepper motor controllers, the DRV250 achieves a theoretical minimum step size of 2.4 nm and a maximum speed of 50 mm/s.
The hybrid stepper motor, with its rotor that consists of 50 individual magnetic teeth, is ideally suited for micro-stepping applications. Aside from the increase in resolution resulting from increasing the steps per revolution from 200 to 409 600, micro-stepping also ensures smoother low-speed motion by allowing the discrete 1.8° step size to be reduced to much smaller steps, resulting in lower vibrational noise.
The DRV250 stepper motor drive is equipped with a trapezoidal screw thread for more efficient high-load operation than is available from a standard threading.
This actuator is designed for use with our 2" TravelMax Manual Stages. To use the DRV250 with these stages, mount the motor to the side of the stage using two 40 mm long M4 cap screws (included). In order to secure the TravelMax stage to a table while using the DRV250 actuator, the LNR50P4(/M) base plate is required.
A 500 mm (19.7") cable with a 15-pin D-type connector is attached to the unit to connect the stepper motor to a controller. The unit also comes with a 3 m (9.8 ft) extension cable (item # PAA613). If a shorter cable is needed, the 1 m (3.3 ft) PAA612 cable is available separately.
Pin Diagram
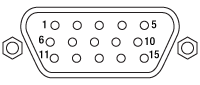
High-Density D-Type Male 15 Pin Connector
15-Pin D-Sub Connector Pin Out
Pin | Description | Pin | Description |
---|---|---|---|
1 | Limit Grounda | 9 | Ident (for Future Use) |
2 | CCW Limit Switch | 10 | +5 V |
3 | CW Limit Switch | 11 | Reserved for Future Use |
4 | Motor Phase B - | 12 | Reserved for Future Use |
5 | Motor Phase B + | 13 | +5 V |
6 | Motor Phase A - | 14 | Reserved for Future Use |
7 | Motor Phase A + | 15 | Ground |
8 | Reserved for Future Use | - | - |
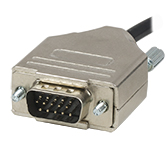
Click to Enlarge
High-Density D-Type Male 15 Pin Connector
Posted Comments: | |
Peter Hogg
 (posted 2021-08-27 13:23:46.94) I'm a graduate student who is trying to build a custom stage with a controller and parts I already have in the lab. I was wondering the compatibility of this actuator (DRV250) with a controller I already have (Sutter MP 285). I have the pin-out for the Sutter's driver and I am comfortable with creating custom wiring but want to make sure I of compatibility before purchasing anything. cwright
 (posted 2021-09-02 09:25:24.0) Response from Charles at Thorlabs: Thank you for your query. Unfortunately we are not able to support the use of third party controllers with our actuators and would recommend the use of BSC201 with the DRV250. wmwu
 (posted 2016-02-29 19:00:04.997) Dear Officer,
Is "Stepper Motor Drive (DRV014)" able to connect to the "Translation Stage(PT1A)", and to control its motion?
Thanks very much.
Best regards, Alan bwood
 (posted 2016-03-01 04:06:43.0) Response from Ben at Thorlabs: Thank you for your feedback. Unfortunately, the DRV014 is not compatible with the PT1A. Among other reasons, the DRV014 barrel size is too large (Ø12 mm) for the PT1A (Ø9.5 mm). The recommended stage to pair with the DRV014 are the 50 mm TravelMax™ stages, and the recommended actuators for the PT1A can be found under the "Actuator" tab on the PT1 series web page. |

Required Controller:
KIM001 or KIM101
- KIM001: Single-Channel Output
- KIM101: Four Output Channels, Capable of Multi-Channel Operation
- Standalone Control via Top Panel or PC-Control via USB
- Voltage Output from 85 V to 125 V
Item #a | PIA50 | |||
---|---|---|---|---|
Travel | 50 mm (1.97") | |||
Typical Step Sizeb,c | 10 - 30 nm (Typ.), ≤30 nm (Max) | |||
Step Size Adjustabilityd | Up to 30% | |||
Max Step Frequency | 2 kHz | |||
Backlash | None | |||
Max Active Preloade | 25 N | |||
Recommended Max Axial Load Capacityf |
2.5 kg (5.5 lbs) | |||
Speed (Continuous Stepping)b,c |
1.2 - 3.6 mm/min (Typ.) ≤3.6 mm/min (Max) |
|||
Drive Screw | 1/4"-80 Thread, Hard PVD Coated | |||
Motor Type | Piezoelectric Inertia | |||
Mounting Feature | Ø3/8" (Ø9.525 mm) Barrel | |||
Operating Temperature | 10 to 40 °C (50 to 104 °F) | |||
Dimensions | 3.80" x 1.24" x 0.67” (96.6 mm x 31.5 mm x 17.0 mm) |
|||
Cable Length | 1.0 m (3.28') | |||
Connector | SMC, Female | |||
Required Controllerg | KIM001 or KIM101 |
Features
- Ø3/8" Mounting Barrel for Compatibility with Translation Stages
- Compact Design: 31.5 mm x 17.0 mm (W x H)
- Manual Adjustment via Knob on Adjuster Screw
- 125 V Maximum Operating Voltage
- Also Available in 13 mm and 25 mm Travel Versions
- Ideal for Set-and-Hold Applications that Require High-Resolution Relative Positioning
- Control Cable can be Adjusted up to 110° for Space-Constrained Applications
Thorlabs' PIA50 Piezoelectric Inertia Actuator provides high-resolution linear motion control with a long piezo-controlled translation range in a compact package. It can support loads up to 2.5 kg (5.51 lbs) and preloads up to 25 N with typical step size ranging from 10 nm to 30 nm and no backlash. The step size can be adjusted up to 30% to a maximum of approximately 30 nm using the KIM101 Controller and Kinesis® software. However, due to the open-loop design, piezo hysteresis, and application conditions such as the direction of travel, the achieved step size of the system can vary by up to 20% and is not normally repeatable. An external feedback system will need to be used to overcome this variance.
This actuator has a Ø3/8" (Ø9.525 mm) barrel that can be mounted in a manual stage that has a Ø3/8" mounting clamp. For compatibility with 1/4"-80 or 3/16"-100 threaded mirror mounts see our 10 mm travel piezo inertia actuators. The actuator is self-locking when at rest and when there is no power supplied to the piezo, making the actuator ideal for set-and-hold applications that require nanometer resolution and long-term alignment stability. Manual adjustments can be made using the knob on the adjuster screw, as long as the piezo is not actively translating the screw; the knob is also compatible with 5/64" (2.0 mm) hex keys.
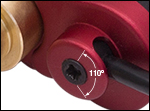
Click for Details
The control cable can be adjusted up to 110° for space-constrained applications.
Powered by a 10 mm long discrete piezo stack, the actuator can operate at speeds of up to 3.6 mm/min. The design of the piezo motor will rotate the tip of the lead screw during translation. For information on the design of our piezo inertia "slip-stick" motor actuators, please see the complete presentation here.
Required Controller
A K-Cube Piezo Inertia Controller is required to operate our PIA50 Piezo Inertia Actuator; the actuator cannot be operated using a standard piezo controller. The K-Cube controllers have an internal sawtooth voltage signal generator capable of sending sub-millisecond pulses (steps) with controllable amplitudes from 85 V to 125 V. In addition to a single-channel driver, we offer a four-channel driver capable of single- or dual-channel operation, which is ideal for applications involving multiple motorized actuators, such as beam steering.
For more information, please see the full web presentation.
Posted Comments: | |
No Comments Posted |

Required Controller:
KIM001 or KIM101
- KIM001: Single-Channel Output
- KIM101: Four Output Channels, Capable of Multi-Channel Operation
- Standalone Control via Top Panel or PC Control via USB
- Voltage Output from 85 V to 125 V
Item #a | PIA50VF |
---|---|
Travel | 50 mm (1.97") |
Step Sizeb,c | 10 - 30 nm (Typ.), ≤30 nm (Max) |
Step Size Adjustabilityd | ≤30% |
Max Step Frequency | 2 kHz |
Backlash | None |
Max Active Preloade | 25 N |
Recommended Max Axial Load Capacityf |
2.5 kg (5.5 lbs) |
Speed (Continuous Stepping)b,c |
1.2 - 3.6 mm/min (Typ.), ≤3.6 mm/min (Max) |
Drive Screw | 1/4"-80 Thread, Hard PVD Coated |
Motor Type | Piezoelectric Inertia |
Mounting Featureg (Auxiliary) |
Ø3/8" (Ø9.525 mm) Barrel (3/8"-40 Thread with Lock Nut) |
Vacuum Rating | 10-6 Torr |
Operating Temperature | 5 to 40 °C |
Max Bakeout Temperature | 130 °C |
Dimensions | 97.0 mm x 31.5 mm x 17.0 mm (3.82" x 1.24" x 0.67") |
Mass (Including Cable) | 65 g (2.29 oz) |
Cable Length | 0.75 m (2.46 ft) Flying Lead for Vacuum, 1.0 m (3.3 ft) Cored Cable for Wiring Outside Chamber |
Connector | SMC Female |
Required Controllerh | KIM001 or KIM101 |
Features
- Compact Design: 31.5 mm x 17.0 mm (W x H)
- Manual Adjustment via Knob on Adjuster Screw
- Rated Down to 10-6 Torr
- 125 V Maximum Operating Voltage
- Ø3/8" Mounting Barrel for Compatibility with Translation Stages
- Ideal for Set-and-Hold Applications that Require High-Resolution Relative Positioning
- Also Available in 13 mm and 25 mm Travel Versions
Thorlabs' PIA50VF Vacuum-Compatible Piezoelectric Inertia Actuator is rated down to 10-6 Torr operation and provides high-resolution linear motion control with a long piezo-controlled translation range in a compact, vacuum-compatible package. It can support loads up to 2.5 kg and preloads up to 25 N with typical movements of 20 nm and no backlash. The step size can be adjusted up to 30% to a maximum of approximately 30 nm using the KIM101 Controller and Kinesis® software. However, due to the open-loop design, piezo hysteresis, and application conditions such as the direction of travel, the achieved step size of the system can vary by up to 20% and is not normally repeatable. An external feedback system will need to be used to overcome this variance.
This actuator has a Ø3/8" (Ø9.525 mm) barrel that can be mounted in a manual stage that has a Ø3/8" mounting clamp. For compatibility with 1/4"-100 threaded mirror mounts see our 10 mm travel piezo inertia actuators. The actuator is self-locking when at rest and when there is no power supplied to the piezo, making the actuator ideal for set-and-hold applications that require nanometer resolution and long-term alignment stability. Manual adjustments can be made using the knob on the adjuster screw, as long as the piezo is not actively translating the screw; the knob is also compatible with 5/64" (2.0 mm) hex keys.
Each actuator has an integrated 0.75 m flying lead, plus 1.0 m of cored cable for wiring outside the vacuum chamber. The flying leads and cored cable lengths can be cut down as needed, but the total length (inside and outside) should not exceed 2.0 m. As shown in the image below, the flying lead for each actuator can be rotated up to 110° for space-constrained applications.
Powered by a 10 mm long discrete piezo stack, the actuator can operate at speeds of up to 3.6 mm/minute. The design of the piezo motor will rotate the tip of the lead screw during translation. For information on the design of this piezo inertia "slip-stick" motor actuator, please see the complete presentation here.
Required Controller
A KIM001 or KIM101 controller is required to operate our PIA13VF Piezo Inertia Actuator; the actuator cannot be operated using a standard piezo controller. These drivers have an internal sawtooth voltage signal generator capable of sending sub-millisecond pulses (steps) with controllable amplitudes from 85 V to 125 V. The KIM001 and KIM101 controllers offer one and four output channels, respectively.
For more information, please see the full web presentation.
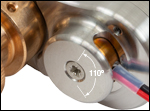
Click for Details
The flying lead can be adjusted up to 110° for space-constrained applications.
Posted Comments: | |
No Comments Posted |

Thorlabs' DRV, ZST, and ZFS Stepper Motor Actuators, as well as our Z9 DC Servo Motor Actuators, come with cables for connecting to the required controllers. Thorlabs also offers separate cables that may be used as extension cables.
Stepper Motor Cables
Thorlabs offers a variety of cables to support several stepper motor actuator and controller combinations. Supported stepper motors include our ZST, ZFS, and DRV actuators; supported controllers include our BSC benchtop controllers, our KST201 K-Cube™ Controller, and our MST602 Rack Control Module. In order to see which cable is compatible with a given combination of stepper motor and controller, please see the table below. The pin assignment for each cable is given in the Pin Diagrams tab. Please note that these cables cannot be used with motors and controllers that do not match their pin assignment, even if the connectors are the same.
DC Motor Cables
The PAA632 is a 2.5 m cable for our Z9 series of DC motor actuators. This cable is intended to be used with the KDC101 K-Cube DC Servo Motor Controller. The pin assignment for this cable is given in the Pin Diagrams tab. Although it uses a 15-pin connector, this cable is not compatible with any of our stepper motors.

![]() |
|
PAA612 and PAA613 Stepper Motor Cables
DA15 Male D-Type to DE15 Female D-Type
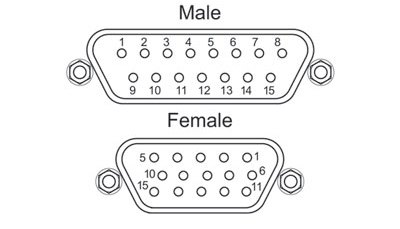
DA15 Male Pin | DE15 Female Pin | Description |
---|---|---|
11 and 12 | 1 | Limit Switch Ground |
10 | 2 | Reverse Limit Switch |
9 | 3 | Forward Limit Switch |
7 | 4 | Motor Phase B - |
14 | 5 | Motor Phase B + |
8 | 6 | Motor Phase A - |
15 | 7 | Motor Phase A + |
6 | 9 | Reserved for Future Use |
5 | 13 | 5 V |
PAA632 DC Servo Motor Cable
DE15 Male D-Type to DE15 Female D-Type
DE15 Male Pin | DE15 Female Pin | Description |
---|---|---|
1 | 1 | Ground |
2 | 2 | Forward Limit Switch |
3 | 3 | Reverse Limit Switch |
5 | 5 | Motor - |
7 | 7 | Motor + |
10 | 10 | 5 V Encoder Supply |
11 | 11 | Encoder Channel A |
13 | 13 | Encoder Channel B |
PAA614 Stepper Motor Cable
DE15 Male D-Type to DE15 Female D-Type
DE15 Male Pin | DE15 Female Pin | Description |
---|---|---|
1 | 1 | Ground |
2 | 2 | CCW Limit Switch |
3 | 3 | CW Limit Switch |
4 | 4 | Motor Phase B - |
5 | 5 | Motor Phase B + |
6 | 6 | Motor Phase A - |
7 | 7 | Motor Phase A + |
10 | 10 | +5 VDC |
15 | 15 | Ground |
Posted Comments: | |
No Comments Posted |