300 mm Linear Translation Stage, Direct-Drive Brushless Servo Motor

- 300 mm Travel at Speeds Up to 400 mm/s
- Brushless DC Servo Motor
- Bidirectional Repeatability of ±0.25 µm
BBD301
1-Channel Controller
(Sold Separately)
DDSA04
Platform Height Adapter
MJC2
2-Axis Joystick
DDS300
300 mm (11.81") Servo Motor Translation Stage

Please Wait
Key Specificationsa | |
---|---|
Travel Range | 300 mm (11.81") |
Speed (Max) | 400 mm/s |
Acceleration (Max)b | 10 000 mm/s2 |
Bidirectional Repeatability | ±0.25 µm |
Backlashc | N/A |
Horizontal Load Capacity (Max)d | 10.0 kg (22.0 lbs) |
Min Achievable Incremental Movement | 100 nm |
Absolute On-Axis Accuracy | ±7.5 µm |
Cable Length | 2.5 m (8.2') |
Required Controllere | Benchtop: BBD30x; Rackmount: RBD201, MBD602 |
Stage Dimensions (L x W x H) | 500 mm x 130 mm x 50 mm (19.69" x 5.12" x 1.97") |
Motorized Linear Translation Stages | |
---|---|
100 mm | Stepper |
DC Servo | |
150 mm | Stepper |
Stepper with Integrated Controller | |
220 mm | DC Servo |
300 mm | Stepper with Integrated Controller |
DC Servo | |
600 mm | DC Servo |
Optical Delay Line Kits | |
Other Translation Stages |
Features
- 300 mm (11.81") Travel
- High Speeds Up to 400 mm/s
- Low Profile: 50 mm (1.97")
- Integrated, Brushless DC Linear Servo Motor Actuators
- High-Quality, Precision-Engineered Linear Bearings
- Controller Sold Separately (See Table to the Right)
- Accessories Available:
- Height Adapter for 62.5 mm Platform Height
- 2-Axis or 3-Axis Joysticks for Precise Manual Control
Thorlabs' DDS300(/M) Low-Profile, Direct-Drive Translation Stage provides 300 mm of travel with a minimum incremental movement of 100 nm and a maximum speed of 400 mm/s. This stage is ideal for applications that require high speeds and high positioning accuracy, including automated alignment, surface inspection, mapping, and probing.
An innovative, low-profile design with integrated, brushless linear motors eliminates the external housings that create mechanical clash points and impede access to the moving platform. The direct-drive technology removes the need for a leadscrew, eliminating backlash. Internal flexible ducting ensures cables cannot become trapped as the mechanism moves. Twin, precision-grooved linear bearings provide superior rigidity and linearity with excellent on-axis accuracy (±7.5 µm). This backlash-free operation coupled with high-resolution, closed-loop optical feedback ensures a bidirectional repeatability of ±0.25 μm.
Notes:
This stage is not suitable for operation in a vertical (Z-axis) orientation. Additionally, when no power is applied, the mounting platform has very little inertia and is virtually free running. This may make the stage unsuitable for applications where the stage's platform needs to remain in a set position when power is off.
Controller Options
We recommend the BBD30x One-, Two-, or Three-Channel Benchtop Brushless DC Motor Controllers (sold separately below) for this stage. These controllers provide a user-configurable, trapezoidal or S-curve acceleration/deceleration profile that enables fast, smooth positioning without vibration or shock; a comparison between these controllers is available in the Specs tab. They are ideal for motion control applications demanding operation at high speeds (hundreds of mm/s) and high encoder resolution (100 nm). The design incorporates the latest digital and analog techniques as well as high-bandwidth, high-power servo control circuitry. The controllers ship with our Kinesis software for easy integration into an existing system. See below for a brief overview or click here to view the full presentation for these Brushless DC Motor Controllers.
We also offer the RBD201 Rackmount Controller for implementation into a 19" rack and the MBD602 Rackmount Controller Module designed for use with the MMR60x Motion Control 19" Modular Rack System. These controllers are compatible with the DDS300(/M) direct-drive, linear translation stage and allow for customizing more complex systems with multiple motor controls.
Joystick Options
Two optional joysticks are also available for remote positioning applications, the MJC2 Two-Axis Joystick and the MJC3 Three-Axis Joystick. See the presentation below for more details. Please note that in order to control two stages simultaneously, a multi-channel controller is required.
Optical Height Adapter Plate
The DDSA04(/M) riser plate raises the deck height of the stage to 62.5 mm to match that of our NanoMax, MicroBlock, and RollerBlock stages.
Item # | DDS300(/M)a,b | |
---|---|---|
Travel Range | 300 mm (11.81") | |
Speed (Max) | 400 mm/s | |
Acceleration (Max)c | 10 000 mm/s2 | |
Bidirectional Repeatability | ±0.25 µm | |
Backlashd | N/A | |
Encoder Resolution | 50 nm | |
Minimum Achievable Incremental Movement |
100 nm | |
Horizontal Load Capacity (Max)e | 10.0 kg (22.0 lbs) | |
Absolute On-Axis Accuracy | ±7.5 µm | |
Straightness/Flatness | ±4.0 µm | |
Pitch | ±100 µrad | |
Yaw | ±150 µrad | |
Continuous Motor Force | 10.0 N | |
Peak Motor Force (2 s) | 20.0 N | |
Bearing Type | High Rigidity, Recirculating, Precision Linear Bearings |
|
Limit Switches | Magnetic Sensor at Each End of Stage | |
Operating Temperature Rangef | 5 to 40 °C (41 to 104 °F) | |
Motor Type | Brushless DC Linear Motor | |
Cable Length | 2.5 m (8.2') | |
Dimensions | 500 mm x 130 mm x 50 mm (19.69" x 5.12" x 1.97") |
|
Mass (Weight) |
Excluding Cables | 5.9 kg (12.98 lbs) |
Including Cables | 6.14 kg (13.54 lbs) |
Item # | BBD301 | BBD302 | BBD303 |
---|---|---|---|
Number of Channels | 1 | 2 | 3 |
Drive Connector | 8 Pin DIN, Round, Female | ||
Feedback Connector | 15-Pin D-Type, Female | ||
Brushless Continuous Output | 2.5 A per Channel, 5 A Max All-Channel Total Output | ||
Brushless Peak Output | 4.0 A per Channel, 5 A Max All-Channel Total Output | ||
PWM Frequency | 40 kHz | ||
Operating Modes | Position and Velocity | ||
Control Algorithm | 16-Bit Digital PID Servo Loop with Velocity and Acceleration Feedforward |
||
Velocity Profile | Trapezoidal/S-Curve | ||
Position Count | 32 Bit | ||
Position Feedback | Incremental Encoder | ||
Encoder Bandwidth | 2.5 MHz (10 M Counts/sec) | ||
Encoder Supply | 5 V | ||
AUX Control Connector | 37-Pin D-Type Female (User Digital IO, 5 V O/P) | ||
Front Panel Display | 4.3" Full-Color LCD, 480 x 272 Pixels | ||
Input Power Requirements |
250 VA Voltage: 100 to 240 VAC Frequency: 47 to 63 Hz Fuse: 3.15 A |
||
Dimensions (W x D x H) | 199.8 mm x 229.1 mm x 108.8 mm (7.87" x 9.02" x 4.28") |
250.0 mm x 279.1 mm x 108.8 mm (9.84" x 10.99" x 4.28") |
350.0 mm x 279.1 mm x 108.8 mm (13.78" x 10.99" x 4.28") |
Mass (Weight) | 1.20 kg (2.65 lbs) | 1.70 kg (3.75 lbs) | 2.20 kg (4.85 lbs) |
The flying leads are terminated in a male 15-pin D-Type and male 8-pin round DIN connector. Pin details are given below.
Feedback Connector
Motor Drive Connector
Pin | Description | Pin | Description |
---|---|---|---|
1 | Not Used | 9 | Ground |
2 | Ground | 10 | Limit Switch + |
3 | Not Used | 11 | Limit Switch - |
4 | Enc Index - | 12 | Enc Index + |
5 | QB - | 13 | QB + |
6 | QA - | 14 | QA + |
7a | 5 V | 15 | Not Used |
8a | 5 V |
Pin | Description | Pin | Description |
---|---|---|---|
1 | Motor Phase B | 5 | Stage ID |
2 | GND | 6 | Enable |
3a | Unused (Motor Phase D) | 7 | Motor Phase C |
4 | Motor Phase A | 8a | +5 V |
BBD30x Controller Pin Out Descriptions
MOTOR DRIVE
Female DIN Connector
Pin | Description | Pin | Description |
---|---|---|---|
1 | Motor Phase B | 5 | Stage ID |
2 | GND | 6 | Enable |
3a | Unused (Motor Phase D) | 7 | Motor Phase C |
4 | Motor Phase A | 8a | +5 V |
FEEDBACK
Female D-Type Connector
Pin | Description | Pin | Description |
---|---|---|---|
1 | Not Connected | 9 | GND |
2 | GND | 10 | Limit Switch + |
3 | Not Connected | 11 | Limit Switch - |
4 | Index - | 12 | Index + |
5 | QB - | 13 | QB + |
6 | QA - | 14 | QA + |
7a | 5 V | 15 | Not Connected |
8a | 5 V |
HANDSET
Female Mini DIN Connector
Pin | Description | Pin | Description |
---|---|---|---|
1 | RX (Controller Input) |
4 | Supply Voltage for Handset 5 V |
2 | Ground | 5 | TX (Controller Output) |
3 | Ground | 6 | Ground |
AUX I/O
Female D-Type Connector
Pin | Description | Pin | Description | Pin | Description | Pin | Description |
---|---|---|---|---|---|---|---|
1 | RS232 TX | 11 | User Digital O/P 11+ | 21 | +5 V | 31 | User Digital O/P 4+ |
2 | RS232 RX | 12 | User Digital O/P 10- | 22 | User Digital I/P 3 | 32 | User Digital O/P 4- |
3 | Ground | 13 | User Digital O/P 10+ | 23 | User Digital I/P 2 | 33 | User Digital O/P 5+ |
4 | Differential I/P 2+ | 14 | User Digital O/P 9- | 24 | User Digital I/P 1 | 34 | User Digital O/P 5- |
5 | Differential I/P 2- | 15 | User Digital O/P 9+ | 25 | User Digital I/P 0 | 35 | User Digital O/P 6+ |
6 | Differential I/P 1- | 16 | User Digital O/P 8- | 26 | User Digital O/P 0 | 36 | User Digital O/P 6- |
7 | Differential I/P 1+ | 17 | User Digital O/P 8+ | 27 | User Digital O/P 1 | 37 | Ground |
8 | User Digital O/P 12- | 18 | User Digital O/P 7- | 28 | User Digital O/P 2 | - | - |
9 | User Digital O/P 12+ | 19 | User Digital O/P 7+ | 29 | User Digital O/P 3 | ||
10 | User Digital O/P 11- | 20 | +5 V | 30 | Ground |
USB
Type B USB Female
I/O
Female BNC Connector
5 V TTL
Software
Kinesis Version 1.14.50
The Kinesis Software Package, which includes a GUI for control of Thorlabs' Kinesis system controllers.
Also Available:
- Communications Protocol
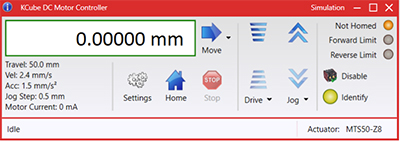
Kinesis GUI Screen
Thorlabs offers the Kinesis® software package to drive our wide range of motion controllers. The software can be used to control devices in the Kinesis family, which covers a wide variety of motion controllers ranging from small, low-powered, single-channel drivers (such as the K-Cubes™) to high-power, multi-channel benchtop units and modular 19" rack nanopositioning systems (the MMR60x Rack System).
The Kinesis Software features .NET controls which can be used by 3rd party developers working in the latest C#, Visual Basic, LabVIEW™, or any .NET compatible languages to create custom applications. Low-level DLL libraries are included for applications not expected to use the .NET framework and APIs are included with each install. A Central Sequence Manager supports integration and synchronization of all Thorlabs motion control hardware.
By providing this common software platform, Thorlabs has ensured that users can mix and match any of our motion control devices in a single application, while only having to learn a single set of software tools. In this way, it is perfectly feasible to combine any of the controllers from single-axis to multi-axis systems and control all from a single, PC-based unified software interface.
The software package allows two methods of usage: graphical user interface (GUI) utilities for direct interaction with and control of the controllers 'out of the box', and a set of programming interfaces that allow custom-integrated positioning and alignment solutions to be easily programmed in the development language of choice.
Legacy Software
Select products are still capable of running the legacy APT™ software package. Information on software compatibility can be found in the product documentation (), and additional details about the APT software can be found here.
Posted Comments: | |
nikki BAI
 (posted 2024-07-25 02:54:18.413) I hope this message finds you well. I am writing to report a technical issue we have encountered Home Failure for Model DDS300M.
We tried to uninstall the Kinesis software and download the APT software for alternative solutions. However, both failed to function normally as expected.
We wonder if you could provide any remote assistance. If there are any further details or documentation required from our end, do not hesitate to ask. spolineni
 (posted 2024-07-30 11:34:09.0) Thank you for reaching out about the issue with the DDS300M model. I will be in touch personally to help troubleshoot and resolve the problem. Vladislovas Cizas
 (posted 2023-09-14 15:27:36.99) The DDS300/M stage connected to BBD302 controller upon homing goes to home position, then returns to the middle and then goes back. In some setups this is very uncomfortable. Is there any way to disable this? (everything up to direct hex command would be perfect). Hai Tran
 (posted 2022-11-15 14:22:56.393) Hi,
I am using Kinesys app with BBD302 controller to control DDS300 linear stage. Been having a hard time talking to it. The stage is not responding to homing. I am running Kinesys 64bit for Windows. Could this be the problem.
Hai JReeder
 (posted 2022-11-23 09:15:09.0) Thank you for your enquiry. In order to troubleshoot this issue, common things to check are the following: Is the channel enabled? Did the stage initialise/was a phase initialisation error received? Does this issue persist when using a different channel of the controller? What colour is the LED on the D-type connector (this indicates the status of the encoder)? What length USB cable are you using (3 m is the recommended maximum length)? I have reached out to you directly to help troubleshoot the issue. Chris Timossi
 (posted 2022-10-07 15:31:02.863) We're using the DDS 300 in combination with the BBD201. I've measured the time it takes between starting the motion with the 'input trigger' and the actual start of the motion as indicated by the 'output trigger' (these trigger
signals are from the Rear Panel USER IO Connector). I setup a relative motion (2mm) on low-to-high transition of the input trigger. I setup the output trigger to low-to-high on 'in motion'. The time I see between the trigger-in and trigger-out signals varies between 25 and 50ms. Can this variation be improved? Is the BBD301 any better? DJayasuriya
 (posted 2022-10-10 10:10:38.0) Thank you for your inquiry, We have got in touch with you directly to resolve your issue. andrea mura
 (posted 2022-05-26 08:01:00.49) Dear Sirs
can these translation stage be controled by means of rs232, GPIB communication protocol ?
Thanks a lot for your replay.
Regards
Andrea Mura DJayasuriya
 (posted 2022-05-27 08:16:53.0) Thank you for your inquiry. Internally the devices use the RS232 communication standard, and the BBD does have exposed RS232 RX and TX pins on the AUX I/O pinout.
If connected over USB, then the FTDI chip receives USB commands from the PC, and "translates" them into serial commands on the internal RX/TX headers. We have also got in touch with you directly. Andrey Kuznetsov
 (posted 2021-05-26 17:59:26.973) Does it work on MacOS? DJayasuriya
 (posted 2021-05-27 08:07:03.0) Thank you for your feed back. Unfortunately we do not currently support MacOS for APT or Kinesis. However with a Mac using boot camp you would be able to run windows. DJayasuriya
 (posted 2021-05-27 08:07:03.0) Thank you for your feed back. Unfortunately we do not currently support MacOS for APT or Kinesis. However with a Mac using boot camp you would be able to run windows. user
 (posted 2019-04-12 03:26:47.54) Hello! Does 300 mm of travel mean that if something were mounted on the center of this stage, it could travel up to 300 mm? Or is that the distance from one end of the path to the other? In other words, does the 300 mm of travel take into account the size of the stage that is moving? rmiron
 (posted 2019-04-12 06:14:10.0) Response from Radu at Thorlabs: 300 mm is the full travel range of the stage, from one end to the other. More specifically, it is the distance between the two end limit switches. Anything mounted on DDS300(/M) can move by 300 mm. The total length of the stage is 500 mm, as is shown in the CAD drawings posted under "Docs", on the main tab. I hope this answers your question. gert
 (posted 2017-06-27 15:43:42.607) Hi,
We want to operate a DDS300-E at a constant velocity in the range of 1 to 10 mm/s. Would it be possible to give us a spec or estimate for the stability of the velocity that can be achieved with this stage?
Thank you,
Gert awebber-date
 (posted 2017-07-03 10:36:45.0) Response from Alex at Thorlabs: When trying to run servo motors at these extremely low velocities there will be some fluctuations in the speed of the stage. We evaluated a DDS220's performance at various set speeds using interferometer when carrying a load of 500g and after 5 million cycles of soak testing,typical velocity fluctuations were ±0.5mm at 10mm/s and ±0.3mm at 1mm/s (with a background noise of 0.006mm/s when stationary). sipos
 (posted 2015-09-25 18:06:31.23) Dera Sir/Madam,
Can this translator be mounted vertically? In this case what is the maximum torque load? GHow does this effect the Pitch/yaw specs?
Best regards
Áron SIPOS rcapehorn
 (posted 2015-09-30 09:40:29.0) Response from Rob at Thorlabs: Unfortunately our brushless stages are not designed to be run vertically. The main problem is that when the stage is powered down there is nothing to hold the moving world in place, so it will drop back to the home position, which could result in damage to the stage.
If you need to use a stage in a vertical configuration then you would need to use something with a lead screw such as the LTS300/M, the main disadvantage with this type of stage is that the maximum velocity will be much slower and also the positional resolution is not as good as with the DDS300/M stage as there is no encoder in the LTS300/M but this it the longest vertical travel stage that Thorlabs can currently offer. |
Motorized Linear Translation Stages
Thorlabs' motorized linear translation stages are offered in a range of maximum travel distances, from a stage with 20 µm of piezo translation to our 600 mm direct drive stage. Many of these stages can be assembled in multi-axis configurations, providing XY or XYZ translation. For fiber coupling applications, please see our multi-axis stages, which offer finer adjustment than our standard motorized translation stages. In addition to motorized linear translation stages, we offer motorized rotation stages and goniometers. We also offer manual translation stages.
Piezo Stages
These stages incorporate piezoelectric elements in a variety of drive mechanisms. ORIC® stages incorporate piezo inertia drives that use "stick-slip" friction properties to obtain extended travel ranges. Our Nanoflex™ translation stages use standard piezo chips along with manual actuators. Elliptec® stages use resonant piezo motors to push and pull the moving platform through resonant elliptical motion. Our LPS710E z-axis stage features a mechanically amplified piezo design and includes a matched controller.
Piezoelectric Stages | ||||
---|---|---|---|---|
Product Family | ORIC® PDXZ1 Closed-Loop 4.5 mm Vertical Stage |
ORIC® PD2 Open-Loop 5 mm Stage |
ORIC® PDX2 Closed-Loop 5 mm Stage |
|
Click Photo to Enlarge |
![]() |
![]() |
![]() |
|
Travel | 4.5 mm | 5 mm | ||
Speed | 1 mm/s (Typ.)a | 10 mm/s (Typ. Max)b | 8 mm/s (Typ.)c | |
Drive Type | Piezoelectric Inertia Drive | |||
Possible Axis Configurations | Z | X, XY, XYZ | ||
Mounting Surface Size |
45.0 mm x 42.0 mm | 13 mm x 13 mm | ||
Additional Details |
Piezoelectric Stages | ||||||
---|---|---|---|---|---|---|
Product Family | ORIC® PD1 Open-Loop 20 mm Stage |
ORIC® PD1D Open-Loop 20 mm Monolithic XY Stage |
ORIC® PDX1 Closed-Loop 20 mm Stage |
ORIC® PDX1A Closed-Loop 20 mm Stage Low-Profile |
ORIC® PD3 Open-Loop 50 mm Stage |
|
Click Photo to Enlarge |
![]() |
![]() |
![]() |
![]() |
![]() |
|
Travel | 20 mm | 50 mm | ||||
Speed | 3 mm/s (Typ. Max)a | 20 mm/s (Typ. Max)c | 10 mm/s (Typ.)b | 10 mm/sd | ||
Drive Type | Piezoelectric Inertia Drive | |||||
Possible Axis Configurations | X, XY, XYZ | XY, XYZ | X, XY, XYZ | X, XY, XYZ | X, XY, XYZ | |
Mounting Surface Size |
30 mm x 30 mm | 80 mm x 30 mm | ||||
Additional Details |
Piezoelectric Stages | ||||||
---|---|---|---|---|---|---|
Product Family | Nanoflex™ 20 µm Stage with 5 mm Actuator |
Nanoflex™ 25 µm Stage with 1.5 mm Actuator |
Elliptec® 28 mm Stage | Elliptec® 60 mm Stage | LPS710E 1.1 mm Vertical Stage | |
Click Photo to Enlarge |
![]() |
![]() |
![]() |
![]() |
![]() |
|
Travel | 20 µm + 5 mm Manual | 25 µm + 1.5 mm Manual | 28 mm | 60.0 mm | 1.1 mm | |
Maximum Velocity | - | 180 mm/s | 90 mm/s | - | ||
Drive Type | Piezo with Manual Actuator | Resonant Piezoelectric Motor | Amplified Piezo | |||
Possible Axis Configurations | X, XY, XYZ | X | Z | |||
Mounting Surface Size | 75 mm x 75 mm | 30 mm x 30 mm | 15 mm x 15 mm | 21 mm x 21 mm | ||
Additional Details |
Stepper Motor Stages
These translation stages feature removable or integrated stepper motors and long travel ranges up to 300 mm. Many of these stages either have integrated multi-axis capability (PLSXY) or can be assembled into multi-axis configurations (PLSX, LNR Series, NRT Series, and LTS Series stages). The MLJ150 stage also offers high load capacity vertical translation.
Stepper Motor Stages | |||||
---|---|---|---|---|---|
Product Family | PLSX with and without PLST(/M) Top Plate 1" Stage |
PLSXY with and without PLST(/M) Top Plate 1" Stage |
LNR Series 25 mm Stage |
LNR Series 50 mm Stage |
|
Click Photo to Enlarge |
![]() |
![]() |
![]() |
![]() |
|
Travel | 1" | 25 mm | 50 mm | ||
Maximum Velocity | 7.0 mm/s | 2.0 mm/s | 50 mm/s | ||
Possible Axis Configurations |
X, XY | X, XY, XYZ | X, XY, XYZ | ||
Mounting Surface Size |
3" x 3" | 60 mm x 60 mm | 100 mm x 100 mm | ||
Additional Details |
Stepper Motor Stages | ||||||
---|---|---|---|---|---|---|
Product Family | NRT Series 100 mm Stage |
NRT Series 150 mm Stage |
LTS Series 150 mm Stage |
LTS Series 300 mm Stage |
MLJ250 50 mm Vertical Stage |
|
Click Photo to Enlarge |
![]() |
![]() |
![]() |
![]() |
![]() |
|
Travel | 100 mm | 150 mm | 150 mm | 300 mm | 50 mm | |
Maximum Velocity | 30 mm/s | 50 mm/s | 3.0 mm/s | |||
Possible Axis Configurations |
X, XY, XYZ | X, XY, XYZ | Z | |||
Mounting Surface Size |
84 mm x 84 mm | 100 mm x 90 mm | 148 mm x 131 mm | |||
Additional Details |
DC Servo Motor Stages
Thorlabs offers linear translation stages with removable or integrated DC servo motors. These stages feature low profiles and many can be assembled in multi-axis configurations.
DC Servo Motor Stages | ||||
---|---|---|---|---|
Product Family | MT Series 12 mm Stages |
PT Series 25 mm Stages |
MTS Series 25 mm Stage |
MTS Series 50 mm Stage |
Click Photo to Enlarge |
![]() |
![]() |
![]() |
![]() |
Travel | 12 mm | 25 mm | 25 mm | 50 mm |
Maximum Velocity | 2.6 mm/s | 2.4 mm/s | ||
Possible Axis Configurations | X, XY, XYZ | X, XY, XYZ | ||
Mounting Surface Size |
61 mm x 61 mm | 101.6 mm x 76.2 mm | 43 mm x 43 mm | |
Additional Details |
DC Servo Motor Stages | ||||
---|---|---|---|---|
Product Family | M30 Series 30 mm Stage |
M30 Series 30 mm Monolithic XY Stage |
M150 Series 150 mm XY Stage |
KVS30 30 mm Vertical Stage |
Click Photo to Enlarge |
![]() |
![]() |
![]() |
![]() |
Travel | 30 mm | 150 mm | 30 mm | |
Maximum Velocity | 2.4 mm/s | X-Axis: 170 mm/s Y-Axis: 230 mm/s |
8.0 mm/s | |
Possible Axis Configurations | X, Z | XY, XZ | XY | Z |
Mounting Surface Size |
115 mm x 115 mm | 272.4 mm x 272.4 mm | 116.2 mm x 116.2 mm | |
Additional Details |
Direct Drive Stages
These low-profile stages feature integrated brushless DC servo motors for high speed translation with zero backlash. When no power is applied, the platforms of these stages have very little inertia and are virtually free running. Hence these stages may not be suitable for applications where the stage's platform needs to remain in a set position when the power is off. We do not recommend mounting these stages vertically.
Direct Drive Stages | |||||
---|---|---|---|---|---|
Product Family | DDS Series 50 mm Stage |
DDS Series 100 mm Stage |
DDS Series 220 mm Stage |
DDS Series 300 mm Stage |
DDS Series 600 mm Stage |
Click Photo to Enlarge |
![]() |
![]() |
![]() |
![]() |
![]() |
Travel | 50 mm | 100 mm | 220 mm | 300 mm | 600 mm |
Maximum Velocity | 500 mm/s | 300 mm/s | 400 mm/s | 400 mm/s | |
Possible Axis Configurations | X, XY | X, XY | X | X | |
Mounting Surface Size | 60 mm x 52 mm | 88 mm x 88 mm | 120 mm x 120 mm | ||
Additional Details |

Characterized by high-speed translation and high positional accuracy, the DDS300(/M) stage is well-suited for surface mapping and characterization applications where there is a need to move a camera or probe at constant velocity while simultaneously capturing data. Very precise, fine positioning and control can be achieved with the associated MJC2 or MJC3 joystick option (available below)
Notes:
This stage is not suitable for operation in a vertical (Z-axis) orientation. Additionally, when no power is applied, the mounting platform has very little inertia and is virtually free running. This may make the stage unsuitable for applications where the stage's platform needs to remain in a set position when power is off.

We recommend using our BBD Series Brushless DC Servo Motor Controllers with the stages above, selecting the controller with the required number of channels. If using a standalone stage, the BBD301 can be used; if also using a MJC2 joystick, the BBD302 is recommended. The BBD303 3-Channel Controller can be used for applications requiring additional accessories; all three channels can be controlled via the MJC3 joystick.
With a user-configurable, S-curve acceleration/deceleration profile that enables fast, smooth positioning without vibration or shock, these controllers are ideal for motion control applications demanding operation at high speeds (hundreds of mm/s) and high encoder resolution. Incorporating the latest digital and analog techniques as well as high-bandwidth, high-power servo control circuitry, each BBD series controller is designed to drive brushless DC servo motor products with continuous output currents of up to 2.5 A (Item # BBD301) or 5 A (Item #s BBD302 and BBD303).
These DC servo controllers are supported by Thorlabs' Kinesis® control and programming interface, enabling easy integration into automated motion control applications. For greater flexibility, both a USB and RS232 computer interface is provided, and automated PC control of the stage is supported with the supplied software development kit (SDK). The fully documented SDK supports all major development languages running on Windows and comes in the form of a conventional dynamic link library (DLL).
USB connectivity provides easy plug-and-play PC operation. Multiple units can be connected to a single PC via standard USB hub technology for multi-axis motion control applications. Combining this feature with our user-friendly software allows the user to program and carry out complex move sequences in a short space of time. For more information, please see the full Brushless DC Servo Motor Controller presentation.

- High-Reliability Joysticks Utilizing USB HID Protocol
- 2-Axis or 3-Axis Control Via a Joystick Knob
- Two Different Modes for Fast or High Precision Moves
- Speed Dial for Sensitivity Adjustment
- Allows Remote Manual Control
- Can be Reprogrammed using a PC
- Ergonomic Design
The MJC2 and MJC3 Joysticks have been designed for microscope users and provide intuitive, tactile, manual positioning of a stage. The joysticks feature a two-axis joystick knob for XY control or a three-axis joystick knob for XYZ control, respectively. Both joystick knobs can be moved left or right and up or down, with the MJC3 joystick knob also twisting clockwise or counterclockwise for third axis control. A push button to switch between fast or high-precision movement and a speed dial to fine tune speed control are also integrated into the joysticks. In most applications, the default parameter settings saved within the controller allow the joystick to be used out-of-the-box with no need for further setup. This operation mode eliminates the need for connection to a host PC and allows for true remote operation. Parameter settings can also be reprogrammed and saved to a paired controller using a PC, allowing the controller to be disconnected from the computer and remote operation continued.
The MJC2 and MJC3 Joysticks are compatible with our Benchtop Brushless DC Servo Controllers, Rack-Mounted Brushless DC Servo Controller, Rack-Mounted Brushless DC Servo Controller Module, and Stepper Motor Controllers. The joysticks have both a Mini-DIN and a USB Type-C port and are each shipped complete with two cables, a 6-pin Mini-DIN plug to plug cable and a USB 3.1 Type-A to Type-C cable, for use with these controllers as well as setups utilizing the USB HID class. For more information about configuring and setting up the joystick over USB HID, please see the manual by clicking on the red Docs icon () below.

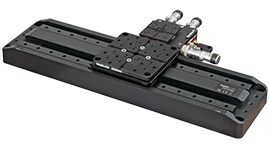
Click to Enlarge
The deck height of the DDS300 Stage is matched to the MAX311D 3-Axis Stage using the DDSA04 Riser Plate.
- Height Adapter to Match the 62.5 mm Deck Height on Our NanoMax300, MicroBlock, and RollerBlock Stages
- Resulting Overall Optical Height: 75.0 mm (When Used with Thorlabs' Tongue and Groove Accessories)
- Array of 48 Tapped Holes (16 of Each): 1/4"-20 (M6), 8-32 (M4), and 4-40 (M3)
The DDSA04(/M) Optical Height Adapter is designed to raise the deck height of the DDS300(/M) stage to 62.5 mm, which is the same as our NanoMax 300, MicroBlock, and RollerBlock stages. This allows our range of tongue and groove optical accessories to be used with the DDS300(/M) stage and gives an optical axis height of 75.0 mm. The plate is fixed to the moving platform of the stage using four 1/4"-20 x 3/8" (M6 x 10 mm) cap screws (not supplied).